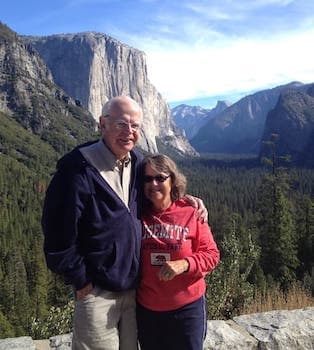
Curated with aloha by
Ted Mooney, P.E. RET
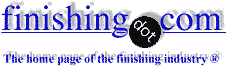
The authoritative public forum
for Metal Finishing 1989-2025
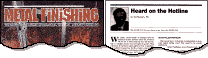
-----
Electroless copper plating on non conductive plastics
Q. I am looking for advice on electroless copper plating on non conductive material. We are having problems with blistering of the spray on products that were recommended to us i.e., silver spray and spray copper from a hobby plating site. We are trying to chrome plate these parts. Any help would be great. Thank you
Jim RodgersAuto parts restoration - Philadelphia, Pennsylvania, USA
2004
A. Here's the thing Jim: there's hobby plating on plastics (perhaps suitable for interior mild-exposure) and then there's real automotive quality, exterior exposure, plating on plastics. You're getting much closer to the real thing when you mention electroless copper than when you speak of silver spray and spray copper.
The great majority of automotive chrome--grills, headlamp surrounds, tail light bezels, etc.--is chrome plated plastic. So it is certainly possible to chrome plate plastic such that it doesn't blister under even the worst conditions for indefinite years. But the process is complex and may be beyond your capabilities to do yourself.
It starts with the right grades of plastic (usually plating grade ABS). The wrong plastics can't be etched to give them proper tooth for truly adherent plating. Then, as implied, it involves etching in a very strong chromic acid based solution or via gaseous etch (a big ticket item).
Then a series of proprietary activators and accelerators involving, usually, palladium chloride and stannous chloride. Then the electroless copper or electroless nickel. Then copper-nickel-chrome plating. The nickel plating must be at least duplex (semi-bright followed by bright), but is often 3 or more layers in newer automotive specs. It is a long, difficult, process demanding proprietary processes.
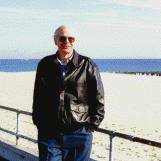
Ted Mooney, P.E.
Striving to live Aloha
finishing.com - Pine Beach, New Jersey
2004
A. The general idea is to somehow infuse a very small amount of Sn+2 compound into the material or onto its surface. Stannous acetate worked well in one paper I read about plating onto plastics. Acetate might be more "like" the plastic than chloride. Including some solvent that almost attacks the plastic but doesn't quite probably also helps. Maybe Isopropanol. Anyway, afterwards, soaking in palladium solution finds the trapped Sn and converts it to Pd metal nano-particles. Pd isn't much oxidized in air like Sn and other things, so if it's present it always provides metal nuclei for electroless-plating solution start to depositing copper or nickel onto. The Pd metal particles are so small and numerous that the growing metal islands of electroless plate-up soon touch and merge. Then you're in business for electroplating. Ted's right about "teeth" helping adhesion, of course. I've made no provision for that. If the object is rough or you can scuff the surface maybe that would help. I did Sn,Pd,etc. to a hard alumina part once, and it all worked except one little spot I couldn't get to start plating. Complete coverage can be evasive when trying to use infusion like this.
- Los Angeles, California, USA
January 17, 2011
Q, A, or Comment on THIS thread -or- Start a NEW Thread