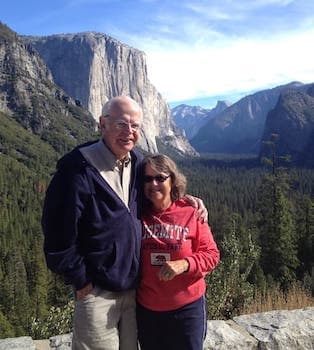
Curated with aloha by
Ted Mooney, P.E. RET
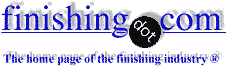
The authoritative public forum
for Metal Finishing 1989-2025
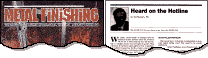
-----
Looking for way to reduce scrap in the anodize process
The parts are brought in from an outside vendor in the 7075-T6 condition, in lengths of 2.000, and with a .228 dia. hole drilled in the middle lengthwise. The parts are Solution Annealed, bent in a press to get a 1.969 radius, and then Artificially Aged. After the Aging process, they are machined. The last step in the process is to send them out to be anodized. When the parts come back they are pitted pretty badly on the inside, outside, and sides of the radius. The anodizer says 7075 is hard to anodize. He also says that the bending opens pores in the metal that make pitting easier. I think there is a problem with the acid etch they do before they anodize.
My question is this: Does bending to such a gradual radius cause pores to open in the metal? How can we fix the problem? Is there a less caustic of prepping the parts for anodize?
Manufacturing - Roy, Utah, USA
2004
Pits on the inside could be attributed to lack of agitation and fresh solution and current on the inside of the tube. Pits on the outside are unforgivable. Get another anodize shop. 7075 is not quite that difficult. The anodic coating forms on a 90 degree perpendicular plane from the base metal. A sharp bend will show a void where the crystalline columns are spread on an outside diameter. Conversely the perpendicular columns will crash into each other on an inside curve. This is usually not a problem with Type II "soft coat" but it is a big problem with thick hard coat. The Mil spec suggests some radius recommendations for some thickness relationships. Again, try another shop.
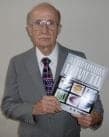
Robert H Probert
Robert H Probert Technical Services

Garner, North Carolina
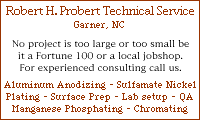
2004
Q, A, or Comment on THIS thread -or- Start a NEW Thread