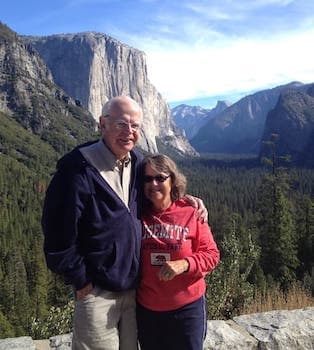
Curated with aloha by
Ted Mooney, P.E. RET
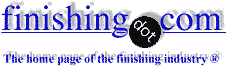
The authoritative public forum
for Metal Finishing 1989-2025
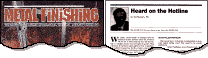
-----
Effect on dimensions of anodizing/hardcoating and stripping & re-anodizing
Q. Someone has the answer to this question ... so please help me so my curiosity is satisfied. In sulfuric anodizing, what percentage of the anodic film is build up. In other words if the part dimension is .250 in diameter and I anodize at 12 ASF for 60 minutes, what will the diameter be after.
Theoretically if I anodize at 12 ASF for 60 minutes, the anodic film would be .8 mil. but I need to understand what part of that .8 mil is making the part larger. And, I am told the alloy of aluminum makes a difference. Anyone help on this question? Thank you, thank you and thank you again for any and all responses.
Todd Huehn- Fridley, Minnesota
2000
A. General rule of thumb, 50% in and 50% out. Although, I don't believe this is an exact science. I'm sure James will correct me if I'm wrong (I meant that as a compliment to your knowledge, James). Your diameter should be .2508, if its an outside diameter.
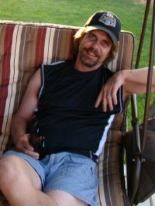
Marc Green
anodizer - Boise, Idaho
2000
A. Todd,
Alloy type does make a difference in the buildup to penetration ratio. Type III Sulfuric anodize (hardcoat) --.8 mils typically is 50% penetration and 50% buildup per surface which means that your dia. would be .2508. Type II sulfuric anodize the ratio varies more, i.e. 6061 will give you approx. 80% penetration and 20% buildup or .2532^.2503 diameter.
Aluminum 2000, 5000, 7000 series all vary as to the ratio. One method I use to determine what % is buildup, I measure the parts before and after, using my thickness gage to I measure the amount of anodize I applied, take the before and after size divide it by two and subtract it from my thickness per side and that tells me what my penetration and buildup is, this method may seem obvious but when I have to hold a tight tolerance, I don't assume and it's helpful on repeat orders. In short there are a lot of variables that can effect buildup and penetration, including the different alloys.
I'm sure that if I too am not correct, my friend James, will set me straight. Hope this helps.
Lamar Jackson- FWB, Florida
2000
2000
? I can't figure where Lamar's second example of .2532 comes from. Even if you plated .0008 on a .250 diameter, with zero penetration, you would only end up with 0.2516. I don't have the time to do the math, at 4:30 on a sunny Friday afternoon, but if the 80% penetration is correct, it sounds to me that the final diameter would be less than .250. I have a problem believing 80% penetration with 6061, as the coating on 6061 is usually very tight and dense, even with Type II, but I can't prove my intuition since I don't have an anodizing tank near by.
Of course, all this assumes that .250 is actually .2500, and not .2504 or .2496. We have to watch how we play with significant digits here. I bring this up because sometimes we assume that incoming parts are uniform, but if we don't know the initial tolerances as well as the actual dimension, a nominal .250 diameter can very well be .2496 to .2504 if the tolerance is ± .0004, meaning with the 50:50 rule anodized parts could vary from .2504 to .2512, and that is assuming that coating thickness is exactly .0008 on every part. You can get into some really sticky situations, particularly if a customer is uneducated on how this all works. It is especially true with hardcoating, so hardcoaters must check and recheck their math several times.
