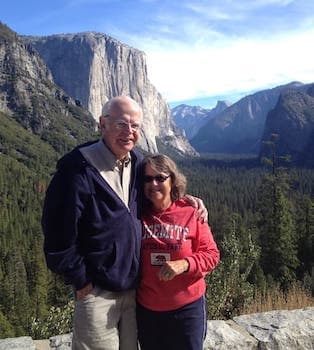
Curated with aloha by
Ted Mooney, P.E. RET
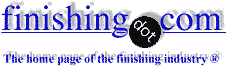
The authoritative public forum
for Metal Finishing 1989-2025
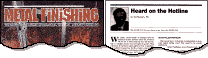
-----
Conductive Aluminum Plating
My company makes high end digital music servers. We currently have a steel chassis (CRS .048 Zinc Clearcoat). For our next generation of products we are interested in using an aluminum chassis. Because we make electronic devices we must contain the radiation. Currently we mask off the paint on the cover (CRS .040 powdercoat) so that there is electrical conductivity to the chassis. With aluminum I am concerned about oxidation over time. My only experience with oxidation prevention with aluminum is with anodization. However anodizing is not conductive. What is the best plating for aluminum that is conductive and will resist oxidation? Or do I even need to plate it? Am I being overly concerned about it oxidizing?
Fritz Koenigelectronics mfgr. - Ballston Spa, New York
2004
2004
You are looking for chromate conversion coating of aluminum, Fritz. You want to get a copy of MIL-C-5541 which explains the process, and look into Type 3 chromating.
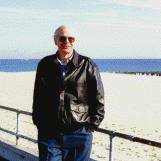
Ted Mooney, P.E.
Striving to live Aloha
finishing.com - Pine Beach, New Jersey
We can evaluate our alternate silica based (zero chrome) coating to meet your requirements. Please contact us.
Ravi Chandran, Ph.DNew Brunswick, New Jersey
2004
If the conductivity needed is for contact is grounding you could mask those areas and anodize the balance.
Chris Snyderplater - Charlotte, North Carolina
2004
Most of aluminum chassis are plated by silver. It is solderable and conductive comparing to bare aluminum or anodized one. Heat sink are plated by silver . contacting area also can be selective plated by silver.
Hadi Khosraviplating and anodizing - Tehran, Iran
2004
Ed. note: We had an older thread on a similar subject, which we've now merged into this one in lieu of maintaining separately . . .
![]() |
This also needs to withstand changes in temperature and humidity. Enclosure will be in contact with tin on printed circuit board. Electroless Nickel has been suggested. This application is for a electronic card cage that will reside inside of a sealed cabinet with max temp swings of -5 to 65 °C. Appreciate any help or advice. Petaluma, California 1996 Stephen-- we are working on an aluminum electronics enclosure that gets installed in emergency vehicles. the aluminum must be coated/plated with a conductive layer that resists corrosion. I'm familiar with electroless nickel but have never heard of it being used on aluminum. please tell me more... we are having chronic problems with color and consistency of a chromate conversion layer. nickel sounds like a good idea. --mark Mark D. Andersonmetal works - Mequon, Wisconsin 1999 Mark: Electroless nickel will cost more, but it's no technical challenge. Plating onto aluminum simply requires the correct pretreatment sequence, which includes a zincating step whereby zinc metal displaces a few microinches of the aluminum; and then the plating sequence plates onto the zinc surface. Stephen: It really depends on exactly what is meant by "maximize conductivity". Only precious metals remain free of tarnish and actually present a metallic surface to the atmosphere. But electroless nickel is widely used on thousands of applications like charging contacts on cordless phones, DC adaptors, etc., because the tarnish is thin and the good looks and good conductivity are maintained. Tin is fine as a permanent contact surface (you make contact and stay in contact) and in fact it used to be used for the contact fingers of some circuit boards. Electroless nickel is quite corrosion resistant and perhaps the ideal material for the application down in a hand hole in the ground. But not if the finish may be scratched away because the reaction couple between nickel and aluminum will cause rapid corrosion of the aluminum if it is exposed. Good luck. ![]() Ted Mooney, P.E. Striving to live Aloha finishing.com - Pine Beach, New Jersey 1999 |
Q, A, or Comment on THIS thread -or- Start a NEW Thread