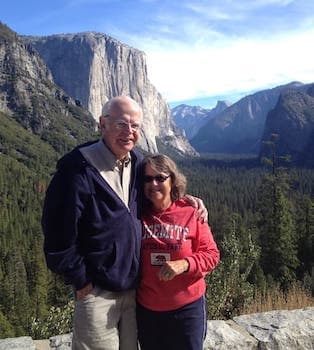
Curated with aloha by
Ted Mooney, P.E. RET
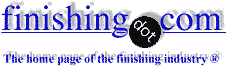
The authoritative public forum
for Metal Finishing 1989-2025
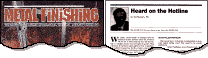
-----
Procedure For Zinc-Nickel Plating
for Shops, Specifiers & Engineers
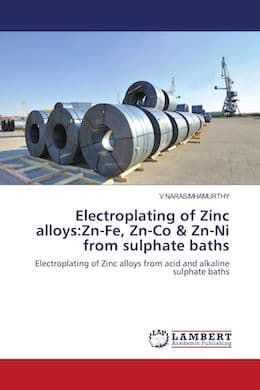
from eBay, AbeBooks, or Amazon
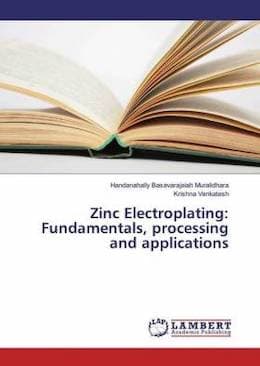
from eBay, AbeBooks, or Amazon
"Alkaline non-cyanide zinc plating with reuse of recovered chemicals" by Jacqueline M. Peden (1994)
from (U.S. EPA)
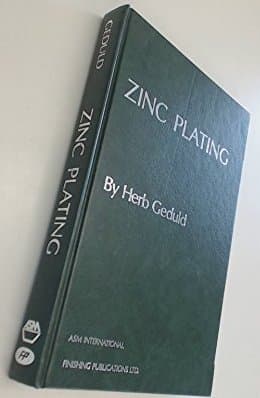
from eBay, AbeBooks, or Amazon
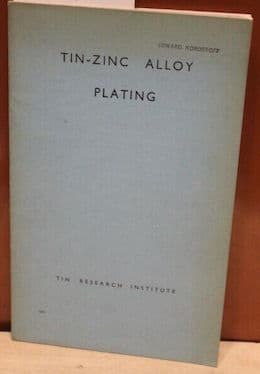
from eBay, or AbeBooks
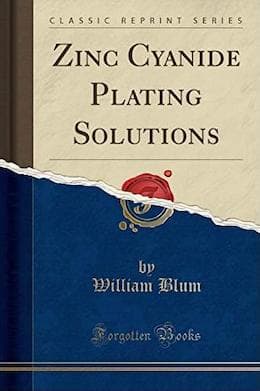
from eBay, AbeBooks, or Amazon
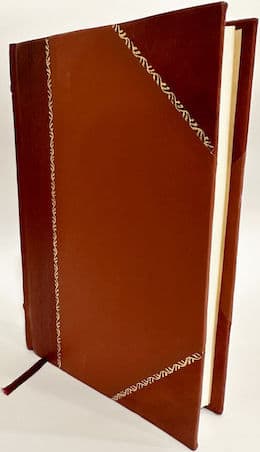
from eBay, AbeBooks, or Amazon
(as an Amazon Associate & eBay Partner, we earn from qualifying purchases)
Q. Question about Abrasive Cleaning in Zinc-Nickel Plating.
The journal article "A New Zinc-Nickel Electroplating Process" by Grace F. Hru mentions abrasive cleaning as a necessary step for good plating adhesion.
It specifies using a method following BAC 5748 with options for glass bead or aluminum oxide abrasive.
What is the importance of abrasive cleaning , I cannot find any information about BAC 5748 and is it important to do abrasive blast before plating.
- KEPALA BATAS , PULAU PINANG
May 6, 2024
A. Hi Abdul.
In general, abrasive cleaning is not a necessary part of the zinc-nickel plating process. It does not have special pretreatment requirements differing from zinc plating and other zinc alloy plating. Usually it can be substituted for plain zinc plating without pre-treatment changes.
