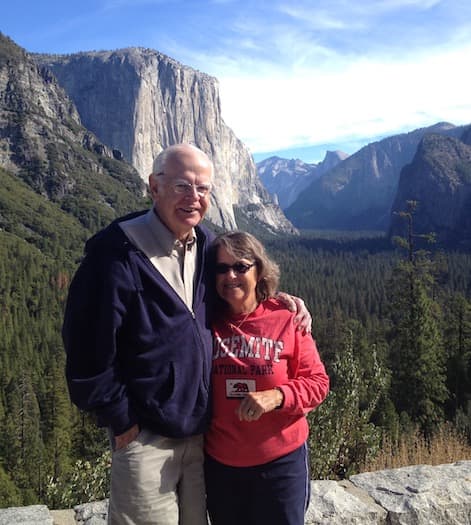
Ted Mooney, P.E. RET
- Pine Beach, NJ
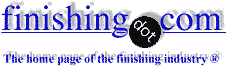
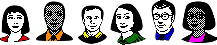
The authoritative public forum
for Metal Finishing since 1989
-----
Purpose of Acid in Copper Plating

Q. Dear sir, I want to know if the structure of copper is affected by high range of sulfuric acid .
We maintain it at 63 gm/l.
But when its range is around 70 gm/l then we get rejected from polishing department like as "bad structure". Is the high range the reason of bad structure copper.
I am with a electro plating company - Noida, India
December 30, 2023
A. Hi Guarav.
I don't know what "bad structure" means. Can you explain, in different words, precisely what your polishing department means by "bad structure"? If you can't explain precisely what they mean, you have a communication problem in-house which ought to be resolved first. Attempting to resolve a problem without agreeing on exactly what that problem is will prove hopeless :-)
I will guess that they mean the plating is "burned". Such a defect will occur first at high current density edges and corners. Is that what the polishing department reports?
Do you run Hull Cell panels? Is there a noted difference when they are run at 63 gm/l vs. 70 gm/l?
In my opinion until you understand exactly what the problem actually is, and/or have Hull Cell panels to demonstrate that high sulfuric acid is problematical, you should not be making adjustments to your operating range. Some shops operate at 70 gm/l, although it is high, and some operate at half that.
Luck & Regards,
Ted Mooney, P.E. RET
Striving to live Aloha
finishing.com - Pine Beach, New Jersey
⇩ Related postings, oldest first ⇩
Q. I am creating some numerical models for electrochemistry. I am hoping to use electroplating as a form of global validation. I have run a few preliminary tests trying to plate copper on copper using 0.1 M Copper (II) Sulphate solution using distilled water at around 1 V Potential difference across a 3 mm gap. I have noticed a black deposit on the ve electrode. I am suspecting this is Copper Oxide formed from the dissolved oxygen in the distilled water. On a number of websites I have found that the addition of H2SO4 is used in the electrolyte, although I cannot find why this is the case. Again, I suspect that it is used to remove the dissolved oxygen. Is this the case, and if not, then why is it there? If I were to use a solution of de-oxygenated Copper sulphate, would I get the same results as including the sulfuric acid? What I am really interested in is whether the sulfuric acid becomes involved with the surface electrochemical reaction?
If anyone has any comments or suggestions I would be very interested in your opinion. Also I would be very interested in any recommended links or resources in this matter. Cheers.
Andrew Garrardstudent - Sheffield, UK
2004
by William Safranek
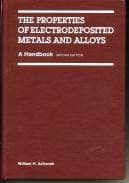
on AbeBooks
or eBay or
Amazon
(affil links)
A. Hi Andrew.
The black smut is probably copper rather than copper oxide -- very finely divided particles of copper or other metals tend to appear black because their shape is such that little light tends to be reflected from them.
The acid is necessary for two reasons. First, the solution needs to be conductive in order for plating to take place, and acids like sulfuric acid exhibit great conductivity because of the hydrogen ions they loose. Second, you cannot deposit metal out of solution unless it is in solution, and you can't keep simple salts of copper in solution at high pH.
As a general rule when you electroplate, a small portion of the applied electricity electrolyzes water into H2^ and 2OH-, the hydrogen leaves the solution as a gas and the OH- continuously raises the pH of the solution, which must be counteracted by additions of acid.
When it comes down to the very fine points of exactly what intermediate reactions are occurring in the boundary layer of the plating process, it is extremely complicated and much of our knowledge is empirical, so I hesitate to try to answer your question of whether the sulfuric acid "becomes involved with the surface electrochemical reaction". Safranek wrote a whole book on how the properties of the deposited metal vary according to the deposition parameters .
