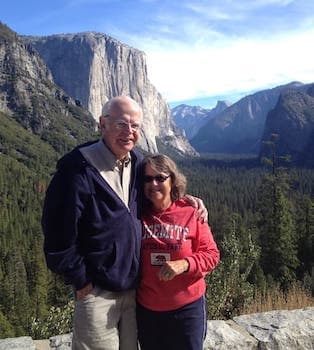
Curated with aloha by
Ted Mooney, P.E. RET
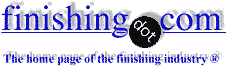
The authoritative public forum
for Metal Finishing 1989-2025
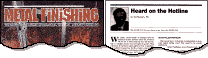
-----
17-4PH Passivation Problems
Q. We have an assembly that has 304SS and 17-4PH laser welded together. We are required to passivate after the welding of the components.
If I run the entire assembly thru ASTM A967 nitric 2, could the 17-4PH harm my nitric bath?, and is there any chance of getting an effective passivation of the 17-4 end of the part with this process?
Medical Component Mfg. - Brooklyn Park, Minnesota, USA
2004
A. Chris,
citric acid passivation, also in ASTM A967, can be used without fear of adverse reactions from having both 303 and 17-4 SS.
adv.
Let us know if we can help you.
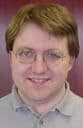
Ray Kremer
Stellar Solutions, Inc.

McHenry, Illinois
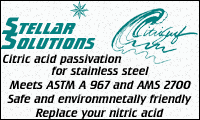
2004
Q. WE ARE EXPERIENCING SEVERE PROBLEMS WITH PASSIVATING 17-4PH INVESTMENT [LOST WAX] CASTINGS. WE CURRENTLY PREWASH OUR FINISHED CASTINGS WITH A HIGH ALKALINE CLEANER, THEN PASSIVATE WITH A citric acid BASED PRODUCT AT 85 °C. THE RESULTS ACHIEVED ARE VERY POOR, RUST SPOTS APPEAR DURING DRYING AND STAINS OCCUR ALL OVER THE PARTS. THE PRODUCT WE ARE USING IS SUPPOSED TO BE SUPERIOR TO THE NITRIC ACID PASSIVATING UNDERTAKEN PREVIOUSLY [QQ-P-35C (canceled) [link is to free spec at Defense Logistics Agency, dla.mil]] UNFORTUNATELY WE HAVE NOT SEEN THE BENEFITS TO DATE. CAN ANYONE PROPOSE A SOLUTION, OR HAS ANY MEMBER EXPERIENCED THE SAME PROBLEMS?
TONY BUCKLANDINVESTMENT FOUNDRY MANAGER - ILFRACOMBE, DEVON, ENGLAND
2004
A. Tony,
Passivation of stainless steel requires the removal of free iron from the surface and then the generation of the oxide film that gives the stainless its rust resistant properties. I would check for the following.
1) The surface presented to the passivation chemical is clean enough for the chemistry to wet out and react with the steel.A poorly degreased surface may prevent a proper reaction. There are available passivation chemicals that can clean as well as passivate.
2) The passivation chemical has done its job. citric acid based materials may not penetrate as well as Nitric based systems.
3) Rinsing after each stage is thorough. Any highly alkaline chemical left on the surface will neutralise the citric acid and any acid left in the pores of the metal could promote corrosion sites. Poor rinsing is a common cause of surface staining.
- Birmingham, England
2004
A. Hi, Tony:
Investment castings of 17-4PH are not easy to get passivated correctly with either nitric or citric formulations, but a process can be developed to do it well. We have had great success with most customers with the citric formulations -- producing excellent passive parts. Sometimes it is a matter of good cleaning first, as John says.
The citric passivation actually goes DEEPER than the nitric, as born out by University studies, and there is no problem with residual citric left in pores due to poor rinsing (like there is with nitric). There are new formulations in development with citric that should do a better job on this kind of application.
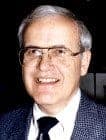

Lee Kremer
Stellar Solutions, Inc.

McHenry, Illinois
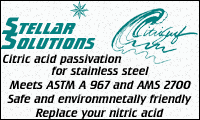
2004
adv.
Great success today with new formula using citric acid on 17-4PH investment castings. Still working on exact process, but this should be an answer to your problem. Excellent corrosion resistance and no staining.
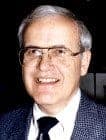

Lee Kremer
Stellar Solutions, Inc.

