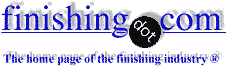
-----
Zinc plating thickness vs. salt spray resistance

< Prev. page (You're on the last page)
Q. Dear Sir,
We have been taking trials of Acid Zinc Plating and trivalent Blue Passivation with top coat on Low carbon steel components. The area of the component is 0.5 dm2. The component is just simply a Bush. SST requirement for this component is 48 hrs without black spots. We have tried external commercial platers also. They are also unable to meet 48 hours of SST. We are trying in-house to achieve the result but unfortunately white rust is forming within 24 hrs. How to overcome this issue? How to achieve the results of 48 hours? Customer is very particular about Trivalent Blue passivation.
Most of the failure samples reveal white rust formation on the HCD area. The plating time is 25 minutes (9 to 12 micron thickness) with 8 pcs and passivation time is 30 secs and top coat time is 15 secs. We have checked the chromating film deposition. It was found to be 50 to 62 nm. When we increase the timing, the corners of the Bush has started stripping in the passivation solution. That is the reason why, we are unable to increase the passivation timing. Kindly request you to provide me the suitable solution. We are under tremendous pressure to take a output and show a consistent result.
MUTHU SWAMY- Chennai, Tamil Nadu, India
January 12, 2017
Zinc plating is failing 96 hour salt spray. Will a higher carbon substrate help?
Q. Sir,
For zinc plating we are conducting Neutral salt spray test for each batch as per ISO 9227. For each batch test is passed for 48 hours. If I check 6 month old zinc plated product is there any chances of getting white rust for same salt spray test for 48 hours?
- Bangalore, India
February 23, 2017
Q. Thanks very much for the response on letter 35197 Ted.
I have another query. We are currently using EN1A steel material. The equivalent is AISI 1213. This is a low carbon steel, with carbon 0.07 to 0.15%. We carried out salt spray testing for components made with this steel, plated with FeZn8 CrIII and found that it had developed brown rust within 96 hours.
We are also debating whether moving to a slightly higher carbon content steel will increase the affinity to Zn plating and thus improve corrosion resistance. Information regarding this would be highly appreciated.
- Mysore India
April 25, 2017
A. Hi Mihir. No, a higher carbon steel will not deter the rusting, and will only make the plating somewhat more difficult.
Repeating from an earlier comment on the thread which we added your inquiry to: You will pass the 96 hour salt spray test "if the substrate was properly mechanically prepared; and it was properly cleaned and activated; and it was properly zinc plated; and it was properly trivalent chromated with a proprietary chromate and the topcoat recommended by the supplier; and the shape of the component is such that it can get proper plating coverage, and the process is under control."
Luck and Regards,
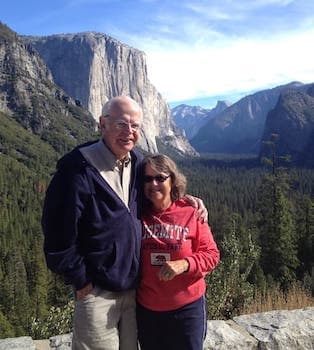
Ted Mooney, P.E. RET
Striving to live Aloha
finishing.com - Pine Beach, New Jersey
Thank you Ted for your comments. Appreciate it. I will check with my supplier team and review their process of plating.
Triton Valves Ltd. - Mysore India
? Hi,
Can you tell us what type of zinc solution you use? Is it acid, cyanide or alkaline? Also the chromate you use. This will help to give you a answer on your question.
Regards
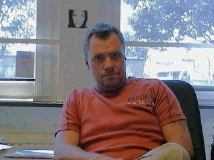
Anders Sundman
4th Generation Surface Engineering
Consultant - Arvika,
Sweden
Q. Hi,
We are facing rusting issue in few of our plated parts which are directly exposed to sunlight and rain. We are specifying Zinc coating of 12 microns. How much of salt spray test requirement we should communicate to Supplier to avoid this?
- Chandigarh, Punjab, India
May 11, 2017
A. Hi Deepak. Although 96 hours would be a good answer, remember that salt spray testing is for the purpose of keeping the process under control, not predicting real-world life. So, what is your evidence that 12 microns would be enough if the process were under good control?
In other words, are you sure that the plated parts which rusted are seeing the same exposure conditions as the parts which didn't? Are you sure that your exposure conditions are not "very severe" (requiring 25 microns of plating)? Is there any exposure to road salt, lawn fertilizer, pressure treated wood, or other chemicals? Is the problem red rust or white rust? Thanks!
Regards,
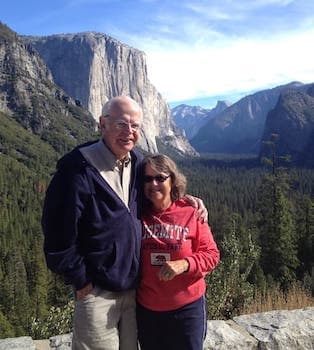
Ted Mooney, P.E. RET
Striving to live Aloha
finishing.com - Pine Beach, New Jersey
Q. The machine is parked in open weather that is exposed to sunlight, Rain and other environmental degradation factors.
Deepak Bathla [returning]- Chandigarh,Punjab , India
A. Hi again, Deepak. Due to the very close timing, it's not clear to me whether your reply was in response to my posting or just coincided with it. But I think the ball is still in your court :-)
Regards,
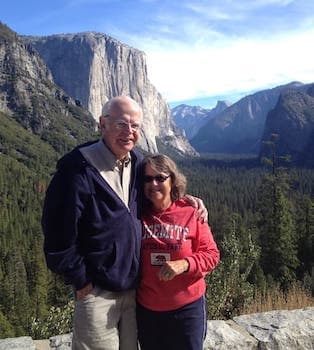
Ted Mooney, P.E. RET
Striving to live Aloha
finishing.com - Pine Beach, New Jersey
Trivalent or hexavalent chromate for more salt spray hours?
