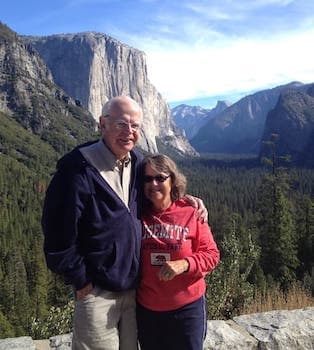
Curated with aloha by
Ted Mooney, P.E. RET
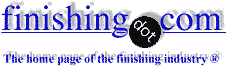
The authoritative public forum
for Metal Finishing 1989-2025
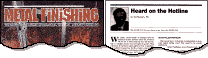
-----
How to reduce hardness in nickel sulfamate plating?

⇦ Tip: Readers want to learn from Your Situation 🙂
many readers skip abstract questions.
Q. Sir, what is the solution of increase the softness of rotary nickel screen? And kindly send me the concentration of nickel bath solution and which chemical has a major role to increase softness of screen.
Shubham patelDirector - Vastral, India
May 31, 2022
A. Hi Shubham. We appended your question to an existing thread which I think will already answer your question for you. But if not, tell us what hardness you are getting and want, and what solution you are using and what it contains and doesn't contain so that readers can suggest what to add or subtract from it. Thanks!
Luck & Regards,
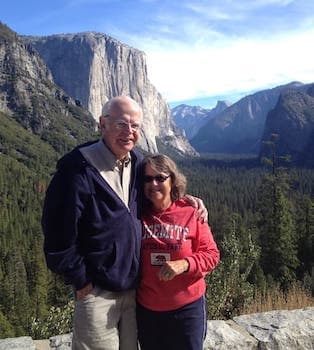
Ted Mooney, P.E. RET
Striving to live Aloha
finishing.com - Pine Beach, New Jersey
June 2022
⇩ Related postings, oldest first ⇩
Q. I made a 1 liter bath to test in, 60 mL of the nickel sulfamate solution 5 g boric acid. I am plating on fiberglass that has been painted with silver paint. My plating came out all cracked. Is nickel sulfamate brittle or flexible? Why is the cracking happening?
Ed Schusterhobby - LA, California, USA
2004
A. Guess 1 is that it cracked because fiberglass thermal coefficient of expansion is about 10 times what nickel is.
Another cause could be something in the bath has caused the nickel to plate in a highly compressive internal stress. I achieved this state when I added a gross excess of liquid anti-pit which cannot be checked with wire loops because of the antifoam agent in it.
Organics from the fiberglass or some other source could also cause this.
- Navarre, Florida
2004
A. Nickel sulphamate nickel can be almost as hard or soft, brittle or ductile as you want! A typical simple bath should be 70 g/l nickel as nickel (the amount of nickel sulphamate will depend on its concentration), 30-40 g/l boric acid ( I prefer to operate about 35-40 g/l), sulfur depolarised nickel anodes and about 10 g/l nickel chloride (optional - the presence of chloride increases nickel stress). Operate at about 55-60 °C with good agitation and a cathodic current density of about 30-35 ASF. The bath pH should be 3.8-4.2. This will give you a dull, ductile and soft nickel.
If you want a brighter and harder deposit, you can add either sodium saccharin or cobalt sulphamate, but these are getting quite technical and you will need some relatively sophisticated equipment to maintain the quality of the bath. Other additives are also widely available. One reason for your problem could be something leaching out of the glass fibre, but that is an unknown to us at present. Always test your deposit with a Hull Cell and a sample deposit.
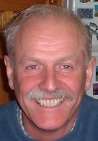
Trevor Crichton
R&D practical scientist
Chesham, Bucks, UK
2004
Q. I am not using nickel chloride, is this bad? I would like the nickel to be very ductile. My pH keeps getting very acidic, what do I do to reduce this? I am plating around .010" thick. Thanks for your help.
Ed Schuster [returning]hobby - LA, California, USA
2004
A. I think that you just mentioned the guilty party. Your anode is not corroding and is acting like an insoluble anode. The resultant low pH tends to drive the internal stress to the compressive side. The insoluble anode also breaks down the sulfamate radical (portion) generating a compound that will drive the internal stress to a very compressive level. That's bad!
If you are not using sulfur depolarized nickel anode - SD rounds in INCO's version - then you need to. If you are using SD rounds, then you have some other problem in your setup, that you have not let us in on yet. Yes, you do have an anode problem.
- Navarre, Florida
2004
A. First, the purpose of nickel chloride is to increase conductivity in the bath and to aid in anode corrosion. If you are using nickel anodes, you need some nickel chloride. If the anodes are insoluble, you probably don't need it.
As far as the pH is concerned, it's normal for the pH to drop with work. You can add nickel carbonate to raise it; be careful because it doesn't dissolve quickly and can lead to roughness in the plating.