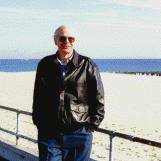
Ted Mooney, P.E.
Striving to live Aloha
finishing.com - Pine Beach, New Jersey
A. The sulfuric acid in a copper electrolyte is there for two reasons, one is to keep the copper in solution, you only used a 0,1 m solution, if you use higher concentrations your copper sulphate will partially get Cu(OH)2 . Also the sulfuric acid gives you a better conductivity and with this comes a better throwing power. Throwing power is the ability of the electrolyte to get uniform depositions in areas with different current densities. The more sulfuric acid you add, the better is your throwing power, for example a usual copper electrolyte contains about 60 g/l Sulfuric acid, a copper electrolyte for plating printed circuit, which have very small holes to plate in, contains about 220 g/l sulfuric acid.
What you plated out of your solution is probably copper; to get a better deposition I would suggest you use a 1m solution of copper sulphate ⇦this on eBay or Amazon [affil links] with 60 g/l sulfuric acid and also about 100 mg/l Hydrochloric acid ⇦this on Amazon [affil link] .
Marcus Hahn- Lucerne, Switzerland
Q. Thank you for your comments. I have continued to attempt to plate copper, but I am having little success. I tried adding the recommended amount of acid to my copper sulphate, but this resulted in a large number of bubbles of H2 being evolved. I would very much like to conduct plating without the evolution of gas, as this will add unnecessary complexity to my model. I know that it is possible to undergo an electrochemical reaction with aqueous solutions without hydrogen evolution. Is there any way of obtaining acceptable results from a simple system of copper anode, copper cathode and copper sulphate solution? If so I would very much like to know it, and if not could anyone recommend an alternative system that I could try?
Andrew Garrard [returning]student - Sheffield, UK
A. Unfortunately I don't understand what it is that you are trying to do when you speak of your model, Andrew. I don't know what exactly you mean by "numerical model" in this particular context, and although I understand the words "global validation", I don't know what you mean with respect to this plating demonstration. And when people don't understand the mission, their suggestions usually result in the wheel-spinning and crosstalk we've seen to date on this topic. Please spend another paragraph explaining exactly what you are trying to do, prove, or demonstrate--and why.
If you are trying to demonstrate Faraday's Law, I agree that hydrogen evolution upsets the demonstration. But while copper can deposit at very close to 100% efficiency, it's probably not quite, so there will be some loss to the evolution of hydrogen, although it is good to get it close to zero. It is possible that copper pyrophosphate may be a better electrolyte for your needs, but I still don't know what those needs are :-)
Electroplating in aqueous solution is not equivalent to a vacuum process where you might try to remove "everything else" so the reaction can proceed unhindered. Rather, ionization and migrationare part and parcel of electroplating, and boundary layer phenomena are poorly understood, and your electrolyte has to be capable of allowing the copper to go ionic and stay ionic. And this may involve acids or complexors, rather than deionized water. Good luck.
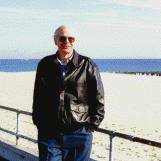
Ted Mooney, P.E.
Striving to live Aloha
finishing.com - Pine Beach, New Jersey
Q. Hello,
In an attempt to keep my requirements simple I have clearly made them unintelligible, and for this I apologise, so please permit me to tell you a little about what I am trying to achieve. As part of my studies, I am trying to create a comprehensive model for electrochemistry. A model is a mathematical prediction of various parameters, such as current density, potential distribution etc based on a set of equations and solved using a computer. I believe that I have developed such a model, primarily using the Butler Volmer equation, which I am sure that electrochemists are familiar with. In order to validate that model is performing correctly, that is to say that the output from the computed equations gives an accurate prediction of what happens in real life, I was hoping to use a simple electroplating system. I have set up a small test rig with a Power supply and naively thought that if I immersed two lumps of copper into copper sulphate that I would produce excellent electroplated results. Very much like the opening paragraph in your "FAQ: Electroplating--How It Works" section. I am neither an electrochemist nor an electroplater, so I have very little experience in this area and am deeply grateful for any help.