Q. Which type of plating is comparatively stronger to salt spray testing, Trivalent or Hexavalent?
Jayant KurundkarRobertshaw controls Pvt. Ltd. - Pune, India
February 5, 2018
A. Hi Jayant. If you read literature from 30 years ago, it will say that hexavalent is much better, which it was. But today's modern proprietary trivalent chromates are the equal of hexavalent chromates (in salt spray testing at least).
Regards,
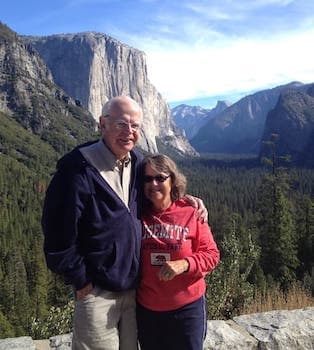
Ted Mooney, P.E. RET
Striving to live Aloha
finishing.com - Pine Beach, New Jersey
Q. I seem to be struggling to get any information on how long zinc plating itself not including passivate lasts in salt spray to red rust. Is there any general information out there for it? E.g., 25 microns lasts "x amount" of hours to red rust?
Many thanks in advance
Andrew
- United Kingdom
February 16, 2018
A. Hi Andrew. For my own part, in a career of 50+ years in electroplating, I don't recall even once seeing zinc electroplating which wasn't chromated, but Tom Rochester suggests that you look at ASTM B695 for that answer. Good luck.
Regards,
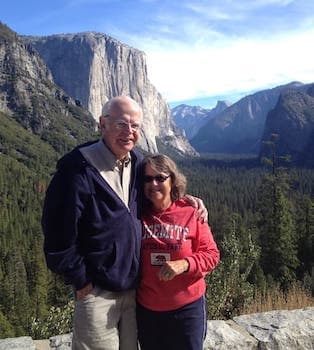
Ted Mooney, P.E. RET
Striving to live Aloha
finishing.com - Pine Beach, New Jersey
Salt spray test for Hydrogen De embrittled part
Q. Will Hydrogen De embrittled part withstand the Salt spray test of 144 hours with Zinc yellow passivation. Coating thickness of 8 microns.
Anand Shanmugam- Coimbatore, India
March 1, 2018
![]() |
A. The best answer to this question can be obtained experimentally. If the article, prior to de-embrittlement, would have passed these requirements and has a trivalent passivate, then it would likely pass after de-embrittlement as well. If it has a hexavalent passivate, and just barely passed before salt spray, it would likely fail. But facts trounce theory and opinion. ![]() Tom Rochester CTO - Jackson, Michigan, USA Plating Systems & Technologies, Inc. ![]() ![]() A. Hi Anand, TEL - N FERRARIS - Cañuelas, Buenos Aires, Argentina |
Q. In Internal salt spray testing we have found red rust in 144 hours in respect to [required] 264 hours.
Plating type - Zinc plating with yellow passivation.
Plating thickness observed -- 9 micron on same batch part in respect to requirement of 12 micron minimum.
Testing condition - As per ISO 9227
Part Type - M10 -Screw
Photo & test Reports - Refer below
So can you please share the probable causes of above issue, accordingly I am planning to visit at supplier to validate the same.
Regards,
- Bawal Haryana, India
March 11, 2018
A. Hi Ansh. I think the failed thickness check rather than the failed salt spray test is the heart of this matter!
If the screws are supposed to be plated to 12 micron thickness, but the supplier is not plating them for a long enough time to achieve that requirement, something is terribly wrong and must be fixed before you can proceed. The vendor perhaps justifies themself by believing that your spec is incorrect or poorly written ... and they may be right or wrong. But whether they agree to plate to your spec or you agree to change the spec, STEP 1 is that the plating thickness must conform to the spec; if it doesn't, everything else is nothing but nonsense :-)
Regards,
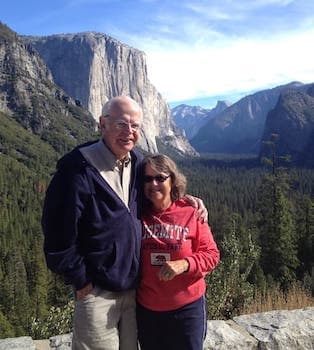
Ted Mooney, P.E. RET
Striving to live Aloha
finishing.com - Pine Beach, New Jersey
A. Hi Ansh. As Ted said, first verify why the bolts have less thickness than specified. It could be that your supplier didn't know the spec (it wouldn't be my first), mistakes in plating time or current, low zinc/low anode surface, low bath conductivity (potassium/ammonia?)...
