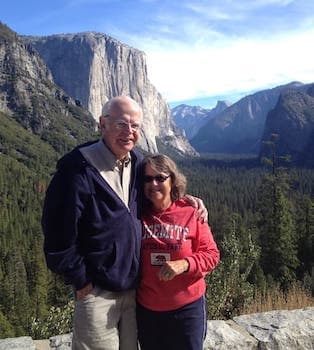
Curated with aloha by
Ted Mooney, P.E. RET
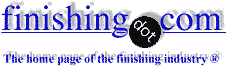
The authoritative public forum
for Metal Finishing 1989-2025
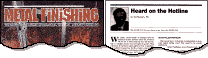
-----
Plating out waste nickel
I am a neophyte waste treatment tech with a background in hydrogeology and hazardous waste. The company that I work for goes to great measures to recycle all of the gold that fails to land on our electrical connectors. However, this company chemically precipitates and disposes of as F006 hazardous waste from 25 - 50 lbs of nickel per week.
It would seem to be more cost effective to plate out our waste nickel baths and resin backwashes so that we can recycle a more valuable product. I would love to hear from people who can recommend books of the "Electroplating For Dummies" ilk, as well as those who have had this idea and explored the possibilities. People have thrown words at me like electrowinning, "gold bug" and moron. Can anybody explain what they are talking about?
Stan Krajewskiwaste treatment - plating - Portland, OR, USA
2004
In this context electrowinning means electrolytic recovery or electrolytic plate-out of the metal from the wastewater. When you electroplate metal out of solution, you find that only a portion of the electricity you put into the effort actually causes metal deposition. Another portion of it goes to liberating hydrogen from the water. Unfortunately, as the concentration of metal in solution drops, the portion of the current wasted to this evolution of hydrogen rises asymptotically. To plate metal out of wastewater to concentrations approaching discharge limitations requires high solution turnover, very large electrode areas, etc. There are also practical and safety issues in electrowinning, including the explosive nature of this hydrogen gas, the possibility of the finely divided powders you are plating out catching fire, and the possibility of short circuits if the metal buildup causes the anode to touch the cathode.
For all these reasons, although electrolytic plate-out is a viable technology, it is best to purchase equipment made for the task rather than waste your time trying to plate the metal out in a conventional plating tank. You may also find that you need to use ion exchange technology to concentrate the metal values in the wastewater before you apply electrolytic technology to remove them.
Gold bug is a trade name of a brand of electrolytic cell used for recovery of precious metals; the same vendor has other electrolytic approaches to other problems.
"MORON" is an acronym for "man of remarkably outstanding nowledge", so be proud.
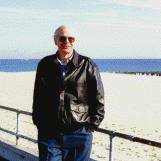
Ted Mooney, P.E.
Striving to live Aloha
finishing.com - Pine Beach, New Jersey
2004
First of three simultaneous responses --
It seems that a "K" is missing in knowledge. NOTION (with a pure latin root but still english), would fit the acronym perfect.
Best regards, Ted.
Guillermo MarrufoMonterrey, NL, Mexico
2004
Second of three simultaneous responses -- 2004
Stan,
Nickel is not the same as gold. In order to sell your nickel for anywhere near the market price, it must be quite pure, shiny, thick, heavy, and in a convenient form. A good example of ideal form are the electrolytic nickel squares commonly used as anodes. Removing nickel from a solution, electrolytically, is difficult. When you attempt to use an inert anode (one that doesn't dissolve), you will find that the pH drops rapidly. As the pH drops, the plating efficiency becomes less and less and, at about a pH of 1.5 (a guess), no nickel will plate out. At the inert anode surface, the current splits water, forming oxygen gas (O2) and hydrogen ion (H+). The oxygen gas comes off and the H+ stays in the solution and lowers the pH. You may think that you could use some hydroxide or carbonate to raise the pH. This may work for a very short time but will eventually poison the solution, creating a massive mess of ugly plated nickel (and, salts) at the cathode which would be impossible to sell.
