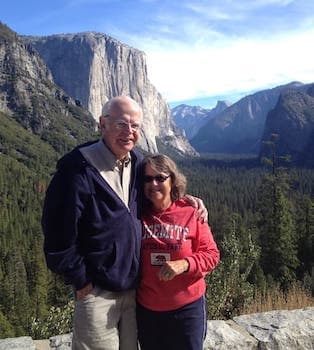
Curated with aloha by
Ted Mooney, P.E. RET
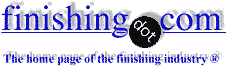
The authoritative public forum
for Metal Finishing 1989-2025
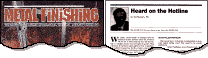
-----
Nickel Sulfamate Plating Problem: Adhesion Is Poor
2004
Q. My facility repairs turbine aircraft engines. We plate sulfamate nickel, electroless nickel, chrome, silver, and cadmium. I am the chemist in charge of maintaining the plating and cleaning tanks. I have been with the company about six months and while I have considerable chemical background I have never worked with plating before and have found that plating is a whole new ball game. Frustration is common and there is no one at my facility who can offer any advise.
Our problem is with nickel sulfamate adhesion. We are attempting to plate a stainless steel turbine shaft. It has both a inner and an outer diameter that require plating. We are having more problems with the inner diameter than the outer diameter but both have a high rate of failure. When the part goes to machining the plating spins off in a pretty ring. It's like there is no adhesion at all. This has been a problem off and on for a number of years.
We have two sulfamate plating baths. It seems that one has a higher rate of failure than the other but we have yet to determined if this is just coincidence. My analytical method calls for the tanks to be maintained at:
9.0-11.5 oz/gal nickel metal
0.4 oz/gal nickel chloride
5.0 oz/gal boric acid
pH: 4
Actual tank concentrations vary:
Tank #1:
12.9 oz/gal nickel
1.9 oz/gal nickel chloride
46.6 oz/gal nickel sulfamate
5.1 oz/gal boric acid
pH: 4.07
Tank#2:
13.4 oz/gal nickel
0.5 oz/gal nickel chloride
54.9 oz/gal nickel sulfamate
5.1 oz/gal boric acid
pH: 4.18
Can a problem be created when the nickel metal concentration and nickel sulfamate concentration are above the upper limit? Our tanks do not have a high usage rate and the nickel metal numbers have been increasing over time. One of the tanks (Tank #2) got too hot over the Christmas break. Last week I had a gentleman tell me that this may have caused a nitrate contamination problem and that could be my issue. Does this seem logical? Does anyone have a method for nitrate analysis of a plating solution? We utilize a Woods nickel strike. I have ruled that tank out as my problem. We also use the Woods nickel strike for our silver, electroless nickel, and Ni-cad plating and have not had problems with those processes. We dummy plate and carbon filter this tank on a regular basis. Please let me know if I should still consider this tank as a culprit.
We have parts other than the turbine shafts that are run in the nickel sulfamate baths and do make. The platers want to blame my plating tanks, but I think it may be an activation and cleaning issue. I am very confused. Any advise would be appreciated. Sorry for the length, I wanted to include as many details as possible. Thank you for any advise. Jennifer
Jennifer Doubledeeplating related to aviation - Neosho, Missouri, USA
![]() |
A. Jennifer, Could you describe the cleaning steps prior to the Woods strike and also the current density and time in the strike? Also if you had access to some ferroxyl solution apply some with Q-tips ⇦ this on eBay or Amazon [affil links] to an area that peeled and if it turns blue that will tell you the adhesion failure is between the base metal and the Woods strike. If it doesn't that will tell you the failure is between the strike and the sulfamate tank. Other things to look at would be stress in the sulfamate deposit. Is there excessive transfer time between the strike and the sulfamate bath? I personally don't think the high metal is the problem. There are test strips for Nitrate contamination that most good lab supply companies have. Hope this helps. Rick Richardson, MSFDayton, Ohio 2004 A. Tank 1 is too high in chloride which causes the metal to dissolve too fast and increase in concentration, also high chloride cause high stress (which in the case of poor surface preparation will peel right off) Tank 2 you got too hot, that caused the sulfamate radical to break down and form ammonium ions which cause brittleness which in the case of poor surface preparation will flake right off. I suspect your "Woods Strike" has crept up in nickel concentration because you do not remove the anodes when not in use. As the metal rises in a low efficient hydrogen scrubbing nickel strike bath it converts to a high efficient nickel plating solution and will not activate stainless steel. Dump it and start over with 32 av oz per gallon of Nickel Chloride plus 32 fluid ounces of Hydrochloric acid AND TAKE THE ANODES OUT WHEN NOT IN USE ! ![]() Robert H Probert Robert H Probert Technical Services ![]() Garner, North Carolina ![]() 2004 |
? Please give us your cleaning and activating process.