BAC 5748 is a Boeing specification for abrasive cleaning, deburring, & finishing which is available only to Boeing suppliers. The article you cited was published 41 years ago and was new technology at the time.
There are certainly cases (for pretreatment of special substrates or prevention of hydrogen embrittlement, for example) where abrasive blasting is the specified and/or required pretreatment for plating, though.
Luck & Regards,
Ted Mooney, P.E. RET
Striving to live Aloha
finishing.com - Pine Beach, New Jersey
⇩ Related postings, oldest first ⇩
Q. I'm a metal part / component manufacturer and many of them are plated in-house. I've known of Zinc plating with Passivation and Nickel plating, but an integrated ZINC-NICKEL plating was news to me. Our parts undergo Nickel plating to about 15 microns for anti-corrosive properties and hardness. I would like to know more about the process, its techno-economics and other advantages over Nickel plating & Hard Chromium plating. Whether it can be done using the existing tanks & rectifiers?
Joseph V. WILSON- Coimbatore, Tamil Nadu, INDIA
2003
A. Hello Joseph,
Zinc-nickel plating is an essentially proprietary replacement technology for cadmium plating, or a step up from zinc plating. It is a non-decorative sacrificial plating, and not a suitable replacement for nickel or chrome plating.
There is a small enough amount of nickel in it to give it the desired potential to cathodically protect steel like zinc plating does, but offer greater corrosion protection. It is offered as either an acid or alkaline process, depending on which supplier you go with. It always uses chromate conversion coatings which are basically similar in application to those used on zinc or cadmium plating, but the chemistry is a little different. Good luck.
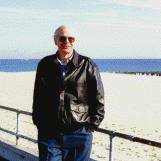
Ted Mooney, P.E.
Striving to live Aloha
finishing.com - Pine Beach, New Jersey
Q. Dear Sir,
I have one of the leading Electroplating Companies. I am planning to do Zinc-Nickel Plating but I don't know the procedure correctly. So, I request you to give me the procedure -- I expect a quick response from you.
Thanking you,
Yours Sincerely,
Electroplating shop - Hyderabad, Andhra Pradesh, India
2004
by Abner Brenner
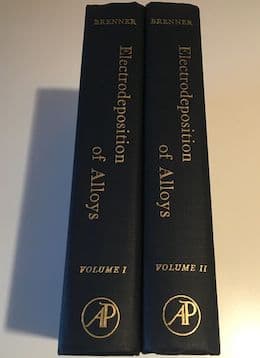
on AbeBooks
or eBay or
Amazon
(affil links)
A. Hi Yalamanchili. If you are just looking for raw research results on what might work in formulating such a process, you might wish to see Brenner's "Electrodeposition of Alloys" ⇨
It includes tables for many different potential formulations, the alloy percentage each formulation was found to deposit, etc.
But the gap from research to commercially viable processes is a substantial one, bridged by years of development work by the suppliers. Realistically, zinc-nickel plating is a proprietary process. You decide whether to do acid or alkali plating, select a supplier, and get from them the technical data sheets which answer all your questions about the procedure. Usually you get hands-on help as well. None of this means that you're forbidden to attempt home brew of course -- but commercial success is based on trade secret development, so you won't find the kind of data you need from trade journals, websites, or other publicly accessible resources. Good luck!
P.S.: This is a public forum. When you tell other readers that you expect a quick response from them, we're all certainly be expecting you to offer quick responses to others' questions in return :-)
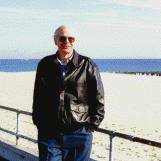
Ted Mooney, P.E.
Striving to live Aloha
finishing.com - Pine Beach, New Jersey
A. Zinc-Nickel Plating is best done from an Alkaline bath which deposits evenly in low current densities. The end use, if automotive, will require a trivalent chromate to match SST specs. Zinc Nickel Alkaline bath is available in India and most GM, Ford, Japanese and German specs specify and accept a 12% Nickel content.
