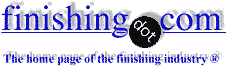
-----
High speed electroforming
We like to find out if somebody already developed a Ni or NiCo electroforming batch that is capable of operation near zero stress levels at 800-1000 A/sf with a minimum use of organic additives and can be used to manufacture optical quality reflectors with reusable chrome plated steel mandrel. If possible we like to operate a tank at 15 A/gallon in combination with a chiller and a strong sparger system.
Karlheinz Stroblplating process research - Bohemia, New York
2004
I am not aware of any commercially available nickel bath that will deposit at 15-20 microns a minute. This is extremely fast deposition and will require, amongst other things, excellent solution maintenance. The rates you are seeking are more akin to "jet plating" and this technology, whilst well worked, has limitations in achievable thicknesses. To get low stress, you will have to use a sulphamate bath and since most organic additives will have almost no effect, any desired properties will have to be inparted by inorganic additives, such as the cobalt you mention. To accommodate this sort of ccd, I would expect you will need a cathode surface electrolyte velocity of approaching 10 m/sec which in itself will create numerous technical problems. Out of interest, why do you want such high deposition rates?
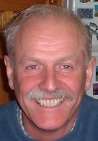
Trevor Crichton
R&D practical scientist
Chesham, Bucks, UK
2004
Out of curiosity, what is jet plating and where can I read about it?
Karlheinz Stroblelectroforming and thin film coating - Bohemia, New York
2004
For your curiosity, we are evaluating the feasibility of electroforming a very high volume consumer part at much lower costs then currently possible.
Karlheinz Stroblelectroforming and thin film coating - Bohemia, New York
2004
"Jet plating" may also known as "high speed metal deposition" and was developed (I believe) by NASA in the 1970's, so that should be a good source of information. The technique is basically to discharge a very high velocity jet of electrolyte at the workpiece whilst passing an electric current through the jetstream. The jetstream must have lamellar flow or the current path will be disrupted. The idea is that the jet velocity will all but eliminate the Helmholz double layer and allow almost instantaneous transfer of metal ions to the workpiece without having the bipolarity of the double layer to limit the electrochemistry. This allows very high current densities and it is possible to deposit at rates of 0.5 um/second (i.e., about 1,500 ASF) for nickel. The techniques does work, but it has severe limitations in the thickness of your deposit. You obviously have to take extreme care of your electrolyte and filtration system. Obviously most organic additives that rely on surface adsorption and/or modifying the HDL do not work with this technique.
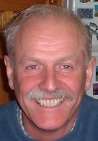
Trevor Crichton
R&D practical scientist
Chesham, Bucks, UK
2004
Mr. Strobl,
I think you may also want to find more about brush (selective) plating, as it has some similarities to jet plating. Extremely fast deposition (+0.001" per minute) and very low stress levels when operated per mfr. instructions. Only problem, too expensive for high production applications.
Monterrey, NL, Mexico
2004
I would personally not recommend electroforming for a high speed process because, as with all metal deposition, it is governed by Faraday's and Ohms Laws. This means that metal is only deposited by the passage of electricity and that the current will find its shortest route. Consequently, it does not lend itself to rapid metal deposition. Any flaw on either the mandrel or the electroform surface will result in preferential deposition and an uncontrolled process. Successful electroforming should be done carefully and precisely, not as fast as it possibly can.
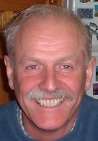
Trevor Crichton
R&D practical scientist
Chesham, Bucks, UK
2004
2004
Maybe my response here will give you more hope than technical advise. We routinely electroform optical parts at 150 ASF (occasionally 200 asf) with stress levels of 0 ± 100 psi. We have also plated parts under 3500 psi at 500 ASF using a high metal content sulfamate nickel and massive solution flow. In both cases a minimum of organics were used. We accomplished these goals through hard work and ingenuity, those things that make America Great.
As far as the technical end goes, what you seek is definitely not "off the shelf" but you can start with a High Speed Nickel formulation offered by Macdermid. Also as I mentioned a high but uniform solution flow in your tank is a big factor here.
Lastly, the use of Steel / Chrome mandrels is not the best choice, both metals easily contaminate the bath and create havoc with the deposits internal stress, even in the ppm range, at high current densities. I believe what you are trying to achieve is possible, the question is Do You?
electroformer - Corona, California
Q, A, or Comment on THIS thread -or- Start a NEW Thread