Russell Richter- Danbury, Connecticut, USA
2004
![]() |
A. Two excellent advises. I would only add that, if you're not doing it yet, you should analyze stress in the plate with a contractometer. Inner diameter needs a slightly compressive stress to push a little bit against inner walls, while the outer one would benefit if slightly tensile. This can be tailored in your same bath with a little experience. For more details, you may want to contact the Nickel Development Institute. They can send you copies of very informative technical papers. Guillermo MarrufoMonterrey, NL, Mexico 2004 A. Jennifer, Mr. Probert is certainly right, but check also your cleaning and activation processes. Out of my experience, when one has trouble with adhesion, the culprit lies in most of the cases in the preparation, especially when plating turbine shafts. Silvio Lusentiaircraft engine service - Zurich, Switzerland 2004 A. You left out a few things. what temp and ASF are you striking and plating at? How high did tank two get? Tank makeup / limits is governed by the OEM who built the part and has the repair process. Having three OEM's to placate, I combined the three and took the resulting most critical (restrictive)limits. I assume that you are waxing this part. Will it pass a water break test after the caustic clean rinse? Are you using pumice? If so are you getting it all out of the edges of the wax. If there are a few particles left and you are doing a heavy build, it will grow huge nodules. If you have huge nodules and the machinist cuts from the outside in, you have a good probability of tearing the plate. This force combined with a poor or marginal adhesion is enough to make it come off as a ring. The machinist can help by taking smaller cuts, working from the center to the outside until the bulk of the nodule is removed. Another evil that the nodules cause is an interrupted cut. This is a high demand on the plate. Next, what are you using for anodes in the Woods Nickel. I had adhesion problems using nickel rounds, especially when the tank started to smell. My preference was for rolled depolarized nickel anodes which do not have to be pulled from the tank except in several days of projected non use. I found that my nickel growth rate in the woods tank increased as the amount of nickel increased. I did my makeup with near the low end of my range of nickel and used 3/4 of my allowable HCl range. The high acid low nickel worked the best for me. This affected how well the strike held and sure seemed to make the sulfamate stick better to the strike. This may be because it made me feel good and was not a reality. I tried to strike at 80 ASF as the optimum is 100 ASF, but falls like a rock above 110 ASF. You do not mention your acid etch or the type of SS. That makes a huge Difference. If it is not activated, it can not stick! Reduce your transfer time from the strike to the sulfamate nickel. James Watts- Navarre, Florida 2004 |
I would like to thank everyone for their information and apologize for my delay in responding. We changed the smut remover in our cleaning and activation process to a cyanide based compound. We have several cyanide based plating tanks and are aware of the extreme hazard of using such a chemical. It appears to have had a positive effect on the adhesion problem. I say "appears" because it is too early to declare immediate success but there is definite positive trend. We had been having problems with smut removal and achieving a good clean surface without having to use some form of mechanical means to remove the smut. This new chemical is removing the smut successfully. We have made a few changes to the nickel sulfamate tanks that include more carbon filtering and increased boric acid. This may also have had a positive affect.
- Neosho, Missouri
2004
A. If you are getting smut, you are over-etching the part. If you are using anodic sulfuric acid, you can look up a high amperage/low amperage etch.It reverses polarity somewhere in that process. It has been a very long time since I used it and was not fond of it at that time. Boeing likes using a sulfuric/hydrofluoric on some of there high strength steels. McDonald Douglas (now Boeing) actually was able to get good adhesion plating over the sulfuric/hydrofluoric smut on landing gear material. No doubt about it, cyanide is a great smut remover.
Increased boric content is not really possible. 5.1 is a saturated solution at 120 °F. When you shut the heat off, you will have a heavy layer of boric crystals on the bottom of the tank.
James Watts- Navarre, Florida
2004
A. 1. electroclean with current FORWARD AND REVERSE 20 ASF for 5 minutes (be sure to exit cleaner on reverse current)
2. rinse (be sure to rinse very well, and that your rinses are clean)
3. 50% hydrochloric acid pickle with reverse current 20 ASF and a carbon anode (room temp, 4 minutes)
4. Woods nickel strike (50 ASF MINIMUM)
5. rinse, rinse..(again, clean rinses, check the PH)
6. sulfamate nickel plate 20 ASF (enter bath HOT (with current)
Jeff Scott- CP, Minnesota, USA
2004
? Is the poor adhesion taking place between the nickel strike and the nickel plate or to the base?
Matt RyanPlater - Lincoln, Rhode Island USA
November 18, 2019
adv.
"The Sulfamate Nickel How-To Guide"
by David Crotty, PhD
& Robert Probert
published Oct. 2018
$89 plus shipping
Q, A, or Comment on THIS thread -or- Start a NEW Thread