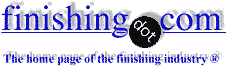
-----
Hard Anodizing 7050 Alloy
We are curently having difficulty hard anodizing 7050 alloy in the T73511 temper. The specific confiiguration of the part is a 1/4" plate with two (2) 1" slots milled in the plate. The exterior of the plate coats without any difficulty, but the inside of the slots have a white looking deposit. A microsection of the slot reveals 0.0003" coating.
The bath contains 12.5 oz/gal sulfuric Acid, 2.5 oz/gal oxalic acid and is chilled to 32°F. We ramp the current slowly to prevent burning and when we reach 30 volts, we hold at 30 volts for 1.5 hours to obtain our coating thickness. We are not experiencing any problems with any other alloys (6061, 7075, A356), only 7050.
Ken Minksaircraft company - Wichita, Kansas
1999
Hi Ken, there are a few questions that might help. Do you know the current density for the parts in question as run? Does the powdery coating continue to rub off in the slots, ie; an amorphous coating, or is it a surface condition? Has the racking been evaluated for current carrying capacity? Are you racking in the slots? What agitation conditions do you have around the parts where they are located in the tank? Have you run other 7050 parts, if so what are the surface conditions there? Is there a "bullseye" appearance around the slots? My first guess would be that localized overheating is taking place and causing a fast dissolution rate at those surfaces causing an amorphous coating. Especially since you are only seeing a .0003 inch thickness after an hour and a half of anodizing. If that is the case evaluating the racking electrical current carrying capacity and a slower ramp, with increased agitation may help. 7050 should anodize satisfactorily.
Ward Barcafer, CEFaerospace - Wichita, Kansas
1999
A problem like this is hard to pinpoint without seeing the part. Ward's comments should be highly beneficial. I also wondered about the possibility of mechanical finshing residues in the slots that are not being removed in the cleaning process. This is assuming that the face of the plate is sanded, polished, or has some other mechanical finish. Another possibility is that air bubbles from air agitation could be hanging up in the slots.
I don't know if this has anything to do with your problem, but I noted that you are ramping to a given voltage and holding it there. If hardcoat anodizers out there were willing to discuss their processing secrets, I would bet that the vast majority would tell you would get a much better hardcoat if you anodized at constant current density. Hardcoat differs from conventional anodizing in that it has a very tight pore structure and much higher coating density. The high coating density is produced by anodizing at much higher current densities than conventional anodizing. Higher current densities means a lot more heat being generated, which is why you need to maintain cold temperatures. Understand that as the coating thickness builds up, the surface resistance climbs, and the voltage will climb if current is held constant. If voltage is held constant, current density drops off, and the rate of coating build up slows down, which is why you need an hour and a half in the tank to get your desired thickness. I consider 90 minutes in the tank as excessive, and it just may be leading to dissolution in the slots. I doubt if the hard coat is very hard, and may even be powdery as Ward suggests..
You didn't say what coating thickness you expect on the parts, but if you anodize at 30-36 asf, you should be able to achieve 2 mils in 40-50 minutes. As Ward says, rack design for hardcoat is very important, and it will be more critical if you do anodize by current control. If you are anodizing to 2 mils, your rectifier necessarily should have at least 75 volts capacity, and preferably 100 volts, with ramping capabilities, of course, and ability to control by current as well as by voltage. Of the alloys you mention, the rise in voltage will be highest in 6061, because its hardcoat will be superior (i.e. harder, denser) to that on the other alloys.
Phil Johnson
- Madison Heights, Michigan
1999
Q, A, or Comment on THIS thread -or- Start a NEW Thread