Phil Johnson
- Madison Heights, Michigan
I stand corrected; the diameter is .2503 approx., however with type II, buildup is rarely a real concern. Phil, thanks for pointing out my error, it's always good to have someone double checking the numbers.
- FWB, Florida
2000
A. I really do not know. I always assumed that I got less effective build up out of alloys with higher amounts of acid soluble metals like copper and magnesium. I also assumed that the ratio changed slightly. Never investigated actual numbers as most customers wanted a given final dimension. I agree with Lamar that keeping good records is the best way to have it come out right the next time.
James Watts- Navarre, Florida
2000
A. One more thing that may need to be addressed in this discussion is the amount of material one removes during the etch process prior to anodizing. Some anodizers may remove as much as .001" prior to anodizing.
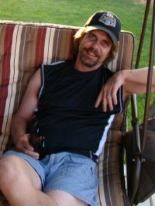
Marc Green
anodizer - Boise, Idaho
2000
Multiple threads merged: please forgive chronology errors and repetition 🙂
Stripping hardcoat anodizing with no dimensional changes
Q. I want to know whether it is possible to strip-off hardcoat from an aluminum roll without change in dimension, since that piece has to be re-coated with hard anodizing. How can it be done?
Muhammad Irfan Rafiq- Gujranwala, Pakistan.
2002
A. Hi, Muhammad.
It is possible to strip hardcoat anodizing in chromic-phosphoric acid without attacking the substrate--see letters 2776 and 3397. But that does not mean there will be no dimension change. Rather, even if you don't consume any aluminum in etching, when one anodizes .002" thick, roughly .001" of the aluminum substrate was consumed in building the anodized film (per the discussion above); so when you strip the part it will be .001" smaller than it was before you anodized it.
Good luck.
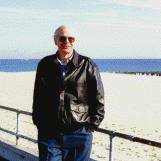
Ted Mooney, P.E.
Striving to live Aloha
finishing.com - Pine Beach, New Jersey
2002
Q. I am with the Society of Automotive Engineers at my university. We are building a "Mini-Baja". It's essentially a large go-cart with full suspension. Anyways ...
My sub-team has finish machining our gearbox for the drivetrain. It was made from some 1" thick aluminum T6 6061. I wanted to have it anodized, but I wanted to know if the anodizing process affects the tolerances/hole sizes where we want to press our bearings into and other dimensions. If so, are they any other solutions to finish our gearbox?
Thanks,
Chad RensopME student - Orlando, Florida, USA
2004
2004
A. Your frame can be chromate conversion coated for corrosion resistance without affecting dimensions, but that's not really as good as anodizing in some ways. You should probably allow for the growth in anodizing, which is about 50 percent of the specified thickness of the anodizing, because the other half is "penetration". Typical sulfuric acid anodizing is probably about 0.0002"-0.0005" thick (even slightly thicker if you want to color it black because the more saturated the color, the more dye you need to absorb into the anodizing pores, so the thicker you need the anodize layer to hold it).
Anodizing can have a large effect on fatigue strength, which is also a good topic for engineering students to study.
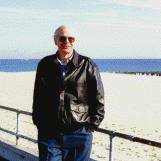
Ted Mooney, P.E.
Striving to live Aloha
finishing.com - Pine Beach, New Jersey
Multiple threads merged: please forgive chronology errors and repetition 🙂
Q. I want to know whether its possible to strip sulfuric anodizing off aluminum and not change the dimension of the parts. If so how can it be done?
Kenneth Mullinsanodizing plating shop - Woodside, New York
2004
2004
A. No, it's not possible, Kenneth. The anodizing is not a finish that is added on top of aluminum like paint or electroplating. Rather, it is a conversion process whereby aluminum from the item combines with oxygen to form aluminum oxide. If you strip that aluminum oxide, even with zero attack on bare aluminum, the part will be smaller than when you started because some of the aluminum was consumed in generating the aluminum oxide.