So my requirements are only for a simple system of electroplating that I can use to validate my model. My model makes the assumption that the system remains in single phase, that is to say that there is no mixture of liquid and gas, it is all liquid. Incorporating the equations for multiphase flow would add significantly more complexity than I can deal with at the moment. Within the chemical process industry there are numerous documented electrochemical reactions that do not result in hydrogen evolution, so I know that some must exist. The addition of acid produces significant amounts of gassing at relatively low voltage. In a paper by Uziel Landau (Case Western Reserve University) about through hole plating of PCBs he says that acid is not necessary to copper plate. In addition I would like a system where the electrolyte is not chemically affected so that I can recycle it and the chemical properties are still known. I am at university, so I can get hold of almost all chemicals, but for convenience, I would prefer ones that were less toxic or corrosive.
Thank you kindly for your time.
Andrew Garrard [returning]student - Sheffield, UK
A. Thanks, Andrew, I understand.
I think your principal problem then is an anode to cathode spacing that is far too close for that voltage. Can you change this to 3 cm instead of 3 mm? If not, then greatly reduce the voltage, although that may not work as well. Here's the deal--
The first principal of electrochemistry as far as electroplaters are concerned is Faraday's Law. This states that 96,485 coulombs (amp-seconds) will deposit a gram molecular weight of metal if operated at 100 percent efficiency. This is simply a conversion factor which accounts for how we count electrons vs. how we count atoms, and you'll understand it with just a few minutes of thought and realize that it is incontrovertible. That is, if the plating process operates at 100 percent efficiency (100 percent of the electrons go toward reducing metal ions in solution rather than into losses such as liberation of hydrogen) then a fixed amount of copper is deposited.
But think of this. Suppose the solution is conductive and a lot electricity is flowing, and there is no or almost no copper in solution, what happens to Faraday's Law then? The electricity is flowing but a proportional amount of copper cannot possibly deposit because it isn't even there. What has happened is that the efficiency has dropped to near zero, with most of the electricity liberating hydrogen.
The cause of your smut is probably efficiency lower than 100 percent (although tramp metal contaminants can also cause smut). Copper ions are not being oxidized into solution, traveling across the solution, convecting themselves through the boundary layer, and being reduced to metallic copper at a rate sufficient to keep up with the electron flow you are imposing -- so electrolytic side reactions are forced to occur by the surfeit of electron flow. Among these is the generation of hydrogen and extremely finely divided copper instead of proper crystal growth, making it into a smut. Increase the anode to cathode spacing by a factor of ten and the solution resistance will increase by a factor of ten, so the current flow will be cut by a factor of ten, and the electroplating process may be able to keep up with the electron flow. You can't rush the plating.
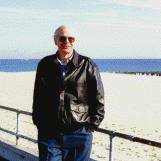
Ted Mooney, P.E.
Striving to live Aloha
finishing.com - Pine Beach, New Jersey
Q. Thank you for all your help in this matter. I was emailed by someone viewing this post who provided some very interesting documentation in the matter.
Ed. note: It's a shame that someone e-mailed you rather than posting -- this isn't intended to be a private hook-up service which leaves the poster satisfied while cutting hundreds or thousands of readers adrift 8 postings into an issue :-(
Try to imagine a Dear Abby or Ann Landers column where she advises the lovelorn that she'll tell them what to do about their posted quandary in private rather than in the newspaper :-)
I have a follow up question regarding a different matter, if anyone could be so kind as to help me with it.
I have seen a number of posts asking about the density of copper sulphate, however, none of them point to the answer that I would like to see. This would be a data base, preferably online, that contained density and viscosity data for electrolytes. Is such a list available anywhere? Obviously I have used an internet search engine to find one, but with no luck. Thank you in advance for any help on this matter.
student - Sheffield, UK
2004
A. Andrew,
"This would be a data base, preferably online, that contained density and viscosity data for electrolytes. Is such a list available anywhere?"
www.chemspider.com might be the kind of thing you are looking for. There are many more chemical databases out there, but chemspider should be a good jumping off point.
Mike
- Galway, Ireland
December 11, 2009
by Blum & Hogaboom
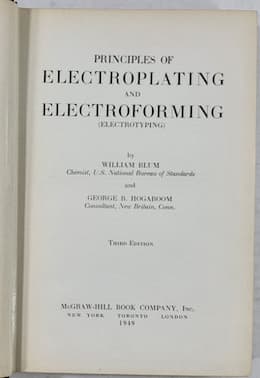
on AbeBooks
or eBay or
Amazon
(affil links)
A. Hi Andrew,
The Principles of Electroplating and Electroforming, Blum & Hogaboom (1929 1932 & 1948) &8680; gives a table showing that copper sulphate and of sulfuric acid give the same effect on specific gravity according to the number of grams per litre in a solution.
