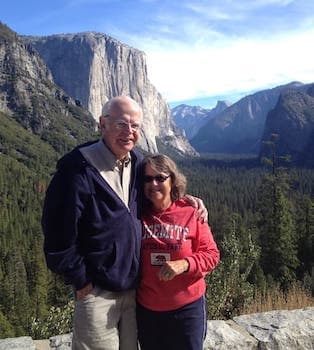
Curated with aloha by
Ted Mooney, P.E. RET
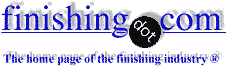
The authoritative public forum
for Metal Finishing 1989-2025
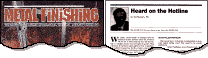
-----
Need help surface polishing 304 stainless steel discs
Q. Hello,
We are surface polishing 304 Stainless discs, 5.25" dia x .3125" thick. We are doing this using a rotating polishing table spinning at 300-500 rpm. It is done by hand using a small rod inserted into the center of the plate and pushed down against polishing paper. We start with 120 grit and work through 180, 240 and finish with 400 which gives us a close to mirror finish. Our problem is that it is extremely time consuming and not consistent from person to person. Our volume is increasing dramatically and I would like to find a mechanical or automated method of polishing. Any advice on where to find a method or machine would be greatly appreciated.
Electronics Mfgr. - Worcester, Massachusetts
2004
A. Besides production, what is the most important factor here, flatness, surface RMS, or mirror finish?
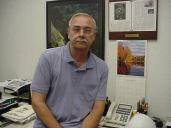
AF Kenton
retired business owner - Hatboro, Pennsylvania
2004
A. Al, the first question I would ask, is why are you polishing 304 stainless (2B or #4) to a mirror finish if it's already available in a mirror finish? At my company we use a 304 #8 non-directional mirror finish (one side) material that works great for us. It comes with a pvc coat on both sides. I'm not sure what your application is, and why you are polishing 304, but you should look into this material. It may be cheaper and definitely less time-consuming.
Martin MagañaManufacturing - Anaheim, California
2004
Q. AF,
Thanks for your response. A little bit more information may help: After we polish the plates to a 400 grit finishv(done mainly to get them flat and smooth), we vapor-hone them to a dull, grey finish. The clean, uniform finish is most important to these plates.
We then use the plates in a manufacturing process and they become scratched or stained which renders them useless. To remove the scratches we have to put them on a surface grinder and take a few thousands off of the surface(this is the only way we have found to remove the vapor-honed finish). Then we polish and vapor-hone again.
The problem is that the plates are easily scratched and hours of work can be quickly wasted by one slip of a production operator. We're really looking for a way to take the scratched plates and quickly re-finish them for production.
Martin,
Thanks for your suggestion. The mirror finished steel would be great for the first use but as soon as it is scratched we would be back to our original problem. I may look into this option anyway to save time up front.
Electronics Manufacturing - Worcester, Massachusetts
2004
A. I am still a little confused about your problem. It sounds as if you should be more concerned with protection rather than refinishing. In lieu of protection, maybe you should consider hard coat plating if it is acceptable. Regarding refinishing. I'm sure you are aware of disc lapping equipment. I am unclear if the problem exists on both sides of the part. If it is on both sides, there are double disc systems. I don't think I'd recommend any other mechanical method, considering your concern with flatness.
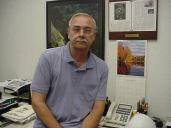
AF Kenton
retired business owner - Hatboro, Pennsylvania
2004
A. I polish tanks & wheels on trucks also do some car resto work. With stainless trim I use wheels on an old wood lathe, and different compounds. My final substance is to use dry powder cement . It brings up the shine an amazing amount.
Hope this tip helps.
- Sound Beach, New York
2004
Q. Dear sir ;
We are a manufacturer of disposable needles; in our process of nannula manufacturing we need mirror polish with dull shine; kindly suggest the detail for this process.
Thanks with regard;
healthcare devices - Rewari, Haryana, India
June 14, 2009
----
Ed. note: Sorry, we're unfamiliar with your industry. Was "nannula" a typo for "cannula"?
Hi, cousin Rajesh.
If you, as someone in this business, describe a specific step you do and the problems you believe it is leading to, I think you'll get good suggestions from the readers. But when you ask them to start at scratch and describe everything one must must do to establish a manufacturing process which is more capable than a successful company with all your experience has managed, it would be both impractical and insulting to you for them to respond :-)
Please get back to us with a specific process and issue. Thanks, and good luck!