The procedure is simple. Soak followed by Anodic cleaning and pickling, followed by a second Anodic stage constitute pre-treatment. The Zinc Nickel Bath runs at 6-10 volts Rack/Barrel with filter and moving cathode for rack. Temperature 25 °C is essential. Controls include Caustic, Zinc as metal, and Nickel as metal as specified in the operation manual. The current is passed through inert Nickel anodes. Nickel is replenished chemically using proprietary concentrates while zinc is dissolved off-line in a separate zinc generator and replenished periodically. Parts must be clean before plating, rinsed well after plating, chromated in special chromates meant for Zinc-Nickel plating and a top coat sealant helps to achieve the required SST hours.
The process is a consolidated metal system which needs to be controlled periodically by analysis to achieve the right alloy composition thereby ensuring consistent SST.
Regards
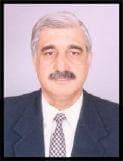
Asif Nurie [deceased]
- New Delhi, India
With deep regret we sadly advise that Asif passed away on Jan 24, 2016
A. Sir:
You have several decisions to make regarding bath selection. First, alkaline or acid. (I prefer Alkaline). Secondly, low nickel in the alloy or high nickel in the alloy. The amount of nickel will have an impact on the ultimate corrosion protection given to your parts. Remember that the higher the % Nickel, the more difficult it will be to put an acceptable chromate passivate on it. Next, consult with your vendors to find a source that will meet your exact needs. I recommend checking the Chemicals advertising section of www.Finishing.com to see if anyone there can be of assistance to you.
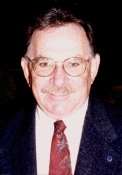

Ed Budman [deceased]
- Pennsylvania
With deep sadness we advise that our good friend Ed passed away Nov. 24, 2018
Multiple threads merged: please forgive chronology errors and repetition 🙂
Effect of Chromate Leaching on Conversion Coated Zinc Nickel Alloy Plate
Q. In a Gumm Chemical Technical Article, "Zinc-Nickel Alloy Plating" by Mr. Nabil Zaki he states that post-plate chromate conversion coating of zinc-nickel alloy plate results in a "nickel-rich superficial layer which in turn increases "the overall corrosion resistance 5 to 10 times". Is this a reasonable expectation of chromate conversion coated zinc-nickel alloy plate and what effect would leaching of the chromate (ie., yellow to clear) have on the overall corrosion resistance? Thank you.
Myron C. Clark- Stanfield, North Carolina
1999
A. Hi Myron. My own personal take on this issue starts with the recognition that both zinc and zinc-nickel alloy are sacrificial (cathodically protective) coatings, whereas pure nickel is only a barrier layer coating, so zinc-nickel offers an important feature which pure nickel doesn't: it corrodes preferentially to steel to protect it. One of its advantages over pure zinc is that, with the right percentage of nickel, the sacrificial corrosion is slower, and/or the corrosion products are more effective towards retarding continuing corrosion.
So I wouldn't focus much on hoping that spending an exact amount of immersion time in a chromate tank of a particular composition, both of which are chosen for optimum chromating success rather than nickel enrichment, will incidentally re-optimize a zinc-nickel percentage which was already optimized :-)
Many people feel that "leaching" is just a specs game anyway, i.e., that if you leach out the color, you're leaching out the chromate, and losing most of its protective value.
Regards,
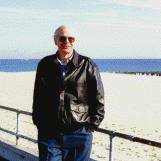
Ted Mooney, P.E.
Striving to live Aloha
finishing.com - Pine Beach, New Jersey
Ed. note: Readers, please note the date of Myron's inquiry. We are now in a RoHS (European driven "Reduction of Hazardous Substances" ) age where colorless new technology trivalent chromates are widely used and 'leaching' is fading into history. Some of the following Q&A's may also precede the continuing switch to improved trivalent conversion coatings.
Hexavalent vs. trivalent chromating for zinc-nickel plating
Q. Hi,
We have a small business which makes small steel rings. The rings are about 1/4 in diameter and are made of annealed steel. In an attempt to get good corrosion resistance, we are plating them with High Zinc/Nickel. Now we must decide to use either Hex chromate or Trivalent chromate (to make the corrosion resistance even better).