The book may be in the university library.
I carry out "gasless" copper deposition on a regular basis.
the vulcan cylinder record company - sheffield england
December 20, 2009
Q. Hi
I have just read with interest the chat between Ted Mooney and Andrew Garrard (Sheffield Uni) re: the effect sulfuric acids has on the electrodeposition of copper onto a copper electrode.
I am growing thin (~100nm thick) copper films on a (gallium arsenide) semiconductor surface by electrolysis, using ~0.3 M copper sulphate solution. I have found that upon adding sulfuric acid the films have been much more uniform (as you were suggesting in your previous discussion), and that on a microscopic level it also contributes to film smoothness.
My aim is to grow a uniform, but rough film. I have found that the addition of a chloride to the acidic solution, or the use of HCl, results in a macroscopically uniform film, which is microscopically rough, and the roughness, i.e. the structures that form are of interest to me.
Do you have any idea as to why the addition of chloride to the solution has this profound consequence? I have read many a journal which say 'it has been shown that Cl- ions have this effect on the surface' but cannot find any description of the mechanism, or of why it has this effect.
Can you offer any insight?
Many thanks,
- Bristol, England
2006
A. I am not a theorist and really can't help much. The best book on such matters is probably Safranek's "The Properties of Electrodeposited Metals and Alloys" ⇦[this on eBay , Amazon, AbeBooks affil links] , but you might do a search for "Rolf Weil" who conducted a number of research projects on similar issues for the American Electroplaters and Surface Finishers Society (NASF).
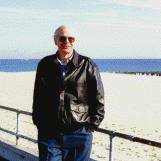
Ted Mooney, P.E.
Striving to live Aloha
finishing.com - Pine Beach, New Jersey
Q. I am trying to plate copper at 0.34 v in a CuSO4 solution. The anode material is getting covered in what looks like a finely divided black powder. The majority can be easily brushed off the anode surface, but some settles into (or possibly forms in) surface pores of the anode and is not easily removed. Is this the smut that is referred to in this thread? Could it be a copper oxide? Suggestions on preventing it? Could increasing solution mixing or bubbling air into the bath solution stop this? Anode surface area is significantly larger than cathode surface area.
Becky windwoodR&D - Portland, Oregon
January 13, 2012
A. Hi, Becky.
The anode is the positively charged electrode. I note this because the opposite definition finds use in electronics, and things will get confusing if we are thinking of opposite poles. Nothing should deposit on it; rather, it should be dissolving. In that case, the black smut is usually the impurities in the copper, that did not dissolve along with it. (The cathode is the negatively charged workpiece upon which electrodeposition occurs).
Regards,
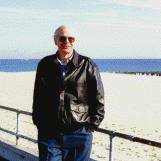
Ted Mooney, P.E.
Striving to live Aloha
finishing.com - Pine Beach, New Jersey
Q. Great article, two questions:
1. I get that the copper sulphate solution has to be acidic, but what pH exactly? 1.0? 5.0? Does it matter? Can it be TOO acidic?
2. The article says that as the electroplating goes forward, the solution becomes progressively more basic and acid needs to be added. I don't understand how that is possible. I have set the current so that no hydrogen is being evolved (that I can see anyway). Oxygen on the other hand is evolving vigorously at the anode. That oxygen is coming from the cracking of water molecules. For every O2 molecule that is made, 4 H+ ions are being added to the solution! Since they're not being converted to hydrogen gas at the cathode (at least in quantities comparable to the oxygen evolving), how are they not making the solution progressively more acidic?
Thanks,
Ray
- Santa Monica, California, USA
May 30, 2012
A. Hi Ray.
1. Sorry, I don't know the pH of typical copper sulphate plating baths, but it's probably somewhere around 2.0; my texts all specify the sulfuric acid ratio rather than pH.
2. Your theory that the pH will rise if O2 gas evolves and H2 gas does not, is absolutely correct--
At the cathode, some portion of the electrons go towards converting water to hydrogen gas and hydroxide ions. Say that 4 electrons are available for this:
2H2O => 2H2^ + 4(OH)-
Whereas at the anode, some portion of the electrons go towards converting water to hydrogen ions and oxygen gas. The deficit of four electrons will cause:
2H2O => 4H+ + O2^
In this balanced condition the pH will neither rise nor fall, and two parts of hydrogen gas will be evolved for each part of oxygen gas.
