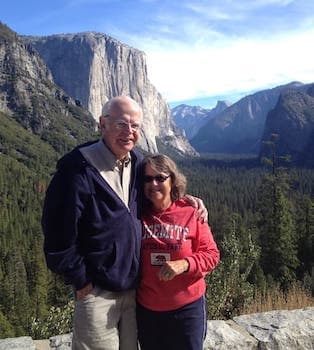
Curated with aloha by
Ted Mooney, P.E. RET
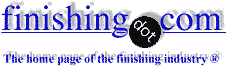
The authoritative public forum
for Metal Finishing 1989-2025
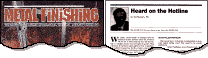
-----
Oxidization of printing press platfroms
2004
My company has just started to use galvanizing as a process to eliminate painting on printing press steel platforms. These platforms are used indoors so do not need corrosion resistance, it is only used as an alternative to paint.
We are not satisfied with the quality of the finish, we have some plates that have wet storage staining and others with varying degrees of oxidization.
What can be done in the galvanizing process to improve the finish of the product, what can we do to clean wet storage corrosion off the plates and what can we do to improve the appearance of all the plates with varying degrees of oxidization. Any help would be much appreciated.
Printing press machine manufacturer - Preston, Lancashire, England
Wet storage stain comes from getting fresh galvanizing wet in contact with other galvanized surfaces. (sometimes called "white rust".) It can be avoided by storage in dry conditions only, or if dampness cannot be avoided, by passivation. Some galvanizers passivate all their galvanizing as a matter of course, some do none. This chromate passivation will typically give about 6-8 weeks white rust prevention, and it usually long enough to get the product to installation / use.
Oxidation of the surface is normal. Galvanizing is a sacrificial coating, and protects by the zinc oxidizing in preference to the substrate (steel). The brightness of the fresh galvanizing depends on many things, but mainly on the amount of aluminium added to the zinc
(typically about 0.003%). In addition, the passivation mentioned helps the galv stay brighter longer. If you want a shiny silver finish for ever, then galvanizng is the wrong choice, unless you overcoat with a clear lacquer or similar.
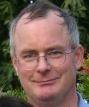
Geoff Crowley
Crithwood Ltd.
Westfield, Scotland, UK
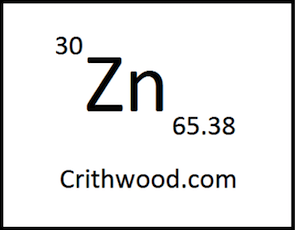
2004
Q, A, or Comment on THIS thread -or- Start a NEW Thread