I've heard hex chromate is better for corrosion resistance but is toxic? What does that mean? If you have a finished product of Zinc/Nickel and hex chromate, is it dangerous for people to handle that finished dry product?
This is very confusing because it sounds like many things are plated this way?
Thanks,
Joe Trainer- Aurora, Illinois, US
2002
A. We are living in changing times, Joe. Hexavalent chromate is the traditional type and historically exhibited far better corrosion resistance than trivalent chromate.
But there has long been a general movement away from hexavalent chromates on leading edge products like aircraft due to toxicity of the waste products and concern that the material might eventually be determined to be carcinogenic for skin contact. More recently, by directive of the European Parliament, hexavalent chromates can effectively not be used on automobiles anymore because they are believed to interfere with recyclability. This ruling served to lend immediacy to the search for replacements.
A number of things have happened therefore: some work that was formerly zinc plated has moved to electroless nickel plating; new topcoat processes have become available to add the required extra corrosion resistance to trivalent chromates (although perhaps sacrificing conductivity); improved trivalent chromates have been developed.
What to specify probably depends on the life cycle of your parts and designs, and your companies attitude toward environmentalism versus affordability. The replacement technologies are more expensive, more complicated, and consequently more subject to error in processing--but you can have a process that imparts sufficient corrosion resistance without using hexavalent chromates.
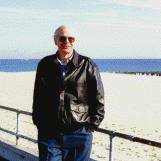
Ted Mooney, P.E.
Striving to live Aloha
finishing.com - Pine Beach, New Jersey
Mr Mooney, thanks very much for the reply. I really appreciate it! We want to be environmentally safe so we are looking into the hex alternatives. Unfortunately, our first quote using zinc/Nickel with Trivalent and top coat is about 6 times more expensive than zinc/Nickel with Hex. That would pretty much put our end price way past reasonable.
The search continues....
Thanks Again,
Joe Trainer [returning]- Aurora, Illinois, US
A. Hi again. All I can say is that the price differential will rapidly fall and will eventually become a minor issue as trivalent chromating becomes a necessity rather than an option. Good luck.
Regards,
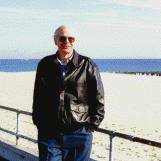
Ted Mooney, P.E.
Striving to live Aloha
finishing.com - Pine Beach, New Jersey
Trivalent chromating of zinc nickel plating
Q. We are investigating and testing trivalent chromates on a Zinc Nickel alloy deposit, 10-15% Ni. Within 24 hours of salt spray testing we get a white substance called or described as a "white veil" or "grey veil". We never see this using a hexavalent chromate on top of Zn-Ni. Red corrosion is not an issue, +1000 hours. Does anyone know what the white substance is and how to stop it?
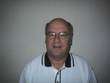
Cliff Roy
plating shop - Conestee, South Carolina
2002
A. Most likely that white substance is either white corrosion or pooling of the topcoat/sealer. Many topcoats for trivalent chromate systems pool up and turn white over a few days' time. You may get the same white stuff if you let the parts sit around untested.
I've heard trivalent chromates don't have as good synergy with zinc-nickel alloys. You may want to compare your zinc-nickel with similar samples of zinc-iron.

Tim Neveau
Rochester Hills, Michigan
Tim,
I appreciate your response. We do not have a topcoat on trivalent chromate zinc-nickel. You probably don't see this condition on zinc iron deposits because the chromate is hex.
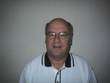
Cliff Roy
plating shop - Conestee, South Carolina
A. Cliff:
Our experience with trivalent yellow passivation on Zn/Ni has given us results similar to yours. That is to say, the appearance of a white or gray veil, that according to the analysis that we have made does not correspond to an oxidized part, but to the decomposition of a by-product that has nothing to do with oxidization of the part.
One observation that supports this thesis is that a Zn/Ni [part I tested] oxidized white in 24 hours, but never came to red corrosion in 1000 hours. I hope to continue speaking of the subject with you.