Excessive hydrogen evolution, though, causes the pH to rise and excessive oxygen evolution causes it to drop (as you report). My question would be why is your anode gassing and your cathode not? Usually, anodes are larger than cathodes, so dissolution is favored over plating. Usually concentrations are fairly low so dissolution is favored over plating. Are you perhaps using a very small anode or an anode which can't dissolve, rather than a copper anode? Any chance your anode is coated or lacquered so it is not dissolving? It is not uncommon in plating for the anodes to polarize (stop dissolving).
Regards,
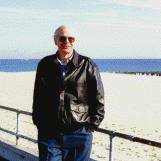
Ted Mooney, P.E.
Striving to live Aloha
finishing.com - Pine Beach, New Jersey
Q. You are correct, Ted. The anode is a tiny strip of platinum, maybe 1 cm x .4 cm max. The cathode is a large piece of copper foil, about 8 cm x 20 cm. I have about .8 amps going for a current density of 5 mA/cm2 (roughly). I was using a graphite anode, but it was dissolving and I was worried that graphite dust would get incorporated into the copper plate.
The pH is at 1.5. I'm planning on raising it as I go by adding copper hydroxide/copper carbonate
⇦this on
eBay
or
Amazon [affil links]
, which will also replenish the copper.
Incidentally, the platinum strip doesn't look like it's being affected at all, but do I have to be concerned about it dissolving over the long term?
Thanks,
Ray
- Santa Monica, California, USA
May 31, 2012
A. Hi. Platinum (or platinum clad titanium) anodes are commonly used as DSAs (dimensionally stable anodes). The platinum will not substantially dissolve, I guess it's too noble.
Regards,
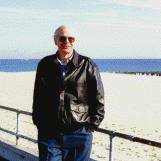
Ted Mooney, P.E.
Striving to live Aloha
finishing.com - Pine Beach, New Jersey
A. Mr. ray, in a CuS04 electrolyte, acidity shall be increasing due to Cu ions deposition at the cathode and the S04 radical goes to Cu anode takes Cu ions to become CuS04 and again deposits Cu on to cathode. In this process Cu metallic ions are continuously removed leaving behind more SO4 radicals resulting in increase of acidic pH3 to O.1 if you do not replenish with CuS04. The best method is to replenish with a concentrated CuS04 by DRIP method to maintain equilibrium constant. Secondly add MnO2 in ppm level to avoid polarisation, i.e., bubbles sitting on cathode interrupting the deposition of copper.
chennamallu prakasham- Chennai, tamilnadu, southindia
May 29, 2015
Q. Dear Sir,
I want to ask a few questions:
1. What is the effect of H2SO4 pH for dissolving Cu with the copper that yield from electrolysis? Is there any equation that provides that, or using stoichiometry to calculate pH from limiting H2SO4?
2. What is the effect of voltage on copper electroplating? Is there any equation besides Nernst equation or there's any other equation related to it?
For your information, first of all, the solution is from chalcopyrite roasting which is dissolved in H2SO4 before electroplating.
- Tangerang, Indonesia
January 30, 2018
A. Hello David, the role of H2SO4 in a acid copper bath has multiple advantages. It is a vital part of the electrolyte where throwing power is essential. It also keeps the copper sulphate soluble in solution. It also keeps the pH of the bath stable. If too much H2SO4 is in a bath it speeds up the deposition rate and plays havoc in metal distribution across the part. Think of voltage as resistance. Cathode to anode spacing, condition of buss bars, contacts and rack or barrel conditions. A low H2SO4 level in the bath increases voltage. Maybe these answers to your questions can be applied to your process. Best of luck.
Mark BakerProcess Engineering - Phoenix, Arizona USA
Q. Hello,
I went through the interesting discussion and got good insights. I am trying to use copper electro-deposition as a process to calibrate my equipment. For that I am using acidic copper sulphate bath (Acid is sulfuric acid). To have a better control on cathodic reactions; I ran some potentiodynamic tests to find a potential range where most of my cathodic reactions were dominated by copper reduction, however while doing so; I have a couple of doubts:
1. since I am using sulfuric acid (pH~1.5), and my substrate is mild steel; would there be a considerable effect of my steel sample dissolution?
2. I am getting a very high values of cathodic current densities; but I would like to deposit only about 1 mg of Cu on steel surface of 1.5 cm2. What is the possible suggestions to do potentiostatic depositions wherein I can reduce current density values?
I tried reducing the conc. of copper sulphate and sulfuric acid; the current density values did reduce but the whole nature of the potentiodynamic curve also changed.
Suggestions in this regards will be much appreciated.
