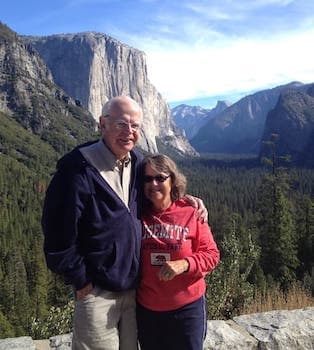
Curated with aloha by
Ted Mooney, P.E. RET
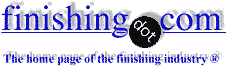
The authoritative public forum
for Metal Finishing 1989-2025
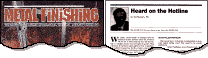
-----
Process to achieve uniform coating
2004
Q. Dear Sir,
We have Mini plating plant and being used for plating applications in the area of microelectronics. Recently we face thickness non-uniformity during Gold plating on Ceramic substrates of size 1X1 inch. Can you please suggest us any changes required in our process to achieve uniform coatings within ± 10% on one inch area.
Details are as follows.
1.Tank size: Polypropylene type, 6"X12"X6"
2.Anodes: 2 Nos., Platinized Ti, 5"X4"
3.Type: Cyanide based acid type gold bath
4.Bath parameters:
(i)pH : 3.7-4.1
(ii)Temperature : 60°C
(iii)Volume : 4 lit.
(iv) Gold content : 8-10 gm/lit
5.Process parameters :
(i)Sample : Sputtered Gold on both faces of Alumina substrates
(1X1X0.025")
(ii) DC Plating current : 60mA at 1.5V
(iv)Agitation : Single rod agitation with 14 rpm motor connected to cathode
(iii) Plating time : 45 minutes (for achieving 5.5µ thickness)
(iv) Loading : One substrate at the centre of cathode rod facing both anodes kept at end (Distance between Anodes 12 inches)
6.Observations: Thickness as measured by Betascope indicates 5.5µ at the centre of 1"X1" substrates. At edges it is 7.5µ; Edge build up of 2µ. Allowable thickness variation is 1µ on entire 1 inch area of substrate. Adhesion of coatings is excellent.
Kindly suggest whether control of anode surface area and position, or temperature of bath would help to achieve the required uniformity of metallization i.e 5.5µ ±10%.
Regards,
D. Balasubramanyam- India
A. Try using a robber: a piece of wire surrounding the edges of the square you are trying to plate. The wire must be cathodic and keep the wire equidistant, close and in the same plane to the edges of the flat square you are plating. This should mollify the changes in current density across the square you are plating.
Michael LanesPlating Manager - Los Angeles, California, USA
2004
Q, A, or Comment on THIS thread -or- Start a NEW Thread