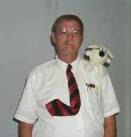
James Totter, CEF
- Tallahassee, Florida
2004
![]() |
A. If you are not using sulfur depolarised nickel, you must add chloride to your bath; if you have SDP nickel, you do not really need it. However, your boric acid is way too low and this may be the partial cause of your problem. The other possibility is the use or creation of insoluble anodes. This will cause the oxygen to evolve from the anode and the pH to decrease. The fall in pH will also cause the nickel deposit to become more stressed. Keep the pH between 3.8 and 4.2. ![]() Trevor Crichton R&D practical scientist Chesham, Bucks, UK 2004 Q. I am using baking soda [in bulk on eBay or Amazon [affil links] to reduce the acid, is this OK? I am using nickel 200 sheet as the anode. Ed Schuster [returning]hobby - LA 2004 |
2004
No, nickel 200 is not a good anode if you want good work! The sodium ions will build up to a level that will affect your plating if you use bicarb.
A. Use SD rounds or pellets in a titanium basket any start out with a new bath and you will not have this problem. Even if you keep the pH perfectly, you are killing your solution.
My thought is that if you are not going to do it right, send it out to a plating shop. pH dropping and requiring nickel carbonate tells you that you either added too much sulfamic acid or you have a serious anode problem. pH dropping on a sulfamate bath definitely is not normal.
- Navarre, Florida
Q. I sent this piece out in the first place and they did not do a good job, that's why I am trying to do it myself. When I got the part back it was paper thin in some areas and .030" thick in other areas. I am conforming my nickel sheet roughly 1/2" around my entire part to try to get a even coat, no shop out there will take the time out to do that.
Ed Schuster [returning]- LA, California
2004
For the record, Ed, I think we should say that it's impractical to pay a shop to take the time to do it, rather than saying that no shop will do that :-)
Some plating shops have people hand applying precision masking under microscopes to do one of a kind plating jobs. Others make micro-machines the size of a pinhead. But you need to pay your plater for his time what you pay your mechanic or plumber, which can certainly make certain time-consuming plating jobs unaffordable.
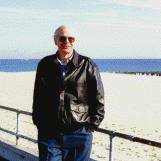
Ted Mooney, P.E.
Striving to live Aloha
finishing.com - Pine Beach, New Jersey
2004
Q. Okay, I have the plating working, what is the best nickel to use for the anode? I need to use sheet to conform it around my part, rounds will not work. I was told wire would work too, any ideas which one?
Ed Schuster [returning]- LA, California
2004
A. I used to make anodes out of titanium micro mesh and 1/16 sheet and TIG welded it together. I used SD pellets on some of the more intricate ones and inserted them thru a 1/2" hole that I plugged with a cut off stopper. This had a napped polypropylene cloth baggie sewn to it or had a draw string. Use poly thread, not silk or cotton.
For my two cents worth, 1/2" spacing is neither necessary nor practical. Increase your air agitation or build a sparger that puts the air agitation where you need it. This requires a non foaming anti-pit, as in SNAP A/M. You very probably need a thief (robber) in selective places to hold down build up in those areas. The wild variation that you referred to normally comes from not using a bleeder type robber and using far too high a current density with inadequate agitation. A picture would sure help talk about this part. Also, a picture of the rack would probably open more comments (help?). Size would help also.
- Navarre, Florida
2004
A. TRY GRAPHITE CONDUCTIVE LAYER INSTEAD OF SILVER.
GOOD LUCK
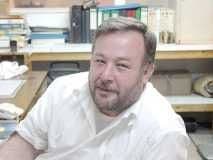
Khair Shishani
aircraft maintenance - Al Ain, UAE
2004
2004
I am getting some better results now, but what you guys are recommending is completely different than what I am now doing. I think for a thin layer the bath you guys recommend is good, I am building this stuff up to .030" thick. After talking to guys here in LA I was told to make my bath 450 G/L sulfamate and 30 G/L boric acid.
This works well, I double checked with a book called "Electroplating" by Frederick Lowenheim
⇦[this on
eBay ,
Amazon,
AbeBooks affil links]
and they had the same mixture listed as well. So I now have the plating working extremely well and very soft nickel, however, after the parts are heated up to 600 or 700 ° C they go very brittle again. Does anyone know how to keep the nickel soft?
How do you make a GRAPHITE CONDUCTIVE LAYER?
- LA, California
A. Hi. Khair is saying that commercially available metalizing materials based on graphite (they're also available based on copper) might work better than silver paint.
I was about to ask what happens to the fiberglass and the silver paint at 700 °C when it occurred to me that you've probably actually been talking about electroforming using a fiberglass mandrel all this time, not electroplating onto fiberglass parts :-)
... in which case a stainless or aluminum mandrel might work better than fiberglass.
If you're only making one or two pieces, your approach with a nickel sheet anode may work, whereas commercial nickel platers must design for equilibrium (the solution should be the same after plating the part as it was before). The issue here is that your nickel sheet won't dissolve well and is actually serving largely as an inert anode rather than a dissolving anode and source to replenish the nickel content, so you may end up starving the bath of nickel pretty soon or having your pH fall too low. James Watts' idea of a titanium mesh anode holding SD nickel crowns might be better, or maybe leaving your nickel sheet but adding SD nickel crowns in a titanium basket as a source of nickel. Continued good luck.
