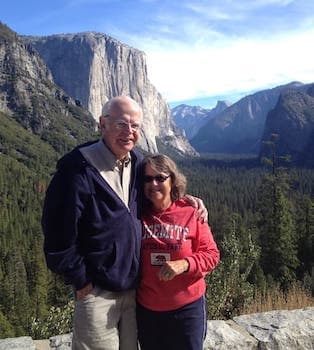
Curated with aloha by
Ted Mooney, P.E. RET
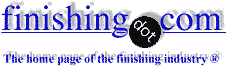
The authoritative public forum
for Metal Finishing 1989-2025
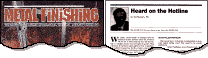
-----
Factors affecting the as-deposited hardness of EN-P
Greetings from Syracuse! I am hoping to demonstrate the power of networking to a co-worker by asking for your input on what parameters of an EN-P plating operation affect the hardness of the deposit. Thanks, mp
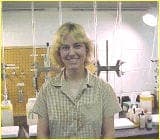
Megan Pellenz
- Syracuse, New York
1999
The results of your networking experiment would only have validity if it were double blind! Many of the factors which affect hardness in Electroless Nickel (EN) plating are well known, and you won't get too many useful answers the way your letter is posted.
To enjoy the benefits of networking, you must supply something valuable of your own; By telling us some of the things you are doing with EN, without giving away all your company secrets, you make the question interesting. When you pique someone's interest, you will often get information which you can use. It also is important when posting on the internet where search engines can find the keywords of your subject, like wear resistance, particular industry, particular industry buzz and trade words.
e.g.
( just made this up)
Hello,
I am trying to use EN to replace hard chrome plating for wear resistance on steel heddles used for a machine which weaves fishnets. 0.001 inches of conventional (sulphate catalyzed) hard chrome lasts approximately 6 hours net-making, while my lastest test with EN (5%P, heat treated), has given me 3 hours of net-making before failure. The hardness of the EN is 500 Rc, Taber Abraser 500 cycles. Does anyone have any information on maximizing the wear resistance of EN against polypro thread traveling at 5 feet per second through a Smith-Whitney Weaving machine?
Thank you,
Tom Pullizzi, Progressive Fishnet Institute of Southern Helsinki
(PFISH)
I will probably start getting email on my fictitious letter in a few weeks, and it won't stop until I delete the letter from the internet.
Regards,
Tom Pullizzi
Falls Township, Pennsylvania
Thanks for the lesson, Tom. When I said "networking" it was a veiled reference to The Net, the medium in which we are communicating. This allusion was easy to miss, I know. Your advice is right on target otherwise. Thanks again. MP
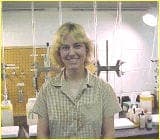
Megan Pellenz
- Syracuse, New York
1999
Phosphorous content and heat treatment would seem to be the biggies, Megan. But see "Hardness Control in Electrodeposited Nickel Phosphorus Coatings" by Narayan and Mungole in the Jan. '85 issue of Metal Finishing. (Thanks for your many fine answers to the other letters here, especially how to strip black oxide from copper).
I think Tom is gone pHishing this week :-)
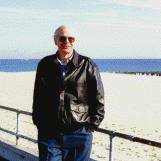
Ted Mooney, P.E.
Striving to live Aloha
finishing.com - Pine Beach, New Jersey
1999
I know this website is not a literary society, but I did ask my mom to jot down the Spanish poem about wanting nothing for nothing, for those who receive must give:
No quiero nada por nada
No te lo quiero tomar
Qué por entendido tengo
Qué él que toma-tiene que dar.


Tom Pullizzi
Falls Township, Pennsylvania
Megan - I agree with Ted, phosphorus content in the deposit and heat treatment have the biggest influence. It is the precipitation of Ni3P that increases hardness and improves wear resistance. Deposits typically consist of about 5 to 10% phosphorous; at 7% have 50% Ni3P and 50% Ni. Consequently one will see significant changes in properties around 7%. The phosphorus content in the deposit is strongly affected by the bath pH, increasing with decreasing pH, an increase in the hypophosphite concentration in solution and the bath temperature at a given pH. Several heat treatments are available to choose from. Be careful to choose one that is compatible with your substrate. From MIL-C-26074 [⇦ this spec on DLA]: 500F 4 hours minimum 550 2 min 650 1 to1.5 750 Ô to 1
Eric Barta- Renton, Washington
1999
Q, A, or Comment on THIS thread -or- Start a NEW Thread