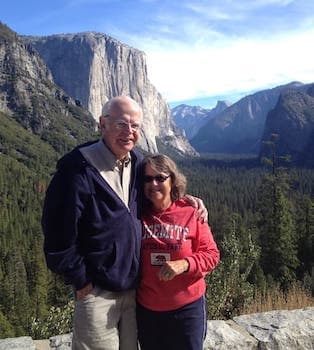
Curated with aloha by
Ted Mooney, P.E. RET
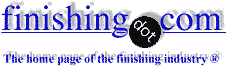
The authoritative public forum
for Metal Finishing 1989-2025
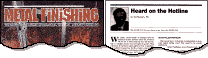
-----
Roughness in acid copper while plating gravure cylinders
adv.: Supplier of Copper Anodes, Nickel Anodes, Bismuth Metal, & Other Metal Products for Industry & The Arts
Q. I have damage in my printing machine. It's in the main Cylinder. Attached is a photo of this damage
I heard about brush plating for filling copper into this damaged area. I searched on the internet but all the plating I found is not giving me filling, it's just coloring. The layer maximum is 5 microns. For that I need the solution to fix this damage by brush plating.
I found some of this chemicals on Alibaba but it's very hard to import it because the police department is concerned about bomb making.
Electrochemical Metallizing by Marv Rubinstein
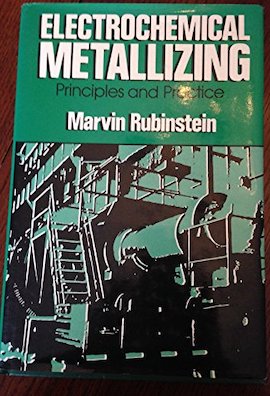
on AbeBooks
or eBay or
Amazon
(affil links)
- Alexandria, Greece
May 13, 2023
A. Hi Tharwat.
I think you would get better plating, better instruction, and attract less concern from the authorities if you simply buy the correct brush plating solutions & equipment from a specialist brush plating supplier. That way there also should be no chemicals involved that should involve import restrictions.
Perhaps your library -- the best in all the world -- has or can get you a copy of "Electrochemical Metallizing" [on
eBay,
Amazon,
AbeBooks affil links], a great book about brush plating, and which covers repairs and printing industry applications.
Luck & Regards,
Ted Mooney, P.E. RET
Striving to live Aloha
finishing.com - Pine Beach, New Jersey
⇩ Related postings, oldest first ⇩
Q. Sir, we plate gravure cylinders in acid copper bath and use normal copper anodes with the bath composition of 250 gm/lt copper sulphate, and 25-30 ml/lit of sulfuric acid, as the cylinder dips in the copper solution only 15-20% and run the bath at 4 amp/dm2. Now my problem is upon operation with the above conditions the cylinder is getting rough deposit on the surface. I suspected suspended particles, and filtered the solution, and even carbon treated the solution. I suspected high current, and controlled and operated at 4 amp/dm2, I even suspected the copper anodes, as they were found black, so replaced them with phosphorized copper anodes, still problem persists. Copper metal and acid are in range. So I kindly request the professionals to suggest , what could be the problem , and how to get rid of this roughness. Awaiting for the reply, in detail.
Thanking you, Sincerely yours,
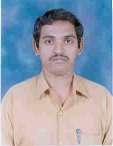
Panjala Mukesh
fashion jewelry mfgr.
Hyderabad, India
2004
A. FIRSTLY I WOULD SUGGEST TO ANALYZE YOUR BATH PROPERLY. KEEP PROPER CONC. OF sulfurIC ACID IT HELPS IN REDUCING THE TENDENCY FOR ROUGH & TREED DEPOSIT. KEEP CONC.AS copper sulphate
⇦ this on
eBay or
Amazon [affil links] 160-225 GM/LTR, sulfurIC ACID 50-75 GM/LTR, USE GOOD QUALITY CHEMICALS, CONTINUOUS FILTRATION, WITH PROPER AGITATION, ROOM TEMP.
START CURRENT DENSITIES:- 1-3 AMP/DM2 PHOSPHORIZED ANODE .02-.04% A BLACK ADHERENT ANODE FILM IS FORMED WHICH ENCOURAGES UNIFORM ANODE DISSOLUTION AND REDUCES PARTICLE FORMATION DUE TO ANODIC DISINTEGRATION. USE ANODE BAGS.