Not knowing your supplier, you can make many assumptions, but what you have is a part not meeting your spec (12 microns minimum, 264 hour of SST without corrosion of base metal). Go with that and listen to what they say :)
Best of luck!
TEL - N FERRARIS - Cañuelas, Buenos Aires, Argentina
Q. Hello. Can we achieve 480 Hrs of salt spray life with 8 Micron coating thickness?
If yes, with which process?
Kindly guide.
Rishi Laser Ltd - Pune, Maharashtra, India
February 5, 2019
A. Hi Pankaj. I doubt it. But at the least, 480 hours sounds equivalent to very severe exposure (25 microns) rather than moderate (8 microns) exposure. Can you tell us what spec you intend to evaluate the salt spray life according to, and give us some background info? Thanks.
Regards,
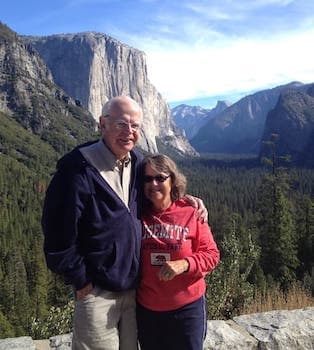
Ted Mooney, P.E. RET
Striving to live Aloha
finishing.com - Pine Beach, New Jersey
Q. Hello Mr Mooney.
Thanks a lot for your reply. Actually we had an inquiry from our customer who is dealing in aerial work platforms which are working in environment with moderate salinity & expecting a life cycle of 5 to 15 years (C4). Customer is specifying Zn-Ni plating and 8 Micron plating thickness.
Our supplier is confident of achieving it, I just want to confirm it.
Rishi Laser Ltd - Pune, Maharashtra, India
A. Hi again Pankaj. Thanks for the additional info. The other people on this thread have been discussing zinc plating; zinc-nickel plating is a different process and is much more corrosion resistant. On topic 28851, Asif Nurie asserts that 500-1000 hours is possible, but some other posters reported failure within that time frame. The way to confirm the ability to comply is to plate sample parts and test them for 480 hours, then evaluate them in accord with some specific specification.
The problem remains that the results will depend not only on the plating process but on the shape of the part, its substrate material, its surface finish, etc. To "teach to the test", designing to salt spray hours instead of real life is a mistake; but to try to do so while ignoring the actual parts is impossible. Good luck.
Regards,
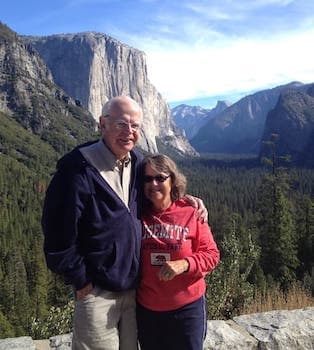
Ted Mooney, P.E. RET
Striving to live Aloha
finishing.com - Pine Beach, New Jersey
⇦ Tip: Readers want to learn from your situation;
so some readers skip abstract questions.
Q. if we deposit 1 micron thickness on parts then How much life will achieve?
Umesh W [surname deleted for privacy by Editor]QA - Aurangabad, Maharashtra, India
April 13, 2019
A. Probably zero, cousin Umesh, because it will probably not accept chromate properly, and may rust in the time before & after salt spray exposure. I've never heard of anyone trying to use only 1 micron of zinc plating. 5 microns is specified for "mild" service conditions.
Regards,
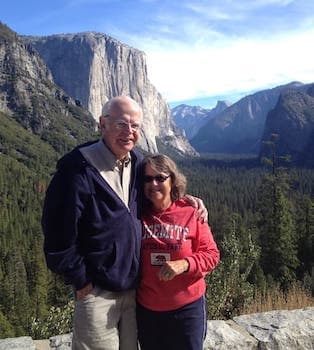
Ted Mooney, P.E. RET
Striving to live Aloha
finishing.com - Pine Beach, New Jersey
A. Hi Umesh,
I'm not sure what life 1 micron will achieve but your business life expectancy with your customer will be zilch if he finds out you were asking.. :)
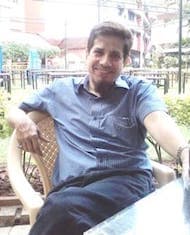
Khozem Vahaanwala
Saify Ind

Bengaluru, India
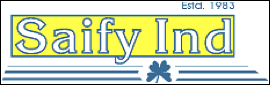
Yay Khozem!
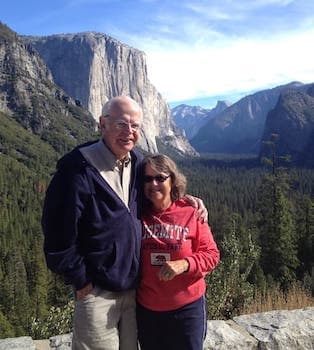
Ted Mooney, P.E. RET
Striving to live Aloha
finishing.com - Pine Beach, New Jersey
Q. I have a customer that is requiring a Zinc Black .0005" plating. My question is does .0005" provide more corrosion protection than .0002?
Andy HanksFastener Distribution - Erie Pennsylvania
June 28, 2019
A. Hi Andy. Yes! .0002" (5 microns) is for "mild" service per ASTM B633 and related specs, and .0005" (13 microns) is for "severe" service. In between is.0003" (8 microns) for "moderate" service.
