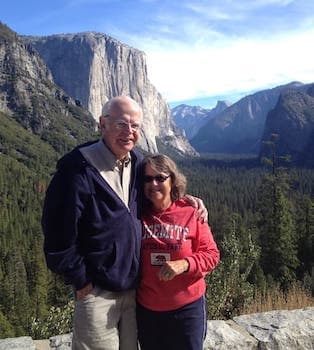
Curated with aloha by
Ted Mooney, P.E. RET
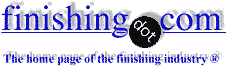
The authoritative public forum
for Metal Finishing 1989-2025
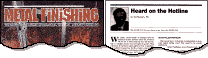
-----
Nickel Sulfamate Plating Cause of Stress
Q. I was wondering what is the cause of stress in a nickel sulfamate bath what is cause and how can it be controlled we currently carbon and dummy plate at 2 ASF for 3 hrs once a week our stress level is high. any reply would be greatly appreciated, our bath is Atotech. Thank You, Ernie.
ernie lehn- fountain valley California.
1999
A. Atotech is a big company with a wealth of information on this subject. Tech services can bury you with literature on the subject. What your process is doing, is controlling the tramp metals like iron and copper. The carbon treatment will remove the "amenable to treatment" organics which is not all organics. If you can get by with your customers, using a small platinized titanium anode at a fairly high anode current density will break down some of the sulfamate portion and yield a stress reducing product. As I remember a 1/8" rod about 15" ,bent into a circle, at about 5 volts would drop a 300 gal tank from 12,000 to 5,000 in 24 hours. Cathode was about a foot away. We did this in a small side tank with solution pumped to it and overflowed back to the main tank. For whatever reason, we found that stress would rise much more rapidly after it got to 10,000 so we would give it a shot when it reached that point. Simple, relatively cheap and a lot more functional than feeding it saccharin.
James Watts- Navarre, Florida
1999
A. We have found that the primary factors influencing stresses in Ni sulfamate deposits include bath chemistry (especially metallic impurities), pH, current density, and temperature as well as exercising care in performing the spiral contractometer test.
Bath chemistry is checked and adjusted