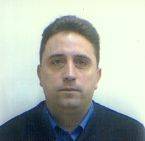
Miguel Angel Martín
surface finishing shop
Madrid, Spain
Q. Could someone please answer the following:
Does a chromate post treatment of a Zinc-Nickel plating (AMS2417, 12% Nickel) have a significant affect on the ability to pass salt spray corrosion testing. I need to pass 1000 hrs salt spray (MIL-PRF-83513) while keeping the surface electrically conductive. The heavy chromate coating over the zinc-nickel plating substantially increases the surface resistivity of the parts, so I'd like to eliminate it. Current plating system is 6061-T6 Al base material, zincated IAW ASTM B253, Electroless Nickel IAW AMS2404, Zinc-Nickel IAW AMS2417.
Thanks,
Joe KlockerWilmington, Massachusetts
2002
A. Have you thought of plating the alloy Tin-Zinc on the electroless nickel. This alloy will exceed 1200 hours of salt spray plus you will have the conductivity you require.
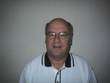
Cliff Roy
plating shop - Conestee, South Carolina
2002
Strange Corrosion Product on Zinc-Nickel Plating with Trivalent Chromate
Q. I am running the standard ASTM B117 salt spray test on Trivalent Zinc-Nickel plated steel. I see the typical white rust and some red rust, but the parts are also forming a hard black scale or corrosion along the edges and near punch outs. Any idea of what this is?
Tony Schweikletest lab - Bloomingdale, Illinois, USA
May 5, 2008
A. Hi, Tony. Very interesting question. Maybe the plating along the edges and at cut-outs is a substantially different alloy composition because of the higher current density there? Or maybe the edges were cut in a way that left a scale on them that the plating shop could not fully remove, so the spots didn't plate or plated differently. Any chance of getting a reading on the alloy composition before the salt spray test, or seeing the parts before they are plated, or learning the mechanism of the shearing and punching (maybe it was by laser or other cutting method rather than typical shear and punch press)?
Regards,
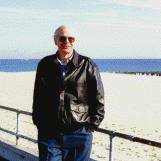
Ted Mooney, P.E.
Striving to live Aloha
finishing.com - Pine Beach, New Jersey
A. Unless ASTM B117 has changed, you mask the outer 1/4 inch of the panel.
For the type of metal finishing that we did, we chose to ignore the outside 1/4 inch rather than to do the masking step and it worked very well for our needs.
- Navarre, Florida
A. Hello Tony.
Unless I am mistaken the problem lies in the PLATING TECHNIQUE. I presume the bath is Alkaline Zinc Nickel?
1)Alkaline Zinc Nickel Plates at half the speed of regular Alkaline zinc. Pushing up Current density causes edge burn. The edge burn then translates to premature failure at the edges. Reducing the Current density could be considered to prevent edge burn which is sometimes not immediately visible.
2) Solution agitation using eductors
⇦ this on
eBay
or
Amazon [affil links] can help you increase current density without the burn.
3) Cathode rod agitation too will help increase the current density.
4) Operating at the recommended bath temperature between 20 and 28 °C too will help keep the metal distribution in order.
Solution circulation using eductors or Cathode rod agitation helps with distribution and uniform alloy composition.
Hope this helps.
Regards,
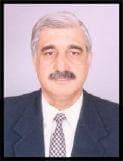
Asif Nurie [deceased]
- New Delhi, India
With deep regret we sadly advise that Asif passed away on Jan 24, 2016
Q. In reply to some of the questions; the parts are from a typical shear and punch, and the plating bath is Alkaline Zinc Nickel.
The part I am running is an assembly with stainless steel hardware. So we were thinking this might be galvanic corrosion, since it seems to start at the hardware and run down along the edge of the plate.
I ran a single plate for 7 days and did not see any corrosion, even after placing stainless steel hardware in one of the slots for the last 3 days.
I plan to send a sample to a lab for analysis on the black substance.
test lab - Bloomingdale, Illinois, USA
May 29, 2008
A. I agree with James. The sides of the sample have to be masked and not considered for the test.
Prat George- Baton Rouge, Louisiana
Zinc-nickel plated bolts are burning
Q. Hi all,
I have been involved in plating line almost 1 year. Any of you know about Zinc Nickel chromate ? I've got problems for this plating. Bolts keep burning during plating and the colour not like iridescence yellow. Please help.
plating line - masai,johor, Malaysia
April 9, 2014
A. Hi Noya. Asif Nurie notes above that Zinc Nickel plates at half the speed of alkaline zinc. Could the burning be resulting from trying to hold too high a current density?
