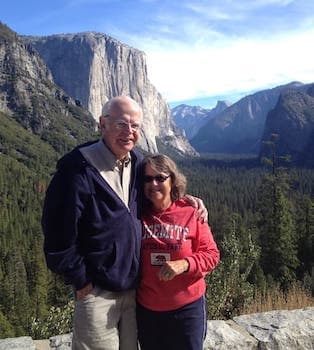
Curated with aloha by
Ted Mooney, P.E. RET
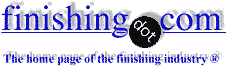
The authoritative public forum
for Metal Finishing 1989-2025
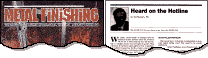
-----
Severe pitting on stainless steel
Q. We have been electropolishing for the past 16 months with excellent results until 2 months ago. Due to evaporation and work of the tank we as were advised by our suppliers to top the tank up with 100 liters of electropolish solution and 25 liters of concentrate. Since then our problem has started. We are experiencing severe pitting on the surface which is so deep we are having to scrap the jobs. This was not on every job but 1 in 29 or 1 in 63 (no sequence) now its on everything we put in the tank (all grades of steel). We noticed when we added this solution it was very dense and floated and stuck like glue to the components. Was told to add large amounts of water, did this, still bad pitting. We have been told then its a current fault, had 3 electricians in have done all the tests and there's nothing wrong with the current/ then told degreaser we checked and bought new only used this so no chance of contamination - still didn't work
We are 6 weeks down the line now looking like we will loose all out customers as we cannot chance putting anything in the tank
Could you please help us with our problem and maybe shed some light on it
We have sent the solution to be analysed by lab on 3 occasions - they actually have told us they only tested on lot and that was OK but only test for density. since then we have sent another sample and its been analysed as having large quantities of zinc in it. Could this be our problem. 16/04/04 Would Zinc have this severe corroding effect on steel?
The other coincidence is that we moved premises beginning Jan and share a large factory with a Powder Coating firm - could this have anything to do with it
Update on message: Chemist has now told us today 19th April he made a mistake on Friday's analysis reading and its not 20% zinc showing in the tank but 2% but ions are there.
electropolisher - NAPIER, NEW ZEALAND
2004
A. As you are using a proprietary solution, your vendor should furnish the primary assistance.
One problem is lack of sufficient agitation. It is of crucial importance to thoroughly mix the solution prior to sampling for analysis and after making additions. Can you give complete solution analysis, including SG (specific gravity @ 20 C)? I suggest keeping an unused stock solution in the laboratory for comparison. What are the limits given by the vendor? Is this a phosphoric + sulfuric acid solution? Any surfactant or other means of handling oils released from parts? Operating temperature? Does your tank have a liner such as polypropylene to prevent shorts and stray currents? What are the tank, cathode and electrical workbar materials?
I doubt whether anyone has ever heard of zinc in an electropolishing solution for stainless steel, so perhaps no definite answer as to whether it causes pitting. Can you identify the Zn source?
Likely causes for pitting are improper water content or improper current density. Test the effect of current density by running a large part or rack of small parts at a 45 degree angle vs. the cathodes (rather than parallel or equidistant). Watch for the intensity of bubble formation as a function of geometry during the testing (and in normal operation), then observe the test part(s). Adjust cathode-to-anode (parts) spacing accordingly.
- Goleta, California

Rest in peace, Ken. Thank you for your hard work which the finishing world, and we at finishing.com, continue to benefit from.
2004
Q. We have been seeing some issues with pits showing up after electropolishing.
These are weldments made from 316SS - when we see pitting we see these pits all over the entire weldment. Since these are components that are welded together we are completely confident that the problem isn't because of material imperfections as these are sheet metal components supplied from different fabricators (who would have purchased from different sheet metal mills).
The interesting thing we are seeing is that not all weldments show pits. The ones that show pitting generally look brighter in appearance than one that doesn't show pitting. I don't know if that has anything to do with it but the ones with pitting are definitely brighter. These pits look to be generally the same shape. When magnified they look almost like a run(for lack of better words).
Can you please explain in technical detail what are the reasons we could see pitting after electropolish?
These are close-ups of different areas showing these pits. Please note the pictures are being taken of different parts of the weldment, so the sheet metal used would have come from different mills. Any help would be greatly appreciated.
- Marion, Iowa
April 24, 2013
A. Trisha,
It's too bad you're seeing this pitting. Based on the evidence you presented, I tend to think that when the parts are being electropolished one or two things is going wrong. The setting could be too high and the parts could be damaged in such a case. Try using a lower setting and also watch placement and load. One can't run too many parts at the same time and then crank it up to full power and expect good results. Another thing you mentioned is that the pitting occurs on the shiny parts. Well, if we assume that the setting is too low, we won't expect to see shiny parts. If the setting is correct or too high we would expect to see shiny parts. If the setting is correct we might not notice that they are shiny, we would just think they look normal, like all the other parts because the setting is correct after all. So, this tells me that the setting is too high and that made the parts appear shiny. Just some ideas. We've seen this type of thing happen a lot but I suppose it could be another cause.
Another idea could be if the parts were left in too long and the rest of the settings were correct. Do you know if the parts run on timers and the power turns off automatically or is it the case where the employee is supposed to turn off the power and take the parts out at a given time? Is it known whether or not the employee had a circumstance which makes it so that so parts can be processed for longer times? It's just something else to investigate. I would recommend a 5-why and Process Map. I'd be happy to help. Good luck.
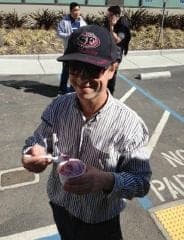
Blake Kneedler
Feather Hollow Eng. - Stockton, California
July 12, 2013
Q, A, or Comment on THIS thread -or- Start a NEW Thread