- Athens, Ohio, USA
July 22, 2019
A. Hi Kushal. I'm not sure which electrochemical law you are trying to use to calibrate your equipment, and in what way you are trying to calibrate it ... but copper will spontaneously plate onto steel, corrupting the usual Faraday's Law relationship. You will likely get an efficiency in excess of 100%.
Regards,
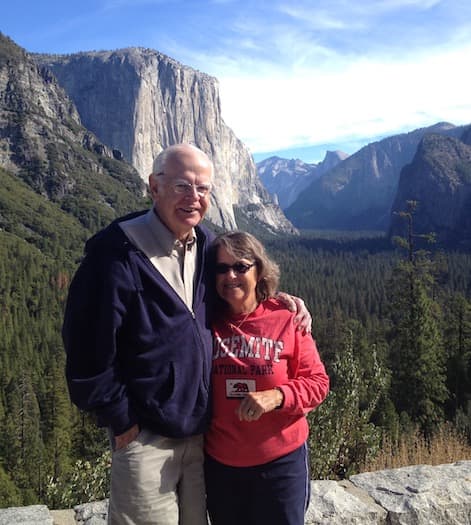
Ted Mooney, P.E. RET
Striving to live Aloha
finishing.com - Pine Beach, New Jersey
A. For a thin adherent copper layer deposit on steel I suggest using 1 gram of copper sulphate, 5 grams of sodium chloride, 10 grams of tartaric acid ⇦this on eBay or Amazon [affil links] dissolved in a small quantity of DI water.
Marvin Sevilla- Managua Nicaragua
Q. Hi everyone. Currently I'm working on troubleshooting rejection in rough deposit involving Acid copper bath tank. Usually after maintenance, rough deposit comes in the first day and becomes better after that. But nowadays, the thing became opposite. After we do some cleaning for that tank it comes out with 0% rejection on rough deposit; but after that, rejection for rough deposit increases from 0% to 80%. It doesn't make any sense. I believe something goes wrong with the solution. Maybe there is precipitate forming during the process? Can you explain what causes can make it that way? And what can I do to overcome it. As you read your conversation above, can putting some acid help to throwing powder. And this condition might be apply to my condition?
Mal AZ- Johor, malaysia
August 17, 2019
A. Hi Mal. Is the roughness primarily on the top of horizontal surfaces, i.e., "shelf roughness"? If so, I would suspect torn anode bags and/or a poorly functioning filter. If the roughness is everywhere I would probably suspect loss of required addition agents. Try a Hull Cell test to see if the problem is definitely a solution imbalance.
We may be having a language difficulty, but there is no such thing as "throwing powder", so that is not the cause of the roughness. "Throwing power" refers to the capacity, ability, or power of the plating solution to achieve plating in low current density areas. A plating solution with high throwing power will tend towards offering an even plating thickness whereas a plating solution with poor throwing power will exhibit far greater plating thickness in the high current density areas like edges and corners. Good luck.
Regards,
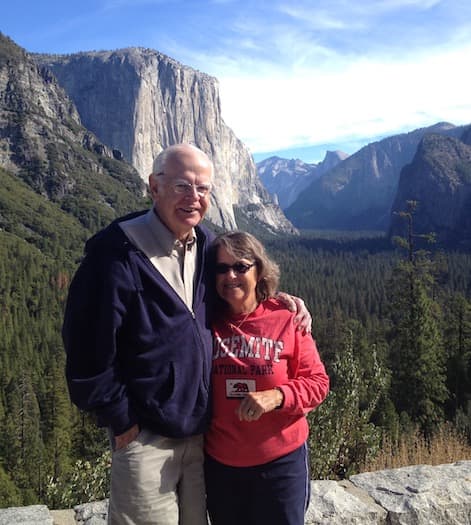
Ted Mooney, P.E. RET
Striving to live Aloha
finishing.com - Pine Beach, New Jersey
A. Hi Mal
A common cause of roughness is solid particles in solution.
A simple test is to take a sample in a glass container and shine a narrow beam of light through it. Light scattered by particles is usually obvious. This is the Tyndall effect.
As Ted says, a punctured anode bag is a common cause but it could also be a badly fitting filter element or simply general shop debris that is not filtered properly.
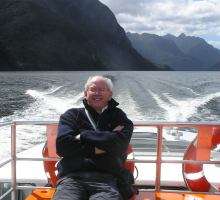
Geoff Smith
Hampshire, England
Q, A, or Comment on THIS thread -or- Start a NEW Thread