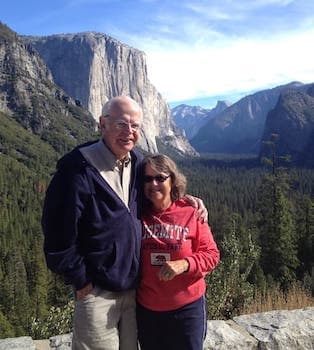
Curated with aloha by
Ted Mooney, P.E. RET
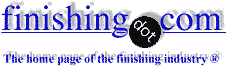
The authoritative public forum
for Metal Finishing 1989-2025
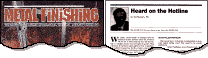
-----
Black coating for 1018 steel that will not scratch
Q. My company makes automobile headrests. We have purchased black electrocoated armatures, but have already noticed scratch marks. The headrests will move up and down and we need to research another type coating. Which coating application is best used on 1018 steel?
Thanks,
industrialist - Milan, Tennessee, USA
2004
A. I would suggest that you consider salt bath nitriding such as is offered by Kolene.
My understanding is that if the finish is not quite black enough for you, you can do a black oxide on top of it which, if it scratches, would only reveal the non contrasting dark gray color of the underlying nitriding. As I understand it, this is the approach used on handguns by one of the world's most respected makers.
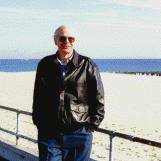
Ted Mooney, P.E.
Striving to live Aloha
finishing.com - Pine Beach, New Jersey
2004
A. I agree with Ted's suggestion of the Kolene ferritic nitrocarburizing process. It provides excellent wear and corrosion resistance, and the color is often quite dark, especially when processed through Kolene's QPQ process.
Toby PadfieldAutomotive module supplier - Michigan
2004
Q. I am confused that whether the QPQ process for low carbon steel after salt bath nitrocarburizing(tufftride) is same as black oxidizing? Will black oxidizing affect the nitro-carburized layer in any way?
Murali M H- Bangalore, Karnataka, India
February 28, 2013
A. Hi Murali. The QPQ process is salt bath nitriding and does case hardening. Black oxide is a superthin black coloration and does not impart wear resistance.
I think Toby probably put it better than I did, that black coloring is part of the QPQ process rather than a post treatment after it. As you see, we appended your inquiry to an earlier thread which includes a link explaining the QPQ process. Good luck.
Regards,
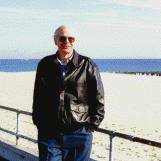
Ted Mooney, P.E.
Striving to live Aloha
finishing.com - Pine Beach, New Jersey
February 28, 2013
Thanks for your reply Ted!!
My confusion arose from the fact that we are right now carrying out Salt bath nitrocarburising, then black oxidising and then polishing. The metal surface is starting to erode in service as if there is no hardened layer. And I am unable to point my finger where the process is going wrong, during nitrocarburising or black oxidising. We are carrying out lapping (polishing) at the end because we are unsure of the thermal distortion that may occur.
- Bangalore, Karnataka, India
March 10, 2013
Is zinc phosphate an alternative to QPQ
Q. My question & my situation:
Good day everyone, my question: is zinc phosphate a good alternative for QPQ if there is no availability to perform this process? And if yes, is it the best alternative or there are other better options?
Thanks
- Helwan, Eqypt
May 28, 2018
A. Hi Ahmed. QPQ is a reasonably attractive, surface hardening, corrosion-proofing process. Zinc phosphate is none of those three. If it doesn't actually have to be black, hard chrome plating might be best, and QPQ is often promoted as an alternative to hard chrome. If it's a cylinder rod, that might be your only reasonable alternative. But black chrome plating might be the closest alternative depending on how you look at it.
Other alternatives really depend on what the item is, and the service condition. Black oxide & oil is used on firearms but is nowhere near the equal of QPQ in wear resistance or corrosion resistance. Gas nitriding or plasma nitriding might function while not being aesthetic enough for you. Good luck!
Regards,
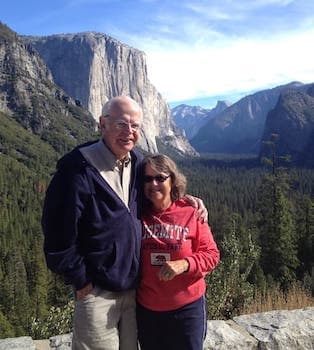
Ted Mooney, P.E. RET
Striving to live Aloha
finishing.com - Pine Beach, New Jersey
May 2018
Q, A, or Comment on THIS thread -or- Start a NEW Thread