Luck & Regards,
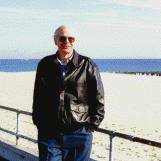
Ted Mooney, P.E.
Striving to live Aloha
finishing.com - Pine Beach, New Jersey
Q. Dear Sir,
We are using Nickel Sulfamate bath to plate Ni on SS plate for mechanical sealing. We required hardness around 100 HV of plated Nickel but after running the process the measured hardness was over 300 HV.
The electroplating is carried out at 60 °C with concentration as: 90 g/l Ni, 41.04 g/l Boric, 5.45 g/l Ni-Chloride, pH maintained 3.8 - 4.4 & Density around 30°Be.
Filtration through carbon & paper along with air agitation was continuous.
Current density is maintained less than 2.5 Amp/dm2.
Please suggest ways to lower the hardness.
electroplater - Karachi, Sindh, Pakistan
September 8, 2008
A. My references say that you will get about 200HV from a clean sulfamate bath. You should be able to control your pH closer to 4.0 than you list. 60 °C is as high as you should go as above that the sulfamate radical starts to break down and drastically raises the internal stress. High watt density heaters will have a local surface temp above the nominal temp. Heat treating it to 600 °C will change the grain structure and all of the other parameters but will lower the HV to about 140. So, 100HV, you will not be able to consistently obtain unless you find some secret that others do not know.
James Watts- Navarre, Florida
September 11, 2008
A. Nickel is usually deposited from a simple nickel bath with no additives at about 200-250Hv - you will not be able to reduce it to 100Hv on a controllable basis. Why do you want soft nickel - perhaps you should consider copper or silver?
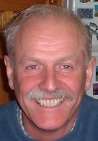
Trevor Crichton
R&D practical scientist
Chesham, Bucks, UK
September 15, 2008
A. Perhaps you could investigate other nickel deposition processes like carbonyl vapor, thermal spraying, sintering, etc.
Guillermo MarrufoMonterrey, NL, Mexico
September 18, 2008
A. The sulfamate nickel must be free of all impurities. Low CD dummy plating may help. No organic additives should be used. continuous carbon treatment is helpful. and There should be no chlorides. The anodes must be SD type with a large anode to cathode area to prevent any anode polarization. Polarized anodes cause the formation of a compound that results in increased hardness and compressive stress. A sulfamate solution can operate without chlorides at moderate, not high Current Density. A pure nickel deposit is the goal for a soft deposit.
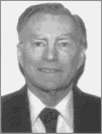
Don Baudrand
Consultant - Poulsbo, Washington
(Don is co-author of "Plating on Plastics" [on Amazon or AbeBooks affil links]
and "Plating ABS Plastics" [on Amazon or eBay or AbeBooks affil links])
September 22, 2008
⇦ Tip: Readers want to learn from Your Situation 🙂
many readers skip abstract questions.
Q. Please explain the mechanism of how stress is related to impurities ? Crystal structure ?
What is the science of this mystery ?
- Greece
October 17, 2008
Hi, Yannoush. Picture rock candy crystals or copper sulphate
⇦ this on
eBay or
Amazon [affil links] crystals, and how the crystals grow large without fracturing from internal stresses when plenty of time is available. A pure metal electrodeposit, produced at a very low current density, can grow large soft crystals where each new atom properly fits into the crystal structure with few dislocations, so the deposit is soft, porous, and stretchy. But add a brightener or an alloying metal that co-deposits, and now the surface is a mess where nothing fits together right; on top of this, increase the current so there are excess electrons demanding to be immediately neutralized by the deposition of a cation, and you get dislocations, additional adatoms, atoms stressed & strained into positions that don't quite suit them, etc. This gives a harder and more stressed deposit.
If this is an insufficient answer, please find a good book on the subject. Public forums and their one or two-paragraph answers are well suited to getting suggestions regarding highly specific problems, but they are generally poorly suited to theory; and abstract questions don't attract reader interest because the human interest in people's problems is absent, plus readers don't want to take the time to poorly explain in 10 minutes what an author took a week to explain far better :-)
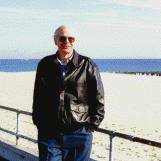
Ted Mooney, P.E.
Striving to live Aloha
finishing.com - Pine Beach, New Jersey
October 2008
Electroplating magnetically soft, low remanence nickel
I have been electroplating permalloy (into micrometer scale openings), but the magnetic saturation is a little too high for my applications. Does anyone know of a particular bath recipe, or post treatment that can obtain particularly, magnetically soft nickel? I am currently using a generic sulfamate bath (Sulfamate, boric acid, sodium laurel sulphate, room temperature). Thanks a bunch.
Peter Tsengstudent - Los Angeles, California
August 2, 2009
Q, A, or Comment on THIS thread -or- Start a NEW Thread