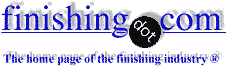
-----
Anodizing thickness
2004
I have been attempting to understand how when I specify 0.001" of hard anodizing my job shops are telling me that half of the coating will penetrate the substrate surface and 1/2 will end up as coating on the surface. This seems to be the normal response after questioning 5 different sources. It also does not seem to matter if it is type II class 2 or class 3. Would I be correct in assuming that this mysterious diffusion depth is actually the amount of material removed in the cleaning and etching steps?
Currently I must specify 0.002" coating thickness if I am to receive my parts back with 0.001" of coating thickness above the substrate. Is this normal for the anodizing industry?
Thank you,
Michael ZurawR&D - Bolton, Ont, Canada
2004
Yes, that's the story, Mr. Zuraw, although depending on the alloy and the type of anodizing, it can vary a little. Most of the missing .001" of aluminum is not in the etching and cleaning tanks though, it's in the .002" aluminum oxide anodized coating. Anodizing is not a deposition process like electroplating, it's a conversion process where aluminum is oxidized to aluminum oxide, and in order to create the aluminum oxide, you consume aluminum.
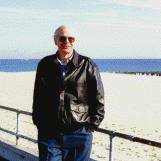
Ted Mooney, P.E.
Striving to live Aloha
finishing.com - Pine Beach, New Jersey
2004
Michael
The easiest way to explain this result it that the oxide (anodizing) is made from the base metal, not put down on top of the base like plating from the bath make up or painting like brushing material on. Therefore you dissolve 1x metal (aluminum) to make up 2x oxide. Or if you could form on 1 inch of oxide you would use 1/2 inch of the base aluminum to form it. Hope this helps.
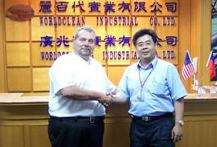
Drew Nosti, CEF
Anodize USA

Ladson, South Carolina
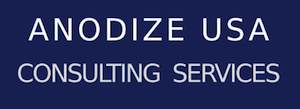
Q, A, or Comment on THIS thread -or- Start a NEW Thread