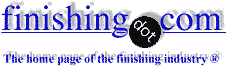
-----
Chilling/cooling of anodising bath Q&A's

Disambiguation: Please see also --
• Topic 58129, "Cooling of home/D-I-Y anodising baths"
Q. Currently doing some small shop type 2 anodizing and am having issues with the sulfuric acid bath heating up. I have seen posts about using a titanium coil/heat exchanger submerged in the acid with a chiller attached to direct cool the acid. Titanium tubing is on the pricey side and thinking about how aluminum can be used as cathodes, could aluminum tubing be used a substitute for titanium? (Coil/exchanger would not be connected to the anodizing electrical circuit.)
- Baltimore, Maryland
September 8, 2023
A. In my experience this is unlikely to work satisfactorily, certainly not as a long term solution - meaning for more than about a year or two, perhaps.
Not only the aluminium tubing will slowly dissolve in the bath even when no current is flowing, it will also pick up stray currents during anodizing operation (even if intentionally not electrically connected to anything) which will further accelerate the corrosion and dissolution.
We have (unsuccessfully) tried something similar during initial R&D of our current anodizing line - as an expedient due to not having the right materials on hand, we used a copper brake pipe for the air sparger, since copper does not appreciably dissolve in sulfuric acid under normal conditions...
But the sparger was actually carrying a stray current even though it was at the very bottom of the tank and mechanically not connected to any other metal objects in the tank, this was causing severe corrosion of the copper pipe and resulting copper contamination of the bath.
So unfortunately, this will not work.
The only acceptable metallic materials for a submerged coil type heat exchanger in a sulfuric anodizing bath are ones that either instantly passivate (titanium), or have extremely insoluble corrosion products (lead).
There are also other coil materials which may be more appropriate, such as PE or PTFE plastic tubing (but this lacks mechanical strength), or PTFE coated copper pipe (expensive, fragile after installation).
But again in our experience, the superior solution is to use a properly designed stacked plate heat exchanger and a circulation pump. Much easier and simpler to install and maintain, although the initial cost is somewhat high.
Using an external heat exchanger also simplifies the control arrangement for the thermostat, since all you need is to switch the circulation pump on and off - or use a VFD for the pump with analog control if you want very close control over the temperature; this is what we do.
- Czestochowa, Poland
September 10, 2023
Thank you, P.H.,
you reminded me that it is impossible to avoid corrosive stray currents :-)
Readers can search the site for the topic "bi-polar anodes" for details, but briefly: metal is much more conductive than anodizing solution, and electricity favors the path of least resistance, so anytime you have plating or anodizing current flowing, electricity will always take the shortcut through any "neutral" metal in the solution, making one face of it cathodic and the other face anodic.
Luck & Regards,
Ted Mooney, P.E. RET
Striving to live Aloha
finishing.com - Pine Beach, New Jersey
Q. The set-up is in 5 gallon buckets and runs are done once or twice a month so the coil would be pulled when not in use. I was looking at 3003 alum .049" walled tubing on McMaster (mcmaster.com/5177K67-5177K47/) as an option but do not know how it will react in the acid bath.
For the volume I do it's hard to justify the price of titanium tube vs aluminum as the anodize work isn't steady incoming work. Kind of a hassle for me but the capability has its perks ...
If there isn't a risk of putting the 3003 alum coil in and it dissolving after 8 hrs of use then it may be the route I take.
Alternatively, going the lead route, I cannot find lead tubing on McMaster. Is there a good supplier for lead tubing roughly 1/4-1/2 Dia?
- Baltimore, Maryland
September 11, 2023
A. Hi MC. The cheapest solution is probably to just coil 50 feet of vinyl tubing into your bucket
Luck & Regards,
Ted Mooney, P.E. RET
Striving to live Aloha
finishing.com - Pine Beach, New Jersey
⇩ Related postings, oldest first ⇩
Q. We are doing hard anodising in India. We are having chilling plant for cooling our sulfuric bath by indirect chilling method. We want to chill our bath by direct immersion of coils in H2SO4 bath. Can we use SS 316 tubes or lead tubes for this purpose? Inside the tube we are using R22 gas. Please give us your suggestions.
ELANGOVAN DAMODARAN- INDIA
1999
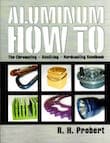
Aluminum How-To
"Chromating - Anodizing - Hardcoating"
by Robert Probert
Also available in Spanish
You'll love this book. Finishing.com has sold almost a thousand copies without a single return request :-)
A. Yes, this has been done with lead coils. However, I think you are making progress in the wrong direction. Here in the U.S. many shops are doing exactly the opposite: converting from direct cooling to indirect! Most seem to think it's inappropriate to be pumping refrigerants around a shop and into vulnerable coils in tanks like that.
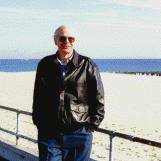
Ted Mooney, P.E.
Striving to live Aloha
finishing.com - Pine Beach, New Jersey
A. Although direct cooling is more efficient, the chance of acid being introduced into the chiller is a very real and serious problem. In addition, with indirect cooling more precise control is possible with modulating valves. Also, indirect cooling provides a cooling buffer to minimize chiller on and off.
