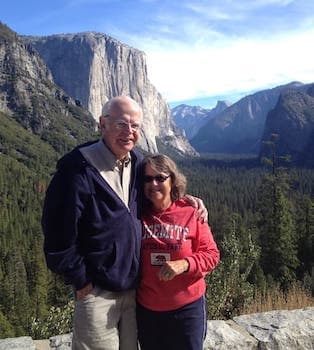
Curated with aloha by
Ted Mooney, P.E. RET
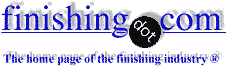
The authoritative public forum
for Metal Finishing 1989-2025
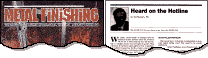
-----
Electroplating in Nanostructures, rate control
My situation may be a little different from the ordinary questioner at this website. I'm currently conducting my diploma thesis, working with construction of nano-structures through electro-plating. Our structures have a very high aspect ratio, mainly by being 30nm wide. My problem now is to accurately predict the time when my structures have grown to a height of approx. 200 nm. Using a Nickel-Sulfamate solution at the optimum specifications. These experiment are conducted in a clean room and in small scale. Say that the rate is 30nm ± 5 nm / min, is there anyway to improve upon this?
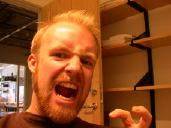
Patrik Nordstrom
diploma thesis - Stockholm, Sweden
2004
The rate of deposition is limited by mass transfer considerations. i.e. replacing the metal ions in the layer next to the substrate from the bulk electrolyte. There are several ways of increasing the limiting current density.
More ions - increase the concentration Increase the rate of diffusion - increase temperature Increase ion transportation - mixing. You can try ultrasonics but the most practical way is probably to jet the solution onto the deposition site. If you can find a small platinum tube to use as a nozzle, this can be used as the anode too. I would expect this method to have at least an order of magnitude increase in plating rate.
Good luck.
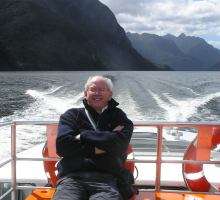
Geoff Smith
Hampshire, England
2004
2004
I may have expressed my question unclear since you answer doesn't really address my problem.
I'm interested in plating as accuracy as possible 150nm thick layer of nickel as uniformly as possible into deep recesses, aspect ratio 5:1. I will further explain my setup. The main problem is size, my plated structure is approx. 0.1 square millimeter large. My conducting clamp although the size of a needle is considerably larger than this area. I now use a sacrificial cathode just to avoid the need for a stable nano-Ampere current source. Typical current density is 0.125 A/dm2, is is low due to achieve desired plating rate of approx. 40nm/min. Due to the fact that my structures are 30nm thick and 150nm high the risk of tilting has made us skip stirring. Currently this setup is the size of a teacup.
Or in other words is it possible to accurate predict the time it will take to reach a 150nm layer Nickel within a reasonable time frame, using any setup? The structures are produced by lithography, although very accurate this area differs with 5-10%.
Greetings from sunny Stockholm, Sweden. Patrik " Nickel-head " Nordström
- Stockholm
2004
The trick to getting a uniform deposit is to have a uniform cathodic current density. Since your workpiece is so small, you can use the carrier as a robber and maintain a good localised current density distribution. This will promote a uniform layer. However, your real problem is trying to determine the exact current density at your active site. Once you know the exact current density and the plating efficiency, you can calculate the plating time. About 15 years ago a computer program was developed by Prof Malcolm McCormack at Sheffield University (UK) for determining the plating distribution by using local current density patterns, but he has since left and I am not sure where he now is. Try contacting the IMF in the UK, they may know.
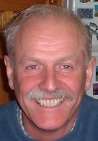
Trevor Crichton
R&D practical scientist
Chesham, Bucks, UK
2004
A robber? Not familiar with the term, but if you are referring to a larger cathode area which is not a part of the active part, that is what is currently used. The dummy cathode uses 99% of input current on a test chip and perhaps 30 microAmps passes through the chip connected to the cathode. This share increases to maybe 50 microAmps in the end of the process. If this is due to decreased resistance, either by an increasing surface area or that the metal is altered from Ge to Nickel.
Patrik Nordström- Sweden
2004
Q, A, or Comment on THIS thread -or- Start a NEW Thread