For rough purposes, half of the anodizing thickness is consumed aluminum. So if you have a plate that is 1" thick and you want to anodize it on both sides to .002" anodizing thickness, it will be 1.002" thick after you anodize it and .998" thick if you strip the anodizing with no material loss. Good luck.
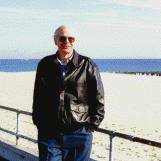
Ted Mooney, P.E.
Striving to live Aloha
finishing.com - Pine Beach, New Jersey
Dimensional changes when stripping and re-anodizing
Q. Regarding Hard Anodizing process, is it viable to strip an existing part of it's hard anodize coating and re-anodizing the same part again? I understand that it will take off a layer of the material, is it possible to coat it back so that the required dimensions can be held?
Edward Layengineering - Kuala Lumpur, Wilayah Persekutuan, Malaysia
2004
A. Hi Edward. In the real world it probably won't work; in the theoretical world it is not impossible.
Say the initial thickness requirement was for .001" of anodizing on a 1" radius (2" diameter) cylinder. In rough numbers, .0005" of aluminum would be consumed in the building of that film thickness, so the radius after anodizing the first time would be 1" minus .0005" plus .001", equals 1.005". If you strip this with a chromic phosphoric acid mix so you lose lose no raw aluminum, it will be .9995" radius after stripping. If you now apply .002" of anodizing on the second try, you'll consume .001" of aluminum in the process. So the radius will be .9995 minus .001" plus .002", equals 1.005". Theoretically possible :-)
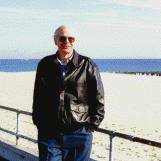
Ted Mooney, P.E.
Striving to live Aloha
finishing.com - Pine Beach, New Jersey
Can anodized aluminum be stripped and re-anodized
Q. Quick question for you.
Is it true a piece of aluminum can only be hard anodized once? We hone aluminum ram bodies and get them hard anodized so that they meet the dimensional requirements called out for in the OEM manual. Someone in the industry mentioned to me that the hard anodizing can only be done one time. After the unit that we hard anodized comes in for service again should we discard it?
Manager - Surrey, b.c. Canada
October 14, 2010
A. Hi, Steve. In practice it's almost always true, due to dimensional considerations. Hard anodizing is considered to be about .002" thick. In building a .002" hard anodizing layer, you will have consumed about .001" of aluminum from the substrate. When you strip the old anodizing, even if you lose no raw aluminum, the substrate will thus be .001" inches smaller than it started. You would have to anodize .004" thick to make up the difference and that thickness almost surely won't be practical.
Regards,
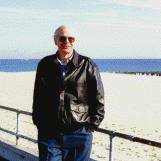
Ted Mooney, P.E.
Striving to live Aloha
finishing.com - Pine Beach, New Jersey
Ok Ted,
Thank you very much. It all makes sense now!
- Surrey, b.c. Canada
October 15, 2010
Q. I had some parts made by a local jobshop, a 1" diameter x 2" long pin made from 2024 aluminum, 0.257 dia. hole running lengthwise through the center of the part. I specified on my drawing that the diameter be +.000 to -.005 diameter, and that it be hard coated. I was told by the plater that hardcoat would build the diameter of the part from .002 to .003.
The parts arrived and all were -.0008 to -.0010 small on diameter. Not only that, but the .257 hole was as big as .263, and tapered over the length of the pin.
I trust this job shop. I don't believe they would have sent badly undersized parts to the plater. Did the plater "cook" the parts too long, or did I get bad information about what to expect? Did the 2024 have something to do with it?
I also noticed that there is some cracking of the finish. I did not expect that.
- Tully, New York
March 8, 2013
A. Hi Leo. As you see, we've appended your inquiry to a thread which discusses the effect of anodizing (and stripping and re-anodizing) on the dimensions of parts. It does sound like these parts may have been stripped a few times by the anodizer, upsetting the dimensions. We probably don't have enough info to solve the problem, but we do have enough to help you get your arms around it. And here are some other things to consider:
- 2024 is one of the most difficult alloys to successfully anodize because only the aluminum content can be anodized, whereas 2024 has a lot of other garbage in it, including over 4% copper. The job would be easier in an alloy like 6061 if that suited your needs.
