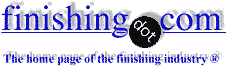
-----
ALUMINUM ANODIZING PARAMETERS?
I am interested in having extruded 6020-T6511 aluminum hard coated to MIL-A-8625 / MIL-PRF-8625 [⇦ this spec on DLA], Type III. I'd like to have the thickness at 0.101mm (0.004") but I'm told by a few hard coaters that this material, which is symilar to 6061-T6, will reach a saturation point at 0.051mm thick (0.002"). I'd appreciate it if someone could help me out here. I could use the 0.101mm thickness for post processing the surfaces to achieve a specific surface finish value (Ra 0.2 micrometers) but I don't know if what I'm asking for is unreasonable.
Blaine Boydautomotive - Monroe, Michigan, USA
1999
What happens in anodizing is that the surface is converted to non-conductive aluminum oxide, so that the process is indeed self-limiting as you have been told. However, the higher the anodizing voltage, the thicker this insulating coating can be before it self-limits.
.002" ± .0005 is considered the minimum thickness for hardcoat, and this requires 40-45 volts; .004" is considered about the maximum practical thickness for conventional approaches and chemistries.
So it could be that the vendors you have spoken to have 40-50 volts rectifiers and cannot give you a thicker coating, but by continued shopping you might find that someone has higher voltage rectifiers installed and can obtain, or at least approach, the .004" thickness you are seeking.
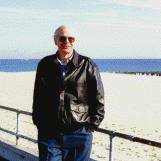
Ted Mooney, P.E.
Striving to live Aloha
finishing.com - Pine Beach, New Jersey
1999
1999
Most hard anodizing specifications use 51um (2.0 mils) as the default target thickness. To lower costs,less hardcoating thickness can be specified with resultant lower performance. Higher thicknesses (up to 250um) can also be specified but at a much higher cost and only marginally better performance. Typically these extra thick hardcoatings are used only for salvage of out of tolerance parts. Normal practice for sizing and finishing after hardcoat is to specify a coating thicknes of 55 to 65um. This allows enough extra material for finishing operations, while still maintaining a final hardcoat thickness of 51um. Experienced hardcoaters should be able to achieve these thicknesses using normal processing techniques. Free extra tip: In general, the better the surface finish is before hardcoating the better it will be after. But do not use methods which move rather than remove metal such as burnishing.
Chris Jurey, Past-President IHAALuke Engineering & Mfg. Co. Inc.

Wadsworth, Ohio
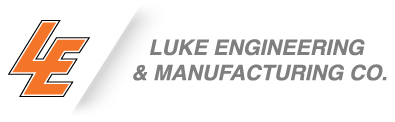
Q, A, or Comment on THIS thread -or- Start a NEW Thread