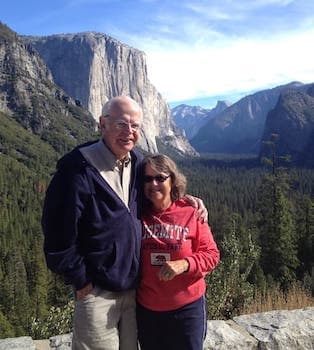
Curated with aloha by
Ted Mooney, P.E. RET
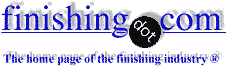
The authoritative public forum
for Metal Finishing 1989-2025
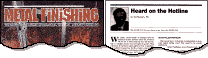
-----
Hydrogen Embrittlement - C1117
2004
Hello all,
I am working on a 1/2" diameter shaft made from cold-drawn C1117. After machining it is case hardened .005-.010" deep (Carbeurized to Rc 60-62). It is then plated in a Zinc acid chloride bath. Due to some unexplained breaking under no load (at a cross-drilled hole) we have added a baking operation of 4+ hours at 400 degrees F within 2 hours of plating. As you can guess, we think our problem is hydrogen embrittlement. All of our material is to specifications, as is the case hardening. Another thing that is interesting is we have made this part (supposedly unchanged) for 18 years and only recently have we had this problem.
Questions:
1) Is this problem likely to be Hydrogen Embrittlement or should I be looking at other causes?
2) If it is Hydrogen embrittlement, what variables should I be looking at in our process that could have changed recently? (acid bath variables, plating bath variables, etc...)
3) Also, on our first baking try, there was no plating left on the parts (dull grey finish) and I'm pretty sure out temps could not have been over 425 F. Is this too hot?
Thanks in advance for the advice and let me know if you have any questions.
Manufacturing - Hastings, Nebraska, United States
Hydrogen embrittlement certainly is one item to consider. Another may be quench cracking. The acid concentration and inhibitor concentration of the plating bath are two parameters to investigate. 425 °F is ~ 220 °C which the upper end of the recommendation in ASTM B850-98. The chromate coating undergoes a change from an amorphous structure to a crystalline structure above ~ 65 °C, which may account for the appearance change. It sounds like you should have a professional failure analysis performed to ascertain the root cause.
Toby PadfieldAutomotive module supplier - Michigan
2004
Tom,
An acid bath embrittles the least of all systems. If this is a new problem audit the pickle. Please use a inhibitor at the pickling stage. Don't passivate after plating. Just rinse and Nitric dip, Rinse, Dry. Please bake for 3 hours at 200 °C. Then Passivate as follows. Cool to ambient in air. No water quench. Activate in 1 percent nitric acid. Passivate as usual. Process as before. This will help.
Regards,
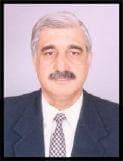
Asif Nurie [deceased]
- New Delhi, India
With deep regret we sadly advise that Asif passed away on Jan 24, 2016
2004
Q, A, or Comment on THIS thread -or- Start a NEW Thread