Regards,
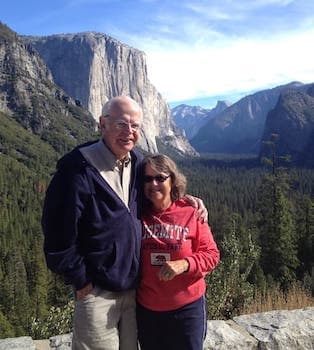
Ted Mooney, P.E. RET
Striving to live Aloha
finishing.com - Pine Beach, New Jersey
Q. Hi I am from a metal stamping company in Malaysia.
I have a customer making snow tire chain wear plates using Boron Steel from SABB Boron 22. After stamping it goes thru Oil Quenching + Blue Zinc Plating (did not specified thickness) + Tempering.
Is it possible to achieve "No white rust after 200 hours in 5% NaCl atmosphere per salt test standards ISO 9227.
Regards,
Lawrence
Y&L Metal components Sdn Bhd - Balakong Malaysia
June 28, 2019
A. Hi Lawrence. If you can plate them, you should be able to get 200 hours with a very good chromate conversion coating. But I think you might want "clear" rather than "blue", and I'm not sure you will be able to plate oil quenched parts unless you have a very good cleaning cycle. Further, this application sounds like "very severe" service", such that zinc plating thickness should be specified rather than being satisfied simply with a white rust salt spray test. Good luck.
Regards,
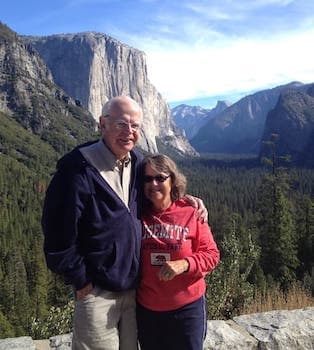
Ted Mooney, P.E. RET
Striving to live Aloha
finishing.com - Pine Beach, New Jersey
Q. We want coated brackets with zinc. Brackets can be welded or bolted, generally L shaped. We require brackets for severe environment conditions. So I want to ask about the thickness of coating and salt spray test durations for white and red rust, we should prefer?
Dhanaj Singh Panwar- Bhopal, India
August 1, 2019
A. Hi Dhanaj. Per ASTM B633 and some related industry standards, "severe" service should have 13 microns, 'very severe' (bold atmospheres, cleaners, saline solutions, denting, scratching and abrasion) 25 microns. It seems to me that automotive and some others tend to use alloy platings like zinc-nickel of the next thicker thickness instead (8 microns of alloy plating for the severe stuff and 5 microns for the moderate).
192 or 200 hours to white rust seems to be pretty typical these days. As for red rust, I'd concentrate on the thickness rather than the hours to red rust since salt spray testing tells us little to nothing about real-life endurance of zinc coatings because the corrosion mechanism is fundamentally different.
Regards,
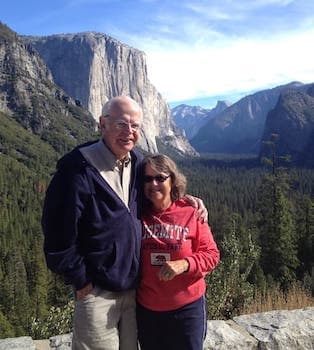
Ted Mooney, P.E. RET
Striving to live Aloha
finishing.com - Pine Beach, New Jersey
Q. My question is: is there any relation ship between plating thickness (any type) and salt spray hours or any other factor also contribute for salt spray hours.
Sateesh .nnash - Bangalore, Karnataka, India
August 22, 2019
A. Hi Sateesh. You are asking an extremely broad abstract question which is probably more appropriate for a book, or at least a chapter, rather than a brief public forum response :-)
The short answer is, no, the salt spray resistance is generally not directly proportional to the thickness. In zinc and zinc alloy plating the quality of the chromate conversion coating is probably a bigger factor in salt spray resistance than the thickness of the zinc plating. But zinc is anodic to iron so there is at least some degree of proportionality between plating thickness and salt spray hours because the zinc plating will gradually dissolve.
But in other types of plating, where the plating layer is cathodic to the substrate, such as nickel plating on steel, the 'porosity' of the plating is far more important than the thickness because corrosion begins as soon as the salt solution reaches the steel substrate. As a general rule, increasing the thickness of the plating probably decreases the porosity, but a properly applied fairly thin plating layer may be less porous and pin-holed than a poorly applied thicker layer.
Please introduce yourself and your particular situation; people can often help you with a fairly specific problem but, much as they may wish to, they can't condense decades of experience into a few paragraphs for you :-)
Regards,
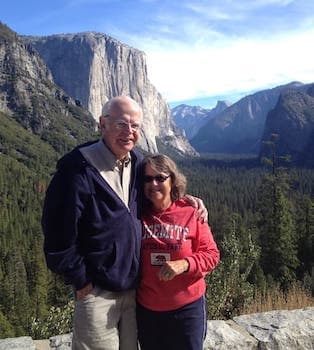
Ted Mooney, P.E. RET
Striving to live Aloha
finishing.com - Pine Beach, New Jersey
Q. Our client want that surface treatment MFZn2-C and SST required 240 Hrs. Is it possible? If yes, what is the procedure?