Unless you start with a full strength plating bath, containing no impurities, and operated within parameters, the quality of the plate will be too poor to sell. Quality plating will never be achieved from weaker drag-out or rinse solutions. Plus, unlike weak gold solutions, you will never be able to plate out all of the nickel. If fact, you may not be able to plate out hardly any of the nickel from a very weak solution, due to the cathode inefficiency (see Hal's post). Whatever is left will have to be removed by your present precipitation method, anyway - you might as well do that to start with. In a commercial electrowinning operation, impure nickel is used as the anodes, in a full strength, highly maintained bath. Instead of splitting water, the current is used to dissolve the nickel anodes, thus somewhat stabilizing the pH at the higher level needed for efficient plating. Of course, the use of nickel anodes would defeat your purpose.
To keep your company from wasting a lot of money, I would stay with the present precipitation method. It's cheap, fast, and efficient. You're already set up for it and, it works! Your heart's in the right place - you just picked the wrong project. In this case, if there was a good way, everybody would be doing it.
My favorite book for the practical (after you get past the 1st chapter) chemistry of the various plating solutions is the 800 page, "Modern Electroplating" edited by Lowenheim. You can pick up a used 3rd edition on the internet for about $40-$50 [on AbeBooks, eBay, or Amazon affil links] . For equipment and setup (plus a ton of other stuff), you can't beat the massive Electroplating Engineering Handbook ⇦ this on eBay, AbeBooks, or Amazon [affil links] . It's expensive. A used 3rd edition casts $275. Your first buy should be a used copy (I like the ones from the 60's or 70's) of the "Metal Finishing Guidebook and Directory", for about $10-$40. It's published every year, revised very seldom, and covers all of the basics in about 900 pages. You will find that very little has changed in the past 40 years, except for the environmental issues, different suppliers, a little hi-tech specialized stuff, and a few new improvements in the additives. These great old books are nearly as up to date today as they were when new.
Chris Owen- Houston, Texas
Third of three simultaneous responses --
I knew some of those things about nickel recovery in a vague fashion Chris, but you have enlightened me and presented the problem very clearly. Thanks. In regular nickel plating the pH rises because anode efficiency is less than cathode efficiency, so hydrogen is liberated, leaving OH- behind. Is it within the realm of possibility to gainfully employ insoluble anodes then to maintain pH without the addition of buffers?
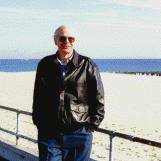
Ted Mooney, P.E.
Striving to live Aloha
finishing.com - Pine Beach, New Jersey
2004
Ted,
You could use inert anodes in a membrane divided tank. The nickel solution would go in the cathode chamber and some sort of mild electrolyte would be in the anode chamber. The anode would still generate H+, but it would be blocked by the membrane from entering the nickel solution. Here again, you wouldn't get much plating from weak solutions and you still would have to ppt. out the remaining nickel.
A better way would be to start out with a brand new nickel plating tank dedicated for nickel recovery only. In it would be a fresh, full strength, watts nickel bath with a stress reducer or, better still, a Ni sulfamate solution. You would operate it just like a regular plating solution - temp., filtration, maintenance, etc. Bagged carbon anodes are used. You analyze the solution. often and keep it up to par. Replenishing the nickel and raising the pH back up can be done simultaneously with nickel carbonate. It is obtained by adding sodium carbonate ⇦ this on eBay or Amazon] to the weak nickel waste solutions and filtering and rinsing - nickel carbonate is formed stoichiometrically and would probably result in a disposable waste solution. The nickel carbonate could be added by packing it into a filter. Passivated stainless sheet cathodes are used. If you mask the edges of the cathodes, the nickel plate can be more easily removed.
Chris Owen- Houston, Texas
2004
Some good discussion on recovering the nickel or not. My own approach is to ask why treat it in the first place? Why not put it back in the plating tank? Most nickel baths are heated and have some evaporation. If you capture the rinse water before contaminating it with other processes and then run it through particulate and carbon filters it is fit to add back to plating. One key is to use good quality (deionized) water for your rinses and to use counterflow rinses. You can enhance evaporation of the plating bath if necessary, or reduce the captured volume by evaporation. We have been doing this without fail for over twelve years. We almost quit buying nickel sulphate and chloride, too.
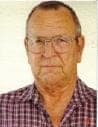
Paul Morkovsky
- Shiner, Texas, USA
2004
Q, A, or Comment on THIS thread -or- Start a NEW Thread