GOOD LUCK
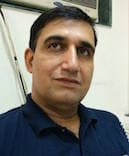
Ajay Raina
Ludhiana, Punjab, India
Q. Bath concentration is perfect, double checked; copper sulphate is 250 gm/lt and sulfuric acid 30 ml/lt, operated at 4 amps/dm2 at these conditions even deposition for 500 microns it is taken around 15 hours with rough deposit, normal copper anodes turning black , so replaced with phosphorized copper and inducted 60 ppm chloride, with continuous bath filtration , and even solution hot carbon treated and filtered , still the problem of roughness persists. Kindly advice is the bath composition is correct? or do we need to change the bath composition to avoid this roughness and for speedy deposition? We do not use any additives in the bath.
Anyone with this expertise , kindly suggest.
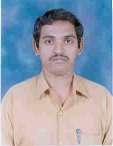
Panjala Mukesh
fashion jewelry mfgr.
Hyderabad, India
A. The usual reason for a rough coating is a contaminated bath. I would suggest you use a 0.5 micron (or smaller) filter and use a flow rate of at 6-8 tank volumes per hour. (If I was electroforming, I would use 8-10 T/O per hour). Make sure you have good polypropylene anode bags that have not got holes in them. Operate the copper bath at 220 g/l CuSO4 and 50 ml/L H2SO4 (SG 1.84). Increase the chloride to 100 ppm. The temperature should be between 25 and 30 C. The anode area should be about double the cathode area. The cathodic CD should be OK at what you have.
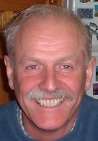
Trevor Crichton
R&D practical scientist
Chesham, Bucks, UK
A. Problem seems in your filtration. CHECK FOR LOW ACID CONTENT. EXCESS CURRENT, LOW TEMP, LOW CHLORIDE CONTENT, CHLORIDE CONC. 60-100 PPM. WHEN COPPER IS TO BE DEPOSITED FROM ACID BATHS ON STEEL MUST FIRST RECEIVE A CYANIDE COPPER OR NICKEL STRIKE THE STRIKE MAY BE AS THIN AS 2 MICRONS. AFTER THE STRIKE PARTS SHOULD BE DIPPED IN A DILUTE SOLUTION OF sulfurIC ACID TO NEUTRALIZE SOLUTION RETAINED FROM THE ALKALINE STRIKE BATH. THE PARTS SHOULD BE THEN RINSED BEFORE ACID COPPER PLATING. INCREASE sulfurIC ACID CONC.30-45 ML\LTR.
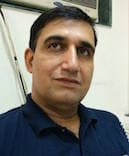
Ajay Raina
Ludhiana, Punjab, India
![]() |
Q. Thanks for the reply , I have tried by increasing the solution turnover and kept 5 micron filter cartridge, still my problem persists, if I operate it 4 amp/dm2 , rate of deposition is very low, I want an accelerated rate , so kindly suggest what kind of bath concentration to be used for gravure cylinder plating , and how to wrap the PP cloth to the anodes. If any additional information is appreciated . ![]() Panjala Mukesh fashion jewelry mfgr. Hyderabad, India A. PROBLEM SEEMS IN YOUR FILTRATION. ROUGH DEPOSIT CAUSES:- LOW ACID, EXCESS CURRENT, LOW TEMP, LOW CHLORIDE CONTENT, SUSPENDED IMPURITIES IN THE BATH. FOR AIR AGITATED BATH CHLORIDE 60-100 PPM. INCREASE sulfurIC ACID CONC. 30-45 ML/LTR. WHEN COPPER IS TO BE DEPOSITED FROM ACID BATHS ON STEEL, MUST FIRST RECEIVE A CYANIDE COPPER OR NICKEL STRIKE,THE STRIKE MAY BE AS THIN AS 2 MICRONS. AFTER THE STRIKE PARTS SHOULD BE DIPPED IN A DILUTE SOLUTION OF sulfurIC ACID TO NEUTRALIZE SOLUTION RETAINED FROM THE ALKALINE STRIKE BATH. THE PARTS SHOULD BE THEN RINSED BEFORE ACID COPPER PLATING. ![]() Ajay Raina Ludhiana, Punjab, India |
A. Mukesh it sounds as if your acid level is too low. Check it out. I also think your filters are too large, use 0.5 micron filters, not 5 micron. Thirdly, I take it you are not using anode bags as you ask how to wrap polypropylene around the anodes. Anode bags are what they say, they are bags that the anodes go into. You MUST use anode bags with copper anodes, otherwise you run the risk of getting particulates into your solution and this will result in a rough deposit. Once you have the bath and process in specification, then the ccd and throwing power should be OK.
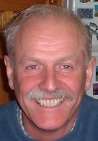
Trevor Crichton
R&D practical scientist
Chesham, Bucks, UK
A. Hello Mukesh,
Check for iron impurity , and also the chloride may be less, causing you treeing effect. I would suggest you use an organic brightener which are specially used for this kind of application where you built up such a high thickness and work and which will allow you to work at higher current density. I hope you can follow my views and check with the best supplier located nearby you.
Thanks and reg,
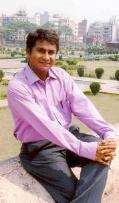
Praveen Kumar
plating process supplier
Mumbai, India
A. Hi Panjela,
I think your want is a major issue here: "if I operate it 4 amp/dm2, rate of deposition is very low, I want an accelerated rate"
Everybody the world over wants to operate at a higher deposition rate, but I suspect that 4 amp/dm2 (40 ASF) is already too high :-(
But in addition, as others have said, better filtration, more acid, and a check for impurities is probably needed. Run some Hull Cell panels ⇦ this on
eBay
Amazon [affil links] and let us know what they indicate please.
Luck & Regards,
Ted Mooney, P.E. RET
Striving to live Aloha
finishing.com - Pine Beach, New Jersey
A. Dear Mukesh,
Add about 10 gms./ltr Potash Alum to your bath. Alternatively you can try Poly Ethylene Glycol for fine grain, roughness-free deposit.
- Mumbai, India
Q. Pitting and drill problem
DEAR RAMESH KHARE
You said "Add about 10 gms./ltr Potash Alum to your bath. Alternatively you can try Poly Ethylene Glycol for fine grain, roughness-free deposit."
Please tell me what is the potash alum. formula (like CuSO4?)
What does the poly ethylene glycol change in the bath? How much poly ethylene glycol per litre?
BEST REGARDS,
- ISTANBUL, TURKEY
2006
A. Hi Ahmet. Polyethylene Glycol is a simple generic "brightener" for home-brew copper plating baths such as are used by hobbyists & artists. It is readily available in the USA as Miralax laxative ⇨.
Briefly, brighteners are attracted to high current density areas and offer shielding against crystal growth, thus causing more adatoms to form for a finer-grained deposit.
In the USA most shops would rely on process suppliers to offer plating baths with proprietary formulations. Plating shops should always have and use Hull Cells
⇦ this on
eBay
or
Amazon [affil links] , and scale up their additions proportionally from the Hull Cell additions. They should never add a material to their process tanks based on theory or rumors ... but for a general sense of the range we're talking about, it will be something like 1 teaspoon of polyethylene glycol per gallon -- a relatively small amount. Good luck.
Regards,
Ted Mooney, P.E. RET
Striving to live Aloha
finishing.com - Pine Beach, New Jersey
Q. Ramesh, can you briefly discuss the chemistry about the using for potash alum in copper bath?
Gaurav sharma-noida, India
December 31, 2023
Ed. note: Ramesh didn't reply in 2006 and e-mail to him is likely to bounce 17 years later, but we'll try. Hopefully other readers are familiar with this potash alum addition to the copper plating process and will jump in.
A. Hi,
I am working in same rotogravure cylinder plating only, I used to Plate average 300 micron in 2 hours with a bath composition of 220-240 gms/lit of copper sulphate content and 60-65 gms/lit of sulfuric Acid. Ours is half immersion plating, so we are giving around 12.5 amps/dm2 to get a good finish without roughness.
- Cuddalore, TamilNadu, India
June 21, 2016
A. You also increase for current density. Fix this around 22-25 amp/dm2 then you can get fine plating
Gaurav sharma- Noida, India
December 31, 2023
Q, A, or Comment on THIS thread -or- Start a NEW Thread