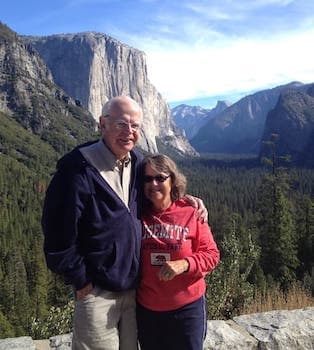
Curated with aloha by
Ted Mooney, P.E. RET
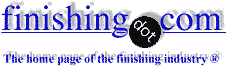
The authoritative public forum
for Metal Finishing 1989-2025
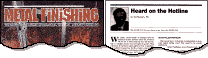
-----
Gold-Plating Iron and the Electromotive Chart
2004
Q. Hi,
I am the chemist/electroplater at the National Radio Astronomy Observatory in Charlottesville, Virginia. At times I get requests from electrical engineers that call for unusual, and normally not chosen, procedures.
One of these of late is the gold-plating of pure iron - 99.5% iron that has a smooth-machined finish which is to be used in vacuum for cores of electromagnets for supercooled situations.
Generally, I just plate the metal I am requested to plate. It was a rush-job for gold plating (cyanide gold in a phosphate-citrate stock - commercial) on iron cylinders and other parts. The gold thickness we used was about a hundred microinches.
Later, longevity of the pieces was called into question. Would these parts last ten to twenty years? Not so much the parts protected in vacuum, but those kept as spares that were not to be stored in any special environment, such as moisture-free, oxygen-free jars?
The thought discussed was the difference in the positions of gold and iron in the electromotive chart. Should not nickel be used instead? The cylinders had two small threaded holes, and would not any screws inserted into them get locked in place due to corrosion. Was there no border between the iron and the gold that contained moisture that would cause anodic-cathodic breakdown and corrosion?
The pieces, naturally, passed the "scotch-tape-test" after initial plating. The filtration used, if relevant, was submicron filtration (we had begun this when doing plating for NASA to meet air qualification).
by Reid & Goldie
-- hard to find & expensive; if you see a copy cheap, act fast!
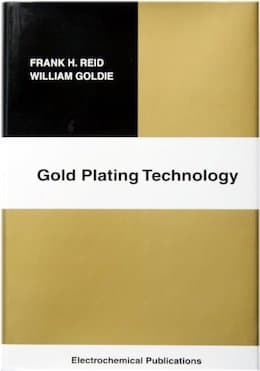
on eBay or
AbeBooks
or Amazon
(affil links)
Please answer, if possible, the concerns I list above, and these additional questions:
1. Is the electromotive difference between gold and iron OK for some applications, e.g. the more commercial and short-term ones, while not for others requiring long- term integrity?
2. Is there a layer of moisture appearing between the iron and the gold at all?
3. If you would use electroless nickel instead of gold, what particular formulation would you choose for... a. durability b. uniformity I can do small batches, as this is not a production facility per se.
4. Why does cyanide gold adhere initially without a problem from immersion plating?
Thanks very much. I know this is an extensive letter, but is of great importance to my colleagues, as it involves an international project with a number of countries...
Vincent E. SummersMicrowave Electronics: Educational - Charlottesville, Virginia, USA
Q. I wanted to ask whether we could plate gold with iron? If not, why not?
Arpit Nagpal- Delhi, India
October 23, 2013
A. Hello,
I would assume the second inquiry was asking about plating of gold directly on iron. It can be done but is not desirable for any application that I know of. Without proper pre - plating measures such as a Cu strike, Cu and Ni barrier plate, you will experience migration of the iron through the gold layer, which in turn would ruin any good characteristics that gold offers. This would be like putting a mink coat on a pauper. Some of these good characteristics are low contact resistance, excellent solderability, corrosion resistance, good electrical conductivity, etc. Iron is not used even as a hardening agent (alloy) in gold plating solutions because of its poor corrosion resistance, and low electrical conductivity value. Nickel, cobalt and silver are common alloying agents for electronic applications. Copper is sometimes used as an alloy to achieve a certain color in decorative gold plating applications.
Process Engineer - Mesa, Arizona, USA
October 23, 2013
Q, A, or Comment on THIS thread -or- Start a NEW Thread