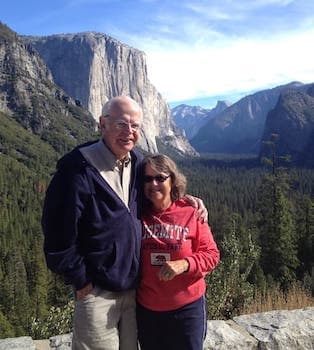
Curated with aloha by
Ted Mooney, P.E. RET
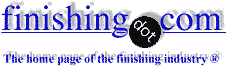
The authoritative public forum
for Metal Finishing 1989-2025
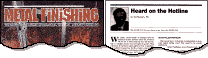
-----
Dirty Black Oxide
Our company is a small tool manufacturer, where we produce tools for the drilling and driving market. We are currently using sub contractors for chemical hot black oxide for some of our components which include high speed steel and 12L-14. The problem that we are having is that the black oxide is very dirty, meaning that when wiped with a soft cloth we get a lot of brown and black residue left behind on the cloth. The result of this dirty finish is that it leaves residue on the packaging and makes for poor presentation to our customer. I have spoken with our sub contractors about this issue on many occasions and they have assured me that this condition is very typical for chemical black oxide. Does anyone have a solution or explanation for problem?
Ken FunkeTool mfgr. - Ronan, Montana, USA
2004
In my experience this does happen with cold black oxide, which is actually a copper selenium compound deposited on the parts. It should not happen with true hot black oxide. Look at rifle barrels, the great majority of which are black oxide; they certainly don't have a dirty finish.
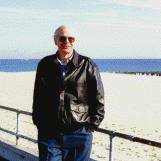
Ted Mooney, P.E.
Striving to live Aloha
finishing.com - Pine Beach, New Jersey
2004
I have read your reply to my problem of dirty black oxide and agree with your response. Previously speaking with my sub-contractor, I had also mentioned the condition of rifle barrels and how clean they are. Their reply to me was that all black oxide, including rifle barrels, gets a wipe down to remove excess residue after blackening and this is part of the normal process. I also know that they are using a hot blackening process as is our secondary sub-contractor, which by the way is also having the same problem with excess residue left on the substrate. What gives, can you suggest remedies or solutions to this problem.
By the way, I think that finishing.com is very informative site that I visit quite regularly, Thank you!
Ken Funke- Ronan, Montana
2004
The problem is the "L" which stands for smeared lead on the surface which makes the black iron oxide muddy. Leaded steel must be dipped thru 50% Fluoboric Acid to remove the lead smears from the surface - then the finish will be much better but never perfect because of the lead left behind.
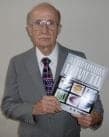
Robert H Probert
Robert H Probert Technical Services

Garner, North Carolina
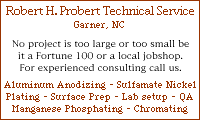
2004
Q, A, or Comment on THIS thread -or- Start a NEW Thread