Jeff Pernick- Detroit, Michigan, USA
Q. Thank you for your advice and we are doing chilling by maintaining a brine chilling solution in a separate tank and from there we are circulating this chilled water through lead coils to H2SO4 solution in the anodising bath (tank). So there is a temp drop always between brine solution and H2SO4 bath solution. To avoid this we want to chill the H2SO4 solution directly by immersing lead or SS316 tubes in H2SO4 solution. This lead or SS tubes will have freon gas R22 inside them for chilling .
This is our question, kindly help us out of this problem.
Thanking you,
ELANGOVAN DAMODARAN [returning]- INDIA
A. A common way of handling the problem, but it is not cheap, is to use an external heat exchanger. The "brine" flows through one circuit and the H2SO4 through the other. Since there is high velocity and large surface area, it is possible to maintain a small temperature difference (less that 10 degrees F) between the "brine" and the H2SO4. (I put "brine" in quotation marks because we actually use ethylene glycol in the water, not salt brine).
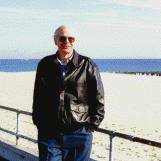
Ted Mooney, P.E.
Striving to live Aloha
finishing.com - Pine Beach, New Jersey
Q. We are in a service of anodising since 1978. But we have a traditional & orthodox procedure but now I want to apply modern technique through you. So please help me to do so. Thanking you.
SACHIN SHARMA (B.E)- Delhi, India
2001
Q. We are doing anodizing in India, we need help for chilling plant we don't know how it's possible. Please guide us.
Manish Pande- Nagpur, Maharashtra, India
2001
A. We have a solution to your need in form of chilling your H2SO4 solution directly through M-22 refrigerant gas, in an all stainless steel heat exchanger outside your finishing tank.This way you can reduce your temperature losses and maintain your acid very close to the refrigerant gas temperature. Also you will avoid refrigerant gas leaking into your finishing tank.
Jittin Gupta- Delhi, India
2003
Q. Kindly assist in the calculation of cooling required in a sulfuric Acid Hard Anodising solution. What size chiller plant is required in a 1000 litre 20 % sulfuric acid solution using a 1000 Amp rectifier up to 80 V for the purpose of hard anodising up to 60 micron thickness. What percentage of current will be transformed into heat.
Thank you,
John KleynPlating Plant and Equipment - Cape Town, South Africa
2004
Treatment &
Finishing of
Aluminium and
Its Alloys"
by Wernick, Pinner
& Sheasby
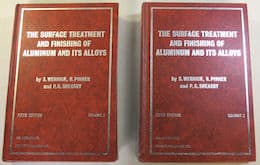
on eBay or Amazon
or AbeBooks
(affil link)
A. Hi John. I have been involved in correcting a number of undersized cooling plants over the years, and I have never seen any indication that less than 100 percent of the anodizing power is converted to heat.
If you are running at 1000 Amps and 80 volts, you will be generating 80 KW of heat. If you are anodizing at this current and voltage 60 minutes out of every hour, you are generating 80 KW-hours of heat or 273,000 BTUs per hour. 12,000 BTUs per hour is a ton of refrigeration, so you're looking at 22.75 tons. Please check my conversion factors because this was a quick on-the-fly thumbnail sketch.
But usually you don't run a rectifier flat-out, and you need to ramp up your voltage, so it can't always be 80 V either. After looking into those duty factors, you'll probably come up with 15 to 20 tons of chilling required.
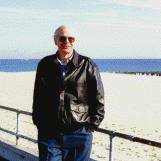
Ted Mooney, P.E.
Striving to live Aloha
finishing.com - Pine Beach, New Jersey
Q. The conventional chilling plants use Brine (Calcium Chloride) as a media for indirect cooling of H2SO4 solution contained in Hard Anodizing Bath. In our firm too a Brine Chilling plant is in operation to maintain -8 °C in Anodizing bath. As brine solution is highly corrosive in nature we are encountering problems, viz., puncture of pipe line due to rust, heavy rusting of pumps and surrounding environment etc due to which plant is under frequent breakdowns. We learnt from you that Ethylene Glycol solution is an alternative for Brine. Please elaborate this by giving the Technical/Chemical/Thermal comparison (from heat transfer point of view) of both the solutions to establish the superiority of Glycol.
Arun Kumar KhamithkarPlating shop Employee - Hyderabad, Andhra Pradesh, India
2006
A. Hello, Arun. Ethylene glycol is automobile antifreeze, and the thermal properties of brine/water and glycol/water are probably reasonably similar. But commercial antifreeze probably includes descaling and corrosion-fighting additives that will somewhat reduce the tendency of scales to form which interfere with the "U factor". If you want to take that tip and run with it, please do. Or if you want to retain a consultant to do an engineering and economic study of the two heat transfer systems for you, please see our Directory of Consultants. But this is a public forum for camaraderie and sharing of quick tips, so we need to warn you that there is little point waiting for someone to undertake a detailed engineering study for you for free :-)
Good luck with it.
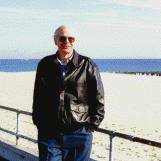
Ted Mooney, P.E.
Striving to live Aloha
finishing.com - Pine Beach, New Jersey
A. I have a suggestion and I think that you wanted to eliminate these problems
1. Improve the efficiency
2. Reduce the heat gained during the circulation of indirect cooling.
You can make a safe approach:
cascade the cooling coils with freon inside a SS case filled with brine(...) immerse this in the tank (cool pack method) that will prevent your coils with freon from being damaged and also avoid to a greater extent the mixing of H2SO4 in the freon or vise versa.
But this will increase your maintenance work in terms of regular check by NDT for any possible hole or thinning of the outer SS shell which contains the brine.
- Bangalore, India but currently Kuwait
Hi Ayzaz,
The concept is interesting, but I think that stainless steel immersed in an anodizing tank is a problem.
Luck & Regards,
Ted Mooney, P.E. RET
Striving to live Aloha
finishing.com - Pine Beach, New Jersey
Q. Greetings,
Over the last several months we have had to replace our Type III Anodize stainless steel heat exchanger twice due to it being eaten up. It appears that the stainless steel is being etched away. The welds are attacked first but the tubes are being attacked as well. The Steel is 347 stainless. Our Solution has been within spec and we have checked for stray current on the heat exchanger itself with none found. The heat exchanger is electrically isolated. We have not had this problem before and prior heat exchangers have lasted for years. Any thoughts?
Best Regards,
Peter
Engineer - Phoenix, Arizona, USA
November 8, 2012
A. Hi Peter.
Regardless of whether or not you are reading stray currents, make sure that you have dielectric unions, or lengths of radiator hose, or some positive electrical insulation in between the anodizing tank and the heat exchanger.
Regards,
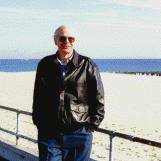
Ted Mooney, P.E.
Striving to live Aloha
finishing.com - Pine Beach, New Jersey
Q. While running a chilling plant, what should be the control parameters to make the plant trouble free? How should be root of the water, control of chilling unit, water pump, etc.
If chillers cooling tube get burst, what is the solution to rectify same?
Paripooran Watsayan - Delhi, IndiaFebruary 17, 2013
A. We are manufacturing chilling plants for Hard anodizing, the sulfuric acid solution is coming directly into the Evaporator. We are using 316L tubes, Tube plates & Shell.
We have had no leakage problems in the evaporators.
CHILLERS - New Delhi, India
September 11, 2014
Q. Is there a separate water inlet to a chilled water plant? Or from the cooling water inlet they get water for making chilled water?
Janaka BandaraSNT automation works pvt Ltd - Sri Lanka
September 16, 2017
by Runge & Kaufman
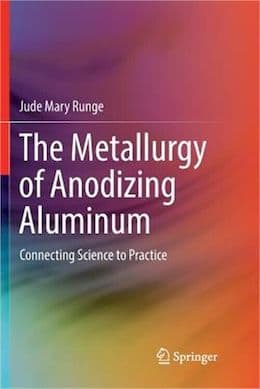
on eBay or Amazon
or AbeBooks
(affil link)
A. Hi Janaka. Unfortunately, that is impossible to answer definitively. Although many systems (including most anodizing chillers) recirculate the chilled water, some chilled water systems might be open loop: for example if you go to a water fountain in your shop, it may chill the potable tap water before serving it to you.
Regards,
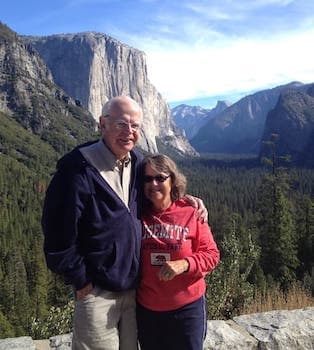
Ted Mooney, P.E. RET
Striving to live Aloha
finishing.com - Pine Beach, New Jersey
Q. What is a thermowell mounting in a chilled water line?
Janaka Bandara [returning]NST Automation Works Pvt Ltd - Sri Lanka
September 19, 2017
A. Hello again Janaka. In certain situations it can be impractical to insert a thermometer or other temperature sensor directly into the liquid. In that case the piping is specially built with a sort of a nest into the pipe so the temperature sensor can be in the middle of the flow but protected from it by metal; this also allows quick change-outs without draining anything.
If at all possible you should try to get a look at this chiller system because it is problematical to design a control system if the things you are trying to control are too ethereal :-)
Luck & Regards,
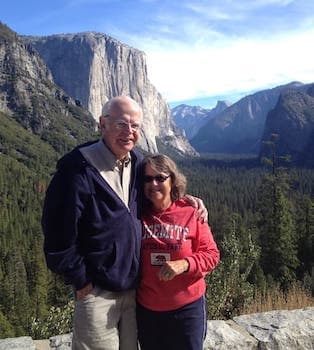
Ted Mooney, P.E. RET
Striving to live Aloha
finishing.com - Pine Beach, New Jersey
Q, A, or Comment on THIS thread -or- Start a NEW Thread