Jamal Yousuf- Karachi, Sindh, Pakistan
September 25, 2019
A. Hi Jamal. What company or international standards body are you referring to with that spec? Different automobile companies have specs that may use similar abbreviations and which look sort of the same but which are not the same specs. In some specs the number after MFZn is the thickness in microns, but I doubt that that's the case here; it's perhaps a Honda spec where the "2" means exposure class 2, not 2 microns.
Under ideal conditions, yes, a well controlled zinc plating process can probably deliver 240 hours, quite possibly more. Does the specification mention 240 hours or is that only mentioned on the drawing? Thanks.
Regards,
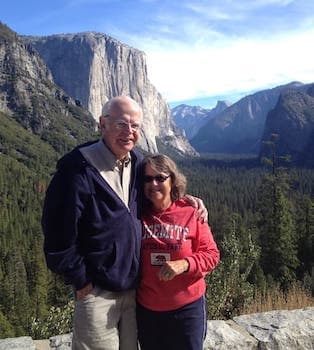
Ted Mooney, P.E. RET
Striving to live Aloha
finishing.com - Pine Beach, New Jersey
WSS-M1P85-B2 zinc plating is failing 120 hour salt spray
Q. Hello, Jason here from the automotive sector.
I have a door hinge of stamped steel (EN 10149-2-S420MC) that is treated per WSS-M1P85-B2 (electrolytic zinc 8µm thin film passivate).
I am seeing red rust around 50-60 hours; spec is 120 hours.
The film build using electrometer is above requirement at ~13µm. Documentation from the supplier is good.
I'm traveling to the plater to [investigate] root cause. What should I be looking for?
My plan is to review the spec and process with the plater. Then place parts in the salt spray chamber (marked) and watch them on-site for three days.
Any insight would be appreciated.
Advanced Quality Engineer - Auburn Hills, Michigan (USA)
October 28, 2019
A. Hi Jason. I think you should try to track one batch of parts from the receiving dock to the salt spray cabinet. Very often the flow sheets, no matter how carefully written, don't describe what really happens. "Walking the line" often immediately reveals what is wrong ("No good decision was ever made from a swivel chair" -- General George S. Patton).
Some thoughts: The spec probably calls for no "white rust" until 120 hours, let alone "red rust". The high salt spray hours bragged about by the process vendors always apply to ideal shaped parts and after excellent mechanical preparation. Has the plater made any comments about "design for plating"? Are the hinges properly deburred? Are these "hinges" pre-assembled, such that capillary action may mean that acids are drawn in from early process steps are carried through the process? Is there a particular area on the hinge which rusts first? Has the plater recently changed chromate suppliers?
Regards,
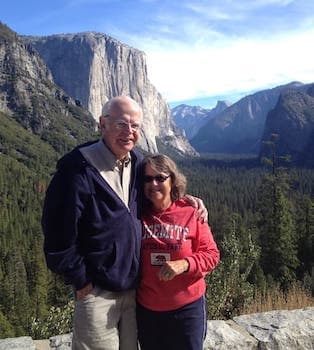
Ted Mooney, P.E. RET
Striving to live Aloha
finishing.com - Pine Beach, New Jersey
Q. We have bung inserts made from EN19 steel and our supplier provides trivalent coating of 9-11 microns thickness. The bung inserts are exposed to hard water and we see rusting on finished components after use as well as when stored at 40% RH. Does the grade of steel make any difference for trivalent coating? If we change steel to IS 20162 (hot rolled structural steel)? Or should we go for Ni-Cr plating? The bung comes in contact with propane gas.
Pradeep KamatComposite LPG Cylinders - Mumbai, India
November 14, 2019
Q. As far as the Zinc spec. ASTM B633 Type III SC 3 (FE/ZN 13) is concerned, what Does the SC mean?
Raymond Haase- Hauppauge, New York USA
December 16, 2019
A. Hi Raymond. SC 3 means Service Condition 3, "Severe Service", and requires 13 microns of plating thickness. Please never quote to plate to a spec without the spec in hand :-)
Regards,
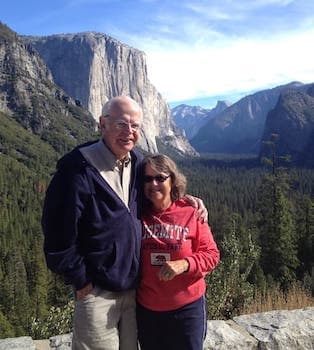
Ted Mooney, P.E. RET
Striving to live Aloha
finishing.com - Pine Beach, New Jersey
Q. Hi Anyone please clarify me about, Salt spray acceptance criteria? We have done Zinc plating coupon 96 hrs salt spray test. Got result with no rust, but coating peels off. We found on some surfaces the coating was completely removed. Can we accept it?
Guhan Veeramani- UAE Abu Dhabi
August 9, 2020
A. Hi Guhan. You ask "Can we accept it?" but haven't introduced yourself as purchaser, test lab, or plating shop
- If you are a testing lab, I think due diligence and product stewardship demands that you do your best to convince the client to not accept the parts.
- If you are the plating shop, I think you should admit that the components are NOT satisfactorily plated.
