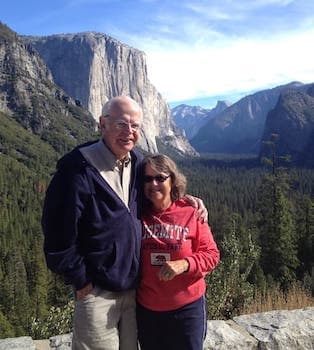
Curated with aloha by
Ted Mooney, P.E. RET
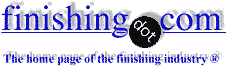
The authoritative public forum
for Metal Finishing 1989-2025
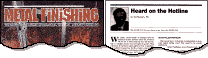
-----
Copper flashing under hard chrome plating - good idea?
Q. A chrome plating supplier has suggested that a thin copper layer can be plated onto 4130 steel prior to hard chrome plating without any effect on the adhesion of the hard chrome. Does anyone have any experience with this who could support or dispute this claim? Purpose of this experiment is to provide a visual indicator of when the hard chrome is worn through. Any comments on further questions to ask, or conditions to be aware of would also be appreciated.
Thanks!
consultant - Seven Valleys, Pennsylvania, USA
2004
A. I haven't heard of doing this, but I suppose it will reveal when the chrome is worn though, as advertised. Hard chrome can adhere well to copper as long as it's done right.
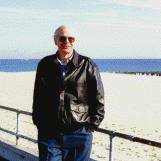
Ted Mooney, P.E.
Striving to live Aloha
finishing.com - Pine Beach, New Jersey
2004
A. If the substrate is hardened and the part is going to be subject to severe friction and sliding wear, the underlying copper lacks enough hardness to provide adequate support to the hard chrome. Scratch resistance will be reduced. For the mentioned purpose, I personally don't think it's a good idea. Alternatively, worn through chrome can be detected by swabbing the surface with a weak mixture of copper sulphate ⇦ this on eBay or Amazon [affil links] and sulfuric acid. Immersion copper deposit will proceed on areas where chrome has gone.
Guillermo MarrufoMonterrey, NL, Mexico
2004
A. Hello Amy Harmon Krtanjek, we want to point out that we have patented this process of wear indication under hard chrome platings.
Best regards,
Switzerland
2004
Hi Michael. Could you please give us the patent number so people can see what is and isn't covered? Thanks.
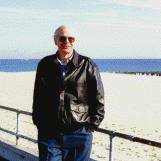
Ted Mooney, P.E.
Striving to live Aloha
finishing.com - Pine Beach, New Jersey
2004
A. In oil tool shafts we used both electroless nickel and copper under hard chrome. Both held good thru tests we rough cut hard chrome with grinding wheel to see if copper would hold up in between to harden surfaces and both held up as good as hard chrome directly 4340 HT. The reason for the test was that we needed a a coating between to stop the undermining of the hard chrome and of course copper was easier to activate than electroless nickel.
Chris Snyderplater - Charlotte, North Carolina
2004
Q, A, or Comment on THIS thread -or- Start a NEW Thread