To my limited knowledge the chromate will be more purple and red than the usual iridescent yellows because it doesn't take as thickly and uniformly on this nickel-bearing alloy as on zinc.
People will need a good deal of data from you to help you troubleshoot. Good luck.
Regards,
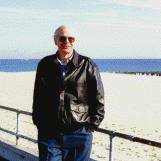
Ted Mooney, P.E.
Striving to live Aloha
finishing.com - Pine Beach, New Jersey
Nuts get no zinc-nickel plating on threads
Q. I'm involved in zinc nickel electroplating for nuts, but currently we are facing some problems. The inside of the nut (thread area) cannot get plating while the outside flat surface got the plating. We are using alkaline zinc nickel solution. Hope to get some idea regarding this problems.
Thank you,
Suriani
chemist - masai, Malaysia
May 15, 2014
A. Hi Suriani. The plating goes where the current goes, and the current takes the shortest path, so there is always much less plating on the inside of a nut than on the outside. But there are a hundred different possible reasons why you are getting no plating on the inside, including the threads not being properly cleaned or activated, or the nuts being racked in a fashion whereby the rack hook steals all the current. So what we'd like to do along with you is to eliminate some of those possible reasons.
Please start by telling us what size these nuts are, whether you are barrel plating or racking them, and whether or not you are doing any other successful plating of these nuts or similar parts. Thanks!
Regards,
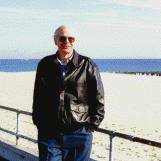
Ted Mooney, P.E.
Striving to live Aloha
finishing.com - Pine Beach, New Jersey
Formulation of boosters for zinc nickel electroplating
Q. Hello
my name is joel from Pretoria,south Africa. I am conducting experiment on zinc nickel electroplating; my problem is I want to know the formulation for boosters to use for the zinc nickel electroplating.
student - pretoria south africa
March 31, 2016
A. Hi Joel. As you will learn from reading the earlier entries on this thread, practical zinc-nickel production plating is a rather different thing than laboratory work...
For your lab studies you can start with Brenner's Electrodeposition of Alloys, which has a long and detailed chapter on the subject; it will give you dozens of potential formulations, and several good starting points for lab experiments with various organic and inorganic additives.
Actual production plating, however, will almost surely require proprietary products -- and no one can or will give you the fruits of those years of development work. So, if your lab work is about trying to study how addition agents work and can be improved, start with Brenner. But if your need is to put useful zinc nickel plating onto parts in preparation for using those parts to meet some need, you will want to purchase a proprietary process. Good luck.
Regards,
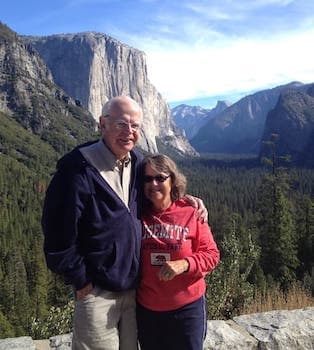
Ted Mooney, P.E. RET
Striving to live Aloha
finishing.com - Pine Beach, New Jersey
Anode Cathode ratio for rack zinc nickel plating bath.
Q. What is the minimum/ ideal anode cathode ratio for a rack zinc nickel bath (85/15)? I have been told it is anywhere from 0.5:1 to 4:1. We run a number of small cylindrical aluminum parts and experience poor throw in the id of the parts. We keep the bath within a finite operating window and have been fighting this for some time. I am finally looking at anode cathode ratio. We run nickel poles for anodes with a total of 3.5 sq.ft. of anode surface area in the bath.
Doug Hughes- San Fernando, California USA
May 27, 2017
adv.: Supplier of Copper Anodes, Nickel Anodes, Bismuth Metal, & Other Metal Products for Industry & The Arts
Q, A, or Comment on THIS thread -or- Start a NEW Thread