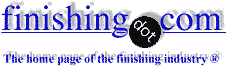
-----
Problems with thinning of pressed sheet metal
We are currently busy on a project that consist of some complicated forming. The part is to be used as a cover on a radio modulator. The part is to be pressed to a curtain form. We finished machining the forming tools but have lots of problems with thinning at some areas. The part's dimensions when pressed is about 150 mm x 120 mm. We are currently using 0.30mm tin sheet to press the part. Is there any other steel available that can be nickel plated and can be used as a deep drawn material. The sheet could not be thicker than 0.30 mm. PLEASE HELP!
Divan SadlerElectronic packaging - Pretoria, Gauteng, South Africa
2004
When you say "0.3 mm tin sheet" do you mean tin-plated steel sheet? Thinning during deep drawing will always be a concern, but it can be controlled to acceptable levels using good manufacturing practices. Another question I have is regarding the Ni plating-- can this be done after the forming? If so, then I would recommend you proceed as follows:
1. Obtain cold rolled steel sheet that is at least drawing quality (DS using ASTM terminology), but more preferably DDS or EDDS. The Euronorm equivalent of these steels are grades DC01 to DC06 in EN 10130.
2. Investigate high quality forming lubricants from industry leaders like Irmco or D.A. Stuart. Discuss the application requirements with them and choose the best lubricant.
3. Perform forming simulations using FEM software such as Deform-2D. The output of these simulations should identify the areas of thinning as well as quantify the amount of thinning. Tool geometry, including punch radii, will be critical for determining this.
4. Plate the part with nickel after the forming operations. Electroless nickel is more common than electroplated nickel.
Toby PadfieldAutomotive module supplier - Michigan
2004
Thank you Toby for the reply. The material is indeed tin-plated mild steel & nickel plated after forming. I used FEM software called BLANKWORKS to help with the designing before hand. The software showed thinning at the one or two places of between 17% & 23%. I figured that this was not much and proceeded in machining of the tools.
Divan SadlerElectronic Packaging - Pretoria, Gauteng, South Africa
2004
Q, A, or Comment on THIS thread -or- Start a NEW Thread