What usually actually answers most questions is the plating specification. Someone should have, and possibly did, write or reference a specific plating specification for the plating contract. Please give us that specification or specification number and we can probably point to a specific line which defines such plating as unsatisfactory. Good luck!
Luck & Regards!
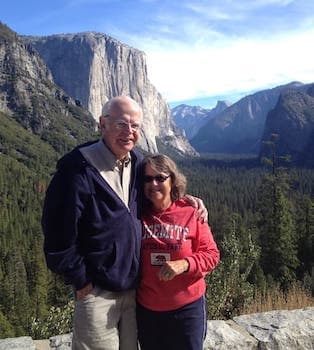
Ted Mooney, P.E. RET
Striving to live Aloha
finishing.com - Pine Beach, New Jersey
Q. Sir
I am Guhan and working as a Quality supervisor at Oil field manufacture company. We are doing now ELECTRODEPOSITED ZINC PLATING ON CARBON AND LOW ALLOY STEELS validation process and currently doing salt spray test (96 hrs). We had sample coupon with minimum 8 Micron (Zinc plating thickness) at before salt spray test stage. And after salt spray test we got good surface without any rusting formed. But Zinc thickness fell into the 6.2 Microns. Can we accept it? Is Zinc thickness also a consideration to have acceptance?
- Abu Dhabi
A. Hi Guhan. The part is probably satisfactory; you are almost surely not supposed to recheck minimum thickness after an accelerated corrosion test, but again we must ask for a specification or specification number before anyone can say for sure whether the part is satisfactory. For example, you say "without any rusting", but do you mean red rust or are you including white rust ... and which one does the spec say you must resist for 96 hours? Salt water isn't terribly abrasive so it's hard to imagine losing 1.8 µm of plating without generating any white rust. And does the spec actually say that testing one sample part is enough, or might it demand a specific sampling plan? You cannot assert that the quality meets the requirements without a specification number telling you what those quality requirements are.
If you received just a vague requirement like "8 µ Zn + yellow chromate, must pass 96 hour salt spray", then you should pick a spec or write a spec that answers such questions because without it you cannot have quality assurance. For example, what happens if you're out sick next week and your replacement views things differently?
Luck & Regards,
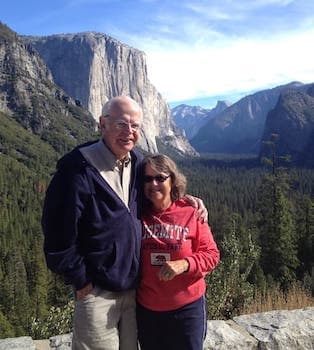
Ted Mooney, P.E. RET
Striving to live Aloha
finishing.com - Pine Beach, New Jersey
Q. Adding to above my question, Electrodeposited zinc plating on carbon and low alloy steels in accordance with the latest revision of ASTM B633 and Salt Spray Test per ASTM B117 for a minimum of 96 hours and sample coupon we selected 3 ea.
guhan veeramani [returning]- Abu Dhabi
Q. Hi to all,
I am Gopinath working as a head of quality dept. in metal shop field. We are making wire mesh cable tray with mild steel base and finish of electro zinc plating Fe/Zn12. It is complete alkaline base zinc plating, blue passivation (Trivalent).
After complete zinc electroplating finishing we did Salt spray on samples for test 550 hrs as per ASTM B117. Here our question is: sample passed 550 hrs SST without any white rust or red rust; only observed black stain marks on the sample.
We have checked mass of zinc coating of the sample the result is 15 microns. How did this material pass SST at 550 hrs sample have only 15 microns?
Our sample is 4.5mm dia wiremesh
- THANE maharastra, India
January 6, 2021
A. Hi Gopinath. That does seem like outstanding performance, but I guess the answer is that you did a good job of applying a very good trivalent chromate and sealer onto a very good zinc plating layer on a very well prepared substrate. But as for "only 15 microns" that is not thin zinc plating, it's more than enough for 'severe' service.
If you are implying a suspicion that the salt spray test was conducted incorrectly, please try to be a bit more explicit and specific. Thanks!
Luck & Regards,
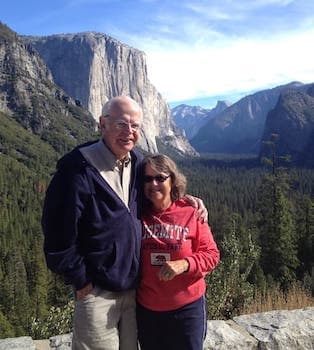
Ted Mooney, P.E. RET
Striving to live Aloha
finishing.com - Pine Beach, New Jersey
Q. Hi,
Our product goes into harsh environment where it is required to meet 500 hours of salt fog testing. The parts are machined rod & springs of around 8 to 10 mm dia.
What top coating is preferred on top of Zinc Trivalent chromate? and what thickness is required for meeting this spec?
- CHENNAI Tamil Nadu
April 7, 2021
A. Hi Venkat. I would suggest that you read this whole thread because several points have been made repeatedly here ...
1. Although Tom Rochester notes below that ASTM B695 for mechanical plating has a table of thickness vs. salt spray hours, I don't think you should be selecting the thickness based on desired salt spray results, but based on the environment. If the environment is 'harsh', that sounds like what the specs call 'severe service', and the thickness should be 13 microns.