Regards,
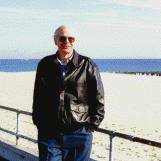
Ted Mooney, P.E.
Striving to live Aloha
finishing.com - Pine Beach, New Jersey
June 19, 2009
Q. I HAVE A CUSTOMER WHO WANTS A 304 STAINLESS STEEL PLATE TO HAVE A SURFACE FINISH OF .05 DO YOU KNOW IF THIS CAN BE DONE? THE PLATE SIZE IS 36 X 36 X 1/2
DENNIS GALLANTresale - Largo, Florida, USA
August 13, 2013
A. Hi Dennis. By ".05" do you mean an Ra of .05 micrometers or something else? An Ra of .05 micrometers is a very smooth finish equal to 2 microinches and is nominally what we would call "mirror polishing". It can probably be achieved by polishing and buffing, but don't expect to achieve it without investing many hours with successively finer grits.
You need to use a very fine buffing compound to achieve the final finish, but to get from relatively rough to .05 with a very fine compound would take the better part of eternity. You probably must use at least 5 or 6 progressively finer polishing/buffing materials, maybe more than that. Some people use India Ink for mirror polishing, as an example of how fine an abrasive may be required. There are a good number of threads about mirror polishing on this site, and many of them suggest actual detail on the various sequences I make reference to. Good luck: very patient searching will be good practice for the supreme patience you'll need to achieve mirror polishing :-)
Regards,
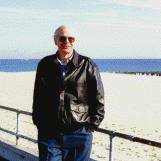
Ted Mooney, P.E.
Striving to live Aloha
finishing.com - Pine Beach, New Jersey
August 15, 2013
January 11, 2014
Q. Hello everyone,
My name is Jonathan and I'm just starting in the world of metals & finishings. I recently had a 4' x 10' sheet of #304 stainless cut into credit-card sized cards with designs in them. The laser cutting process has left some spatter on the back side of the metal as well as burn marks around the areas of the cut design.
I know there are shops that will refinish the surface, but I'd rather learn how to do it on my own. What's the best way to grind/polish/finish the surface back to a #4 finish? My research has given me a few options, namely:
- Hand-grind with successively finer grits
- Send to a finishing shop
- Drop in a vibratory tumbler for a few hours with silicon carbide
Are any of these the best option or is there something else I can consider?
Thanks!
John
- Burbank, California, USA
adv.
Our Scratch-b-Gone kit will allow you to fix all of these issues and very simply. Check it out.
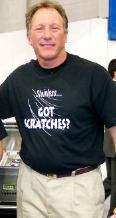
Barry Feinman - Chief Restoration Officer
BarrysRestoreItAll

Carlsbad, California
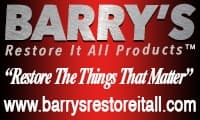
February 1, 2014
Finish for intraoral photography mirrors
Q. We want to make Intraoral Photography Mirrors in 304 Stainless steel, no scratches, no double reflections, very high polish -- so we need your help which kind of finish we use for this product.
Hashim Mustafadental Instruments - sialkot Punjab Pakistan
December 10, 2014
A. Hi Hashim. Although you need mirror polished stainless steel, I don't know if that alone is adequate for your application, or whether you must do rhodium plating or aluminum vapor deposition on the mirror polished stainless steel. If you can tell me what is typical for your industry, we can talk about how to achieve it.
Regards,
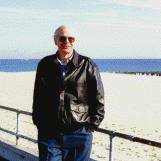
Ted Mooney, P.E.
Striving to live Aloha
finishing.com - Pine Beach, New Jersey
December 2014
A. To add to Ted's questions, I've got some of my own. Do you want to make parts in house? Do you have equipment? What is the size of your parts and how many?
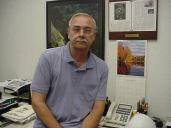
AF Kenton
retired business owner - Hatboro, Pennsylvania
December 11, 2014
A. Hi Hashim.
Provided the mirrors are plane (flat) it would be worth taking a look at metallurgical polishing equipment.
If the mirror is to be concave then lens grinding is the technology to investigate.
Both aim at the type of surface finish you need. Try Struers or there may be a metallurgical lab locally who could do a trial for you
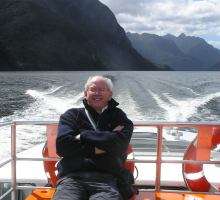
Geoff Smith
Hampshire, England
December 11, 2014
Q, A, or Comment on THIS thread -or- Start a NEW Thread