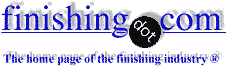
-----
Coating inside of stainless tubes
Hi,
I am looking for methods coating the inside of a stainless tubing
(0.132" ID) with a 5 micron layer of copper at the minimum. 10 microns max actually. The intended purpose is to replace a copper braid that is typically placed on a insulation layer in the tubing. Are there recommended processes for achieving this?
Thanks.
Oil Gas - Houston, Texas
2004
2004
Hi there,
Well V, You do not say the length of the tube. However, If it is more than .5" I would recommend Plating the OD of a copper tube over trying to plate the ID of this Dia. SS tube.
Hope this helps,
Job Shop Plater - San Diego
I have a similar, but more difficult problem. I am trying to coat the inside of a long aluminum microtube (100 feet) with a thin layer of niobium or other refractory metal. one manufacturer, after much consideration, suggested to me that a multilayer strip of metal so formed could be made into a tube. However, it seems to me this would create a seam that could prove problematic. Electroplating from the inside with aqueous solutions would work with some metals. but this can not be done with refractory metals. molten niobium salts could be used for electroplating but for the pesky problem of the melting point of the salts being well in excess of the melting point of aluminum. As for copper onto steel, I am uncertain. but if electroplating can be done with ordinary steel plates, then it should be possible to do the same to the inside of a steel pipe.
The inside of a tube could be coated with some sort of sticky material. Then powder made of the coating metal could be blown through the tubing. the metal powder would deposit in the sticky material against the inner wall of the tube. An electrode could be slowly pushed through the tube to be coated. The tip of the catheter/electrode could be made so that the tip is always held in the middle of the tube. An electric potential could be created between the tip of the catheter and the tube that is to be coated. Electric arcs between the catheter and the tube would arc weld the particles to the inner wall of the tube. Multiple passes could create thicker coatings as needed. The catheter would not disrupt the delicate powder layer as it would only rub against the region of the tube that already has bonded metal powder -- the unbonded region remains untouched. If the tube to be coated is so long that the catheter starts buckling when pushed, then a magnet outside the tube could pull the catheter instead. The sticky material would ideally be made of something that tolerates the heat without causing problems. The tube would probably need be filled with an inert gas or be evacuated before arc welding.
An alternative method of holding the metal powder against the inside of the metal tube would be to create a vortex by appropriately angled sideports near the tip of a catheter blowing inert gas, the axis of the vortex parallel to the axis of the tube to be coated. The powder particles would be tightly held against the wall by centrifugal force. An electric arc introduced by the same catheter then could weld the particles to the inside of the wall.
Alternatively, a special hollow catheter could be fabricated to do the job. The metal to be deposited could be fed to the tip by feeding wire made of the metal through the catheter. At the tip, an electric arc could vaporize the metal. The tube to be coated and the source of metal vapor could be electrostatically charged so that an electric field would accelerate the coating metal from the tip of the catheter onto the inner wall of the tube to be coated. The catheter could be slowly pulled through the tube to be coated at a controlled rate. Multiple passes of the catheter could create any desired thickness of coating. The catheter would have to be electrically insulated, perhaps by anodization, and the tube to be coated would have to be evacuated. A multitude of techniques are nice in theory, not simple in practice. Custom fabrication of such tubing is a painful prospect that I do not cherish. I wish someone just sold these exotic coated tubes. If anyone knows of such a supplier of refractory metal coatings inside aluminum tubing, please let me know.
research/development - New York, New York, USA
2005
Q, A, or Comment on THIS thread -or- Start a NEW Thread