2. What standard will be used to evaluate whether the parts passed? And does it call for no red rust or for no white rust?
3. When looking for 500 hours salt spray, you might want to follow the example of the automotive companies and specify zinc alloy plating (zinc-iron, zinc-cobalt, zinc-nickel, or tin-zinc) rather than plain zinc. The thicker an electroplating is, the less ductile it tends to be; so for use on springs, a thinner zinc alloy electroplate may be preferable to a thicker zinc electroplate. But considering that steel springs are made of hardened materials subject to hydrogen embrittlement, you might also consider mechanical plating in lieu of electroplating.
Sorry, I am not familiar with attempting to apply a home-brew generic top coat onto trivalent chromate. In my experience, the top coat has always been purchased from the trivalent chromate supplier.
Luck & Regards,
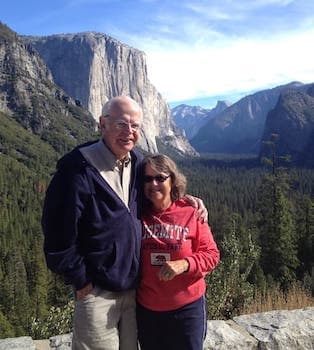
Ted Mooney, P.E. RET
Striving to live Aloha
finishing.com - Pine Beach, New Jersey
A. A trivalent conversion requires a sealer. This is a must.


Sara Michaeli
Tel-Aviv-Yafo, Israel
Q. For zinc plating with yellow passivation of small bolts required salt spray test life the part fails within 48 hr for white corrosion and red rust developed within 120 hrs. Salt spray corrosion resistance is low. What process check should we do to identify area of improvement in process?
Santosh dagademanager - PUNE, India
July 3, 2021
A. Hi Santosh. What plating specification are you attempting to adhere to? What process are you using? I presume it's barrel plating, but cyanide, acid, or alkaline non-cyanide. What chromate are you applying ... is it a proprietary trivalent with proprietary topcoat?
Luck & Regards,
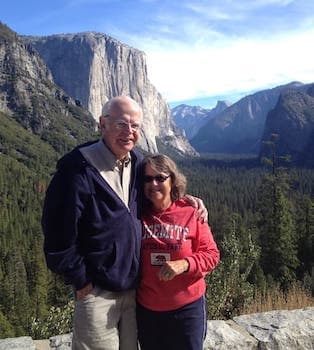
Ted Mooney, P.E. RET
Striving to live Aloha
finishing.com - Pine Beach, New Jersey
Q. MY QUESTION IS :- MY CUSTOMER IS ASKING FOR 96 HRS WHITE RUST AND 120 RED RUST, AT WHAT MIN MICRON OF ZINC PLATING BLUE PASSIVATION IS THIS ACHIEVABLE.
2ND IN DRAWING IT IS MENTIONED MIN 7 MICRONS.
PLEASE SUGGEST ON URGENT BASIS.
- Faridabad, India
January 19, 2022
A. Hi ANUBHAV. The 7µ minimum thickness specified should get you the salt spray hours you are looking for if the trivalent chromate and top coat are high quality, and assuming that the entire process is well controlled.
Proper thickness is supposed to be determined by real world exposure conditions; for example, according to ASTM B633: 5µ for mild exposure, 8µ for moderate, and 12-13µ for severe.
The purpose of salt spray testing of zinc plating is to give you a quick heads-up if you are losing control of the process; you are supposed to design parts for real world exposure conditions not to achieve salt-spray hours.
Luck & Regards,
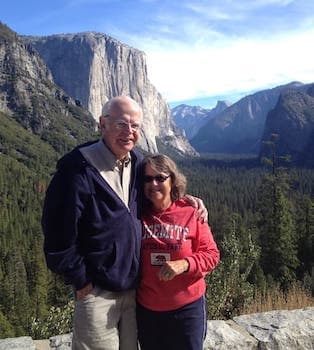
Ted Mooney, P.E. RET
Striving to live Aloha
finishing.com - Pine Beach, New Jersey
Q. Hi,
We are doing doing 5 microns Zinc electroplating and yellow chromate passivation on PTFE Bearings which will have PTFE laminated on galvanized cold rolled steel base. Customer (Hyundai/KIA-MS611-15 standard) requirement is 72 hrs of white rust and 168 hrs of red rust which we are not able to achieve. Our part is getting white rust at only around 24 hours. Though we increase the plating thickness, we are not able to achieve required SST hours.
Is it possible to achieve 72 hrs of white rust and 168 hrs of red rust on our parts with 5 microns considering our base metal?
Employee - India, Karnataka, Bangalore
January 20, 2022
A. Hi Sathyaraj. Apparently Hyundai thinks so :-)
I don't mean that cynically or satirically, but rather that they apparently feel that if the metal has received proper mechanical pretreatment and proper chemical pretreatment, and the zinc plating, chromating, and post-treatment are well controlled it is possible with that zinc plating thickness. Of course cyanide zinc and alkaline non-cyanide zinc give more uniform thickness than acid zinc and you may have thin spots.
Luck & Regards,
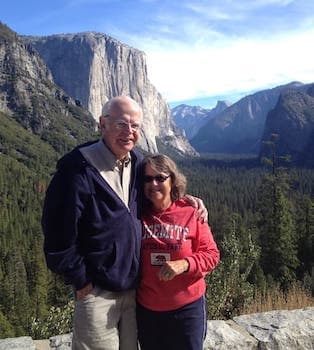
Ted Mooney, P.E. RET
Striving to live Aloha
finishing.com - Pine Beach, New Jersey
Q. Do you have any data which shows the difference between SST Qualification of 96 hours for cyanide zinc plating vs acid zinc plating?
I would also like to know if Cyanide zinc or acid zinc which would qualify for better results in Salt spray test
Plating business - Karachi, Pakistan
March 2, 2022
A. Hi Ammar. Cyanide zinc and alkaline non-cyanide zinc offer better covering power and throwing power (evenness of plating thickness) than acid zinc, so there should be less problem with uncovered or minimally covered areas, and theoretically better salt spray performance. But realistically, 96 hours should not be difficult for any modern zinc plating and chromate conversion coating; 96 hours tests the chromate more than the zinc plating.
We've said a thousand times that design decisions should not be based on optimizing salt spray time; instead, salt spray testing is an early warning that a process is going out of control. I guess as long as people keep saying that that is what they want to do, we'll have to keep repeating that it's not a good idea :-)
As one obvious example, if we make decisions about choice of finish based on salt spray hours we'd never pick hot dip galvanizing; it's expensive, and a much cheaper good paint job will beat it in salt spray hours. But in actuality there is no other finish which even begins to approach hot dip galvanizing in real-world longevity; when away from the sea, three-quarters of a century or even a full century without any maintenance is not unheard of.
Luck & Regards,
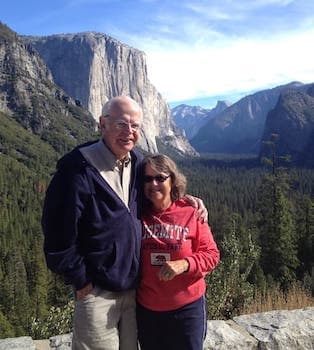
Ted Mooney, P.E. RET
Striving to live Aloha
finishing.com - Pine Beach, New Jersey
Q. Ted,
Thank you for your prompt reply.
Salt spray test qualification and coating thickness are the 2 top measures by which parts are approved or rejected.
Such is the reality of the business world and requirements from quality assurance teams. Since that is the benchmark set by them. Therefore achieving SST qualification is crucial and repeatedly brought up.
How crucial is the dipping time in passivating zinc plated parts play in improving the chromating layer and qualification in SST test?.
What is the max temperature that zinc plated parts should be heated at to provide the best curing and passivation results.
Regards,
Plating business - Karachi, Pakistan
March 2, 2022
A. Hi Ammar. I understand what is common; if someone else in the supply chain has told you to focus your process line toward maximizing salt spray hours rather than actual performance, then my message was directed to them :-)
In any case, as previously mentioned, 96 hours should not be any challenge for a properly operating line; it has been the minimum standard for more than 60 years, and most process vendors claim far more.
These days trivalent chromate conversion coating should probably be done, and that involves not just the chromate conversion step, but a sealing step. Usually the immersion time is not critical, but is in the general range of 45 seconds to twice that; the process supplier will offer a technical data sheet specifying the optimum and acceptable range for immersion time.
Hexavalent chromate drying temperature should not exceed 140 °F (60 °C); I have heard that a bit higher is okay for trivalent chromates, but why go higher if you don't have to.
Luck & Regards,
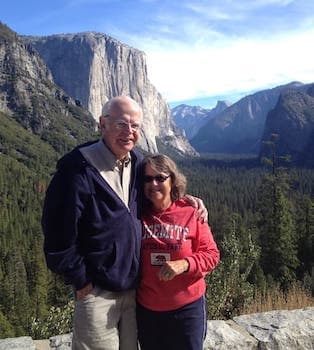
Ted Mooney, P.E. RET
Striving to live Aloha
finishing.com - Pine Beach, New Jersey
on eBay or Amazon
or AbeBooks
(affil link)
Q. Hello,
My client requires 240 hours to Red rust and 90 hours to white rust with Zinc White passivation. Use is in the automobile sector.
Can anyone advise if it is possible to achieve and how many microns are required to be deposit over the same?
- Gurugram/ Haryana, India
February 23, 2023
A. Hi Gaurav,
We appended your inquiry to a thread where the question has been answered quite exhaustively. However, I would add the following in answer to your specific question:
• You should be plating to a specification not just a thickness. Pick a spec, ASTM B695 or ISO 2081 for example, get it and see if it clearly specifies the finish you want.
• I think you will find that even the minimum thickness in the spec, probably 5 µm, will deliver the salt spray hours you need if the substrate is properly pretreated, properly plated, and properly chromated with a high-quality proprietary chromate.
• I believe you'll also find that you are supposed to select the zinc thickness based on service condition, not salt spray hours. 5 µm may pass the salt spray test but that thickness is for mild exposure conditions and 8 µm is more appropriate for auto parts.
Luck & Regards,
Ted Mooney, P.E. RET
Striving to live Aloha
finishing.com - Pine Beach, New Jersey
Q, A, or Comment on THIS thread -or- Start a NEW Thread