- Anodizing IDs can be very difficult, especially when they are deep. Holes of 0.257" dia. in pins of 2" long, comprise very deep . . . and I doubt that such parts can be successfully anodized in run-of-the-mill fashion; rather, they probably require custom jigging with solution propelled through the holes, and perhaps with a center cathode.
Again, I don't have the facts, but if I were asked to guess the most probable case, the anodizer priced the job for routine processing, tried that a few times and failed a few times.
Regards,
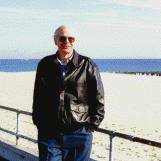
Ted Mooney, P.E.
Striving to live Aloha
finishing.com - Pine Beach, New Jersey
March 9, 2013
Thank you. Everything you say makes sense. And here I thought I was helping the jobshop by specifying an easier to machine aluminum. I've asked that he re-run the job with 6061. I really don't care if the inside of the .257 hole gets plated. I was concerned about the outside.
- Tully, New York
March 11, 2013
Using go/no-go thread gages on hardcoated threads
Q. We specify 15/16 x 20 UNEF 2B threads on a part that is type 3 anodized/hardcoated, 0.001" buildup and 0.001" penetration. The threads are cut 0.005" over mean pitch diameter to compensate for the plating buildup.
Will the go/no-go plug thread gages work after plating, or is there some issue with plating threads that will not allow standard thread plug gages to be used? I have seen some mention that no-go gauges will not work after plating.
Geoff WeinertProduct Designer - Fairfield, New Jersey
August 21, 2015
A. You should be fine with that if the anodizing is done as specified.
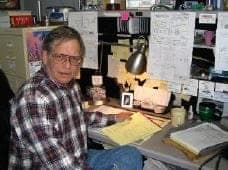
Jeffrey Holmes, CEF
Spartanburg, South Carolina
August 21, 2015
Q. Jeffrey
Thanks for the response. Is controlling the thickness of hardcoat on threads any more difficult if you are doing it to a large amount of identical parts at one time as apposed to just one part.
Geoffrey
- Fairfield, New Jersey, USA
August 25, 2015
A. Threads should NEVER be anodized. On ANY sharp edge the coating penetrates half in half out, that leaves solid aluminum oxide on the edge, which readily breaks off when you screw in the opposing thread. Threads should be masked.
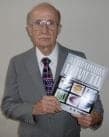
Robert H Probert
Robert H Probert Technical Services

Garner, North Carolina
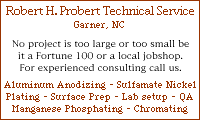
August 25, 2015
Q. I want to re anodise some parts purely because they are the wrong colour but I need to keep dimensions as close to what they now.
They are 6061 parts anodised red. Its looks like typical thin anodising as opposed to a solid looking hard coat.
If I strip the parts but hard coat anodise them will they be close to where they were? OR is there a way to un seal the existing anodise and remove the red dye and dye it blue a re seal?
- Aylesbury, Buckinghamshire, England
May 13, 2016
A. Hi Dominic,
Since it is a color anodized part, it would have been 'clear anodized' prior to the dye stage, probably to about 15-20 microns thick (I am just estimating here ... you have to check it with a coating meter).
Best way to go about it would be, to measure all the dimensions as they are now, and then measure them again after stripping the anodized coating. The difference will give you an idea as to how much you have to coat back - remember, anodizing builds up half penetration and half growth.
Yes, you can hardcoat anodize back to your required size, easily even up to 80 - 100 microns on a 6061 alloy.
Threaded holes may have to be retapped, as strict control is not possible.
- Belgaum, Karnataka, India
June 2, 2016

Q, A, or Comment on THIS thread -or- Start a NEW Thread