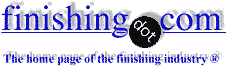
-----
Sulfuric Anodize Wear Characteristics
Hello,
We are about to release a product that has been split into a light duty and a heavy duty version. The light duty version uses anodize per MIL-A-8625 / MIL-PRF-8625
[⇦ this spec on DLA]F, type II, class 1, .0002-.0005 thick while the heavy duty version uses a hard anodize, type III, class 1, .0004-.0006 with nickel acetate seal. There was the tight spec on the hard anodize thickness to allow the use of the same machined part and achieve appropriate wear characteristics. However our anodizers have not been able to hold the required tolerance on the hard anodized version at a reasonable cost and this has cause some wear and dimensional fit problems. Masking has been considered however because of the pricing structure for this product the additional cost per piece is unacceptable. The part is
6061-T6 and rather complex with internal radiuses, grooves, tight tolerance dowel holes and threads. We were considering increasing the thickness range for both the type II and III however there were some concerns about harming the wear characteristics of the sulfuric anodize part by allowing a thicker anodize. The parts are used as a bearing surface. Is there any merit to these concerns? The final solution will probably be 2 different parts but I want to look into every option.
Thanks for the input,
actuator mfg - Ft Wayne, Indiana, USA
2004
I would also take a look at using electroless nickel. It may be more cost effective and you would only have one part number.
James Watts- Navarre, Florida
2004
Q, A, or Comment on THIS thread -or- Start a NEW Thread