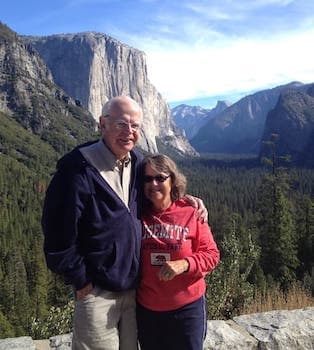
Curated with aloha by
Ted Mooney, P.E. RET
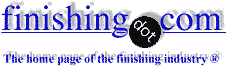
The authoritative public forum
for Metal Finishing 1989-2025
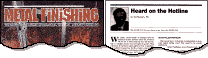
-----
What voltage is needed to copper plate
Q. I would like to set up a small plating tank at home. The object, firstly is to plate in copper and then nickel. My stumbling block is obtaining the correct amount of voltage at the right price. Could I use an arc welder for instance? What are the voltage requirements?
Glenn Hugheshobby - Melbourne, Victoria, Australia
2004
A. Others on this site can hopefully supply the 'typical' voltage/current needed. As for using a welder, low cost (AC) arc welders supply in the 30 to 80 volt range. If you're handy, you could buy a cheap one and remove some of the secondary winding to give a lower voltage. It's directly proportional, to halve the voltage, remove half of the secondary. For plating you need DC, which means you need a rectifier. You'll lose a couple volts in the rectifier, so take that into account when modifying. For availability, try a replacement rectifier for a DC welder. You might also need a fan to keep the rectifier cool. I suggest this route of AC welder plus a rectifier because DC welders have an extra inductor (coil) in them that you don't need, thus driving up the price. It comes down to the local market as to which approach is more cost effective.
Tom Gallant- Long Beach, California, USA
2004
A. Glenn,
Electroplating depends on amps rather than voltage. You just need volts to drive the current across the resistance of the tank. The amps you need depends upon the surface area and the type of plating solution. I expect you will use an acid copper sulphate
⇦ this on
eBay or
Amazon [affil links] rather than the cyanide process but this gives poor adhesion on steel or diecast parts. (you can minimise this by putting the parts into the tank 'live'. The other problem you will have is the need for some 'brightener'. These are proprietary chemicals. A little goes a long way so any friendly plating shop will probably give you a little. A welding unit could potentially run a very large copper tank. A small battery charger
⇦ this on
eBay or
Amazon [affil links]
would be more practical run at 6 v max. and some means of controlling and measuring the current would be useful. If you have limited control I would try about 2-3 v. A brown 'burned' deposit means probably too much current or no brightener. Give it a try & come back if you have problems. If you don't know how to handle acids then find out FIRST.
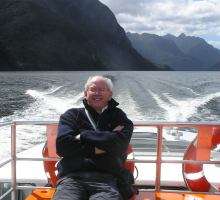
Geoff Smith
Hampshire, England
2004
Q. For copper plating in a tank that is 35 gallons of copper sulphate, what are my needs from the transformer regarding amps and voltage?
If I have the transformer at 8 volts, I think I still need a high level of amps because of the large amount of liquid. The item being plated is a 100 ft steel cable that has been cleaned and treated with a nickel strike. The anode is a large copper pipe.
I am an artist and working with electroplating as a gesture. I am not looking for a high quality perfect outcome, but rather I am more interested in the process of molecular exchange and transfer.
THANK YOU!!
- New York, New York, USA
April 23, 2018
A. Hi Phoebe. We have written a presentation on amperage, voltage and Faraday's Law which I think you will find quite understandable regarding your interest in the process of molecular exchange and transfer.
After you have read it, you will realize that you need to know the surface area of the steel cable and the thickness of copper you desire in order to figure out how many ampere-hours you will need, but the volume of solution is not involved in the calculation (although it can be important in some ways).
Since you are presumably not in a hurry, you can simply use the low voltage Geoff suggested and plate for a long enough time to get the required ampere-hours; I think 8 volts will prove too much and will result in burning. But please also recognize, if you don't yet, that you need DC to electroplate; AC will de-plate as fast as you plate :-)
Regards,
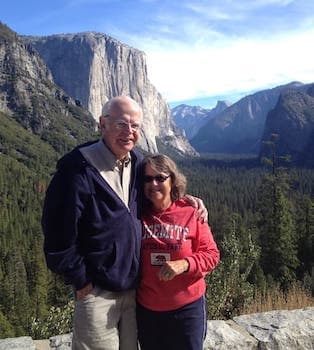
Ted Mooney, P.E. RET
Striving to live Aloha
finishing.com - Pine Beach, New Jersey
April 2018
A. Hi Phoebe
I agree with Ted, but have I spotted a problem?
Your question suggests that the cable is already nickel plated.
To get copper to adhere to nickel plating it must be done immediately (not in five minutes!). That is nickel plate - rinse - copper plate; and certainly not allowed to dry in between steps.
Any delay means that the nickel surface must be re-activated.
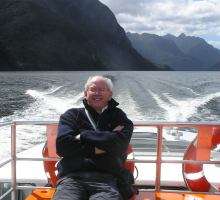
Geoff Smith
Hampshire, England
April 25, 2018
Q. Hi Geoff,
Yes I know about the immediacy of the nickel to rinse to copper ... that was what I did. Seems to be working now for the most part, except only on the cable closest to the copper anode ... other parts of the cable that are farther away in the tank are not plated at all. I presume it's because the molecules adhere themselves to the closest possible destination.
Thanks to everyone for your help.
Best, Phoebe
- New York, New York, USA
April 25, 2018
A. Yes, per Faraday's Law the thickness of the plating is directly proportional to the current flowing to that spot.
Regards,
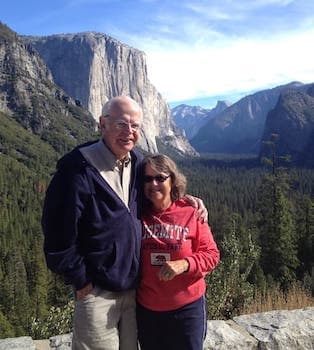
Ted Mooney, P.E. RET
Striving to live Aloha
finishing.com - Pine Beach, New Jersey
April 2018
Q, A, or Comment on THIS thread -or- Start a NEW Thread