McHenry, Illinois
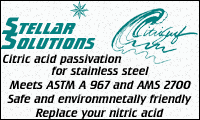
2004
Laser marking issues with 17-4PH and passivation
Q. When passivating 17-4ph (citric bath 10 minutes) sometimes the laser marking comes off and when copper sulphate ⇦ this on eBay or Amazon [affil links] is added it bleeds pink an indiction of Fe on the surface of the laser marking ONLY the rest of the part shines. What is causing the iron to come to the surface is it improper laser marking or passivation?. The laser marking looks good until passivation then it all falls.
Daniel J.MarcotteMedical industry, employee - Portsmouth, New Hampshire ,USA
2006
A. The reason that whole surface is not bleeding pink is because that this surface is covered by oxide film. If you hold passivation liquid longer on the surface, the whole area will bleed pink.
Passivation with proper liquid will save the laser marking and protect the surface without discoloring.
adv.
Contact us for help.
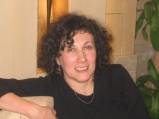
Anna Berkovich
Russamer Lab

Pittsburgh, Pennsylvania
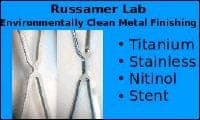
2006
A. Technically, laser marking is heat treat scale which should be completely removed for proper passivation.
But, see letter 41849 and links therein for ideas on laser marking.
- Goleta, California

Rest in peace, Ken. Thank you for your hard work which the finishing world, and we at finishing.com, continue to benefit from.
Q. My name is Oleg and I am a Quality Assurance Manager
I have the same problem with my customer.
Can you please explain what is the reason for it to happen and how to avoid it in the future, meaning for me to provide and implement corrective action.
Maybe I need to instruct my S.C to perform passivation differently?
Thanks
- Haifa,Israel
March 31, 2014
A. Hi Oleg,
We have developed our own passivation solution for martensitic stainless steel. It is not based on Nitric or citric acid s.
adv.
The solution (and gels) were successfully implemented at Bama Technologies in Italy. Contact me for more information.
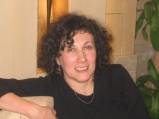
Anna Berkovich
Russamer Lab

Pittsburgh, Pennsylvania
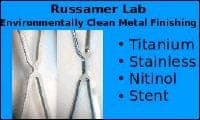
April 1, 2014
A. Oleg,
Much of the problems and failings of passivating castings result from the very bad surfaces that some castings have. The greater the roughness and porosity, the harder it is to get good results. Treatments such as sandblasting, electropolishing, and vacuum impregnation can help.
I could try to hazard a guess at what you can do to improve things if you describe your current process.
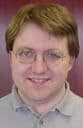
Ray Kremer
Stellar Solutions, Inc.

McHenry, Illinois
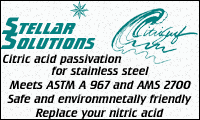
April 2, 2014
Q. Hi
We passivate 17-4ph investment castings with a Stellar Solutions [a finishing.com supporting advertiser] fluid. We experience dark grey/black mottling. We are considering switching to a pickle followed by passivating.
Will pickling resolve the mottling?
- Ilfracombe,Devon,UK
October 8, 2016
Tony,
I would ask which product of ours you are using, perhaps you should contact me directly.
It's somewhat likely that the issue is a result of it being a casting in the first place, the surface of a casting is generally not very consistent or friendly. Are you doing any surface prep work like bead blasting?
I would go ahead and test a few parts in a pickle-then-passivate process to see if it helps any, before making any decisions about whether that's the direction you want to go.
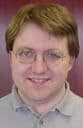
Ray Kremer
Stellar Solutions, Inc.

McHenry, Illinois
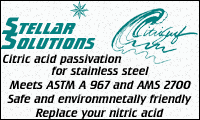
October 25, 2016
Q. I am currently working on a project where we are passivating 17-4 stainless. I have issues with passivation or my copper sulphate test removing laser marking. We are trying a new process with Citric spot passivation just on the laser etched space. It seems to survive the passivation but then during a copper sulphate test it completely plates with copper and then all easily wipes off. Any suggestions on passivation of this grade stainless and getting laser etching to stay. Also maybe copper sulphate test is not appropriate in this case.
Patrick FoleyEngineer - Houston, Pennsylvania, US
October 17, 2016
I can recommend local electropolishing - only at the area of laser mark. It will remove all alloy alternations that are caused by laser heat.
adv.
Contact me for more information.
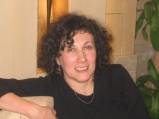
Anna Berkovich
Russamer Lab

Pittsburgh, Pennsylvania
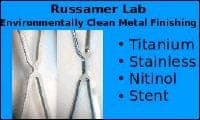
October 17, 2016
A. Patrick,
Laser marks are tricky regardless of the grade. It usually takes some experimentation to nail down the best laser settings and passivation process.
(adv. Please contact me if you would like some tips on that.)
I only rarely see a laser mark that can pass the copper sulphate test. Clearly there is a lot of iron in laser mark, which is also why the passivation acid ruins it when you leave it in too long. I typically skip copper sulphate on laser marks and use a water immersion test instead (usually the boiling version).
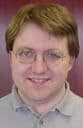
Ray Kremer
Stellar Solutions, Inc.

McHenry, Illinois
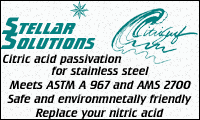
October 25, 2016
Q, A, or Comment on THIS thread -or- Start a NEW Thread