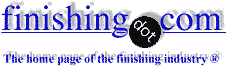
-----
Blisters and peeling in Cu-Ni-Cr
Q. What is most likely the countermeasure of bubbles/peel-off problem?
Our existing set-up for nickel-chrome plate is degreasing>electrodegreasing>Cu activation>Cu plating>Ni activation>Ni plating>Cr activation>chrome plating. Usually Cu plate is the one that peeled-off. I suspected that the cause is due to poor pre-treatment, either in degreasing or in Cu activation. My question is, is it more compatible to use Sulfuric Acid for Cu activation and Hydrochloric Acid for Ni activation? Our existing set-up right now is the other way around. Secondly, how much time is advisable to activate the material (brass items) prior to plating both Cu and Ni?
Thanks in advance.
Jharlen Dianoworking in an electroplating company - Mandaue City, Cebu, Philippines
2004
A. It is difficult to hazard a guess, but remember that chromic acid is a wonderfully effective passivation agent :-)
If your rack coatings are poor, or housekeeping is a problem, chromic acid will get into your cleaners and copper plating tanks and ruin adhesion.
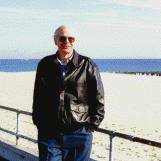
Ted Mooney, P.E.
Striving to live Aloha
finishing.com - Pine Beach, New Jersey
2004
Q. You had not answered my question. I'm asking about the compatibility of acids to be used in activation prior to copper and nickel plating respectively.
Jharlen- Mandaue City Cebu, Philippines
2004
A. I'd suggest sulfuric acid for both.
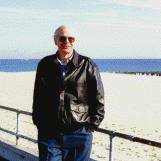
Ted Mooney, P.E.
Striving to live Aloha
finishing.com - Pine Beach, New Jersey
2004
A. Use sulfuric acid 10-15% by volume in both cases and do electro degreasing properly.
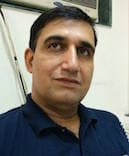
Ajay Raina
Ludhiana, Punjab, India
2004
A. But I think cause of the problem is another thing, as you said Cu plate is one that peeled-off, I think the electroless reaction between copper ions and brass elements is the main reason of this phenomena. We have had such problem during Cu plating on lead bronze alloy.
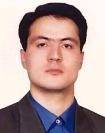
Mahdi Farahani
engine parts - Qazvin, Iran
2004
! Mahdi, your comment about poor adhesion of copper to leaded bronze is interesting. The reason for the poor adhesion is "lead smear" which is caused by the lead in the bronze smudging or smearing during the machining process. This is a common problem with metals where lead has been added to enhance the machining capabilities. I think the best way of overcoming it is to use a copper fluoborate bath as this should adhere to the lead.
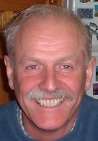
Trevor Crichton
R&D practical scientist
Chesham, Bucks, UK
2004
A. If your brass items are leaded brass and soldered assemblies, I recommend the following process flow: Degreasing > Electrodegreasing > rinse > Acid dip in 10% by vol. fluoboric acid for 5-15s at RT > rinse > dip in a 30g/LNaCN solution > rinse > Copper strike plating > rinse > acid dip in 5% by vol. sulfuric acid >rinse > Nickel plating>acid dip in 10%-15%vol. sulfuric acid > rinse > chrome plating > rinse > hot rinse > dry
Malou CanonesMIRDC-Government Agency - MIRDC, Manila, Philippines
2004
A. We encounter the same problem in our line. Yes basically copper plating adhesion on your base metal is weak. Both acids you mentioned will do. Try to consider the oil removing capability of your degreaser first before jumping ahead on your process. You could also improve your rinsing process.
Marlon L. CordezSurface treatment supervisor - Sta. Rosa, Laguna. Philippines
2004
A. Better to use Iron activation prior to Cu plating and Sulfuric Acid prior to Ni plating...
Redford OlanProduction Engr. - Muntinlupa
2005
How to plate copper over Ni (35%)-Co(35%) based alloy?
October 20, 2013Q. How to plate copper over Ni (35%)-Co(35%) based alloy?
Recently, I have been trying to electrodeposit copper onto Ni-based alloy using bright acid copper solution. The adhesion between Cu and NiCo alloy is very poor. My clean and etching steps are as following:
1. soak in sp degreaser(60 °C),
2. hot water and DI water rinse,
3. Activate in H2SO4, HNO3 and HCl mixed solution
4. rinse
5. electrodeposit in acid copper solution using 1.5 A/dm2 current
- Tallahassee, Florida, USA
A. Hi Rongmei. This nickel-cobalt alloy will be very passive and unreceptive to plating. Please try starting with a Wood's Nickel Strike, and then, almost immediately, doing the copper plating. Good luck.
Regards,
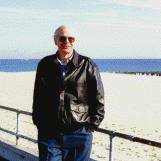
Ted Mooney, P.E.
Striving to live Aloha
finishing.com - Pine Beach, New Jersey
October 23, 2013
Q. Dear Ted,
Thanks for your answer. you are right, it is really hard to plate on Ni-Co alloy with well bonding, even using Wood's Nickel strike.
- Tallahassee, Florida, USA
October 24, 2013
A. Hi. ASM Metals Handbook Vol. 5, "Surface Engineering" has a chapter on prepping refractory metals for plating with very aggressive activation sequences. You could review whether parts of those powerful processes are applicable ... and then follow them with the Wood's Nickel. Good luck.
Regards,
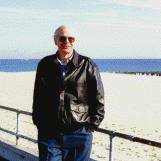
Ted Mooney, P.E.
Striving to live Aloha
finishing.com - Pine Beach, New Jersey
October 24, 2013
Q, A, or Comment on THIS thread -or- Start a NEW Thread