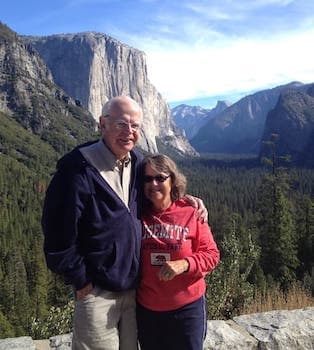
Curated with aloha by
Ted Mooney, P.E. RET
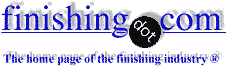
The authoritative public forum
for Metal Finishing 1989-2025
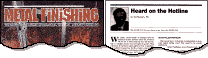
-----
Need help about Zinc plating properties and procedures
Q. Hi mate, please help me about "Zn plating" Information (properties of coated layer, procedure of Zn plating, tests, problems, ...)
Thanks.
plating shop - Isfahan, Iran
2004
A. Hi, Reza. There are at least three broad classes of zinc electroplating solutions (cyanide, acid, and alkaline non-cyanide) and each has somewhat different properties, procedures, tests, and problems. But the short answer is that zinc plating is a sacrificial coating that is very versatile and inexpensive. It is, however, being rapidly supplanted by alloy zinc platings like zinc-cobalt, zinc-iron, zinc-nickel, and tin-zinc because they offer more corrosion resistance.
Many professionals spend their whole career doing nothing but zinc plating, so it's a pretty broad topic. Try to get hold of a copy of "Zinc Plating" [on Amazon, AbeBooks affil links] by Geduld. That volume should be able to most questions. Good luck.
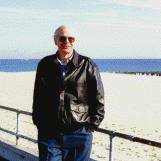
Ted Mooney, P.E.
Striving to live Aloha
finishing.com - Pine Beach, New Jersey
2004
A. Sir:
You need to be more specific. Zinc is a metal that generally is deposited on steel. Depending on the use of the product or the environment, determines the plating thickness. The norm is 8 microns. The procedure is rather simple. you clean, rinse, acid clean, rinse, zinc plate, rinse, pickle, chromate yellow or clear, rinse, dry. Perform adhesion tests and plating thickness tests. The most common problems can be bare spots or non-plate.
- McAllen, Texas
2004
December 19, 2017
Q. Hello,
Recently we have installed an automatic plating plant (rotating barrel type) for zinc plating of fasteners.
So the issue is we just have got stuck for setting up the plating process parameters and validation for the same.
What exactly we want to know is the approximate quantity (mass) of the fasteners to be loaded into a barrel and the voltage required for that, as we are a fastener manufacturer so as the size of the fastener is changed then according to that we also have to change the process parameters due to the surface area concept.
As the plant is automatic and the program is same for all the products there will be no change into the plating time, electrolyte, and plating thickness required (our requirement is 10 micron to 15 micron); what we have to change is
1) the quantity of the fasteners to be loaded
2) the voltage or current requirement through out the process
I have gone through the basic calculation and made a sheet that requires following data as an input:
1. Total surface area to be plated
2. plating thickness required
3. mass of one bolt without plating
4. Total mass of a lot to be loaded into barrel
5. plating thicknesses required
And got the following output:
1. Voltage and current required
But the result we got does not comply with that of the actual process taking place so is there any other parameter that we are forgetting to be considered
Kindly help for the same.
- Rajkot, Gujarat, India
Hi Bhavik. Plating barrels come in different sizes from thimble size to quite large, but for industrial zinc plating the practical range is probably from about 14" inside dia. x 30" inside length to about 21" dia. x 72" long. If you can tell us the size of your barrels, people can give you the benefit of their experience regarding surface area and weight. It's pretty common to plate anywhere from about 75 pounds of fasteners to about 300 pounds per load depending on the size of the barrel and the size of the fastener (large fasteners obviously weigh much more for the same surface area than small fasteners). You also need to tell us whether you are doing acid zinc plating or alkaline non-cyanide.
Your equipment vendor should be giving you a little help, and your chemical process vendor should be giving you a lot. But if they are not, electroplating consultants can certainly help you.
I think you also should be trying to hire an experienced zinc plater. It sounds like you may be hoping you just turn on this automatic plating machine and have it start producing satisfactory work, but I'm afraid that there is a lot more to it than that :-)
Luck & Regards,
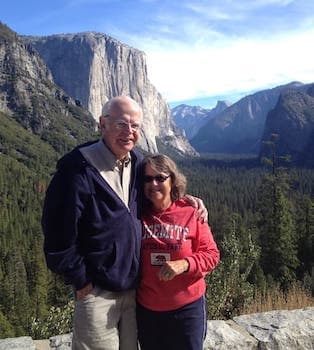
Ted Mooney, P.E. RET
Striving to live Aloha
finishing.com - Pine Beach, New Jersey
December 2017
December 20, 2017
A. Hi Bhavik!
As Ted said, tell us:
Size of the barrels.
Plating time (if you can at this time, try to make this parameter variable, as you could make more production in some cases and you may need to increase time for some bolts to make up to 10-15 microns in acid zinc plating).
Acid (Potassium/Ammonia) or Alkaline (Cyanide/Non) zinc plating?
Cathodic bars or danglers? Difference of conductivity between one or another will change the potential needed to achieve the desired thickness.
I think that with this data we could help you, BUT you will need to check and adjust there for each bolt/fastener to get the best parameter for optimizing productivity, thickness and quality of the applied coating.
We look forward to hearing from you again!
TEL - N FERRARIS - Cañuelas, Buenos Aires, Argentina
Q. Thanks for replying.
Here is the data regarding plating process that you have asked for:
1. Process type : Acid zinc plating
2. Electrode used : Danglers
3. Barrel size : dia. 24 inches (hexagon type), length 60 inches
4. Plating time : 50 min.
- Rajkot, Gujarat, India
December 22, 2017
A. Hi Bhavik. Those are quite large barrels, probably capable of holding 300 pounds or more per load, maybe 500 pounds. You will probably be operating at 10 to 12 Volts (be careful about destroying titanium anode baskets with too high a voltage), and perhaps 1000 to 1500 Amps depending on fastener size. But I don't understand how you'll know whether this is too much or too little if you don't have an experienced acid-zinc plater, technical service person from your chemical supplier, or consultant on hand evaluating it.
The idea that you can set parameters on an automatic plating machine from book knowledge and just start plating is, in my experience, completely unrealistic. Good luck.
Regards,
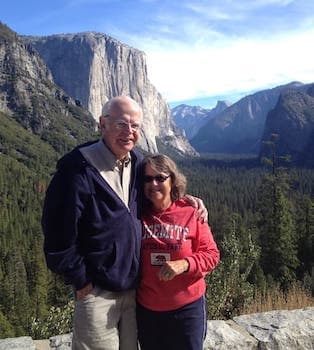
Ted Mooney, P.E. RET
Striving to live Aloha
finishing.com - Pine Beach, New Jersey
December 2017
A. Bhavik, a decent rule of thumb, with several exceptions, is to plate at the same amperage as the weight in the barrel. With acid zinc chloride plating the chemistry we use strongly suggests not pulling above 9 Volts to ensure you do not polarize the anodes. Also, if you are not experienced with barrel plating be careful with your larger fasteners as you may experience chipping as they bounce off each other in the barrel. A nice fix is to run a smaller dummy load of ball bearings or even fasteners that can absorb that energy with the larger fasteners. Also, depending on the thickness required you may be able to run the barrel for a shorter amount of time, just run it for 20 minutes, test the thickness, and put it back if it is not enough. Let us know how everything is working out.
Jordan EgnatoffTri-State Plating - Huntington, West Virginia USA
January 18, 2018
Hi Bhavik!
Tell us if you could solve this on your own. We have barrels approx. that size, but with cathodic bars because danglers break too often with our products. We load 120-200 kg (265-450 lb) maximum, and we use up to 1500 A for 80 min.
The amount of surface depends on the type of parts you plate, so you should adapt your parameters for every product and try to group them so it's easier to set up for process.
Anode baskets did not work for us (long story), so we use zinc hanging by copper hooks and it works very well, as we change them when they are "spent" and we melt them to make new ingots for us to use.
Hope you can solve your issue! Best of luck!
te - Cañuelas, Buenos Aires, Argentina
February 7, 2018
"1500 A for 80 min." -- Sounds like you're doing good heavy plating, Daniel! Congrats, I'll have to look for your fasteners :-)
Regards,
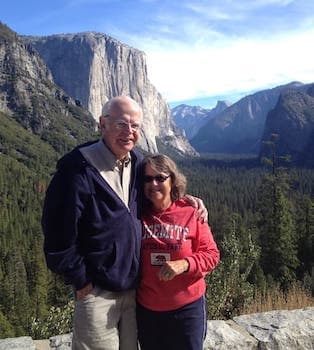
Ted Mooney, P.E. RET
Striving to live Aloha
finishing.com - Pine Beach, New Jersey
February 2018
A. Hi Ted!
Yes, very small screws need very high current, 4 barrels with around 4800 A deposits zinc with 7-8 micron thickness. Each barrel contains 70 m2 of approximate surface area, and not all of this area is exposed at the same time (this is one of the reasons for the wheel to rotate), so it's really a matter of try-and-see what you get :)
The cathodic bar contact is not the best conducting agent, so you need to raise the voltage a little when you use those, so you can't have some barrels with danglers and some with cathodic bars because they have significantly different parameters.
Really (because of the design of our automatic line) we can't plate there for less than 56 minutes. So, we need to adjust our parameters to our line limitations, as every plater I can think of.
So... If I can help in any way and have some time in my hands, I'll be around!
TEL - N FERRARIS - Cañuelas, Buenos Aires, Argentina
February 8, 2018
A. Hello again, Daniel. I designed automatic plating lines for 40 years, so I understand what you are saying. But 7-8 microns is a good thickness for most purposes; some USA shops/customers use the rather meaningless term "commercial quality" to justify plating thicknesses of about half that for barrel plating of fasteners so they don't have to adhere to a 5 micron minimum :-)
Regards,
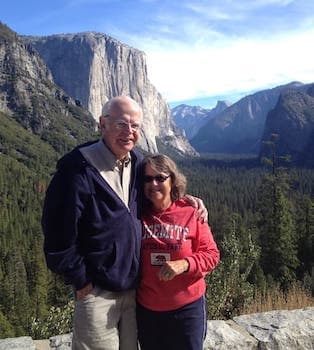
Ted Mooney, P.E. RET
Striving to live Aloha
finishing.com - Pine Beach, New Jersey
February 2018
Q, A, or Comment on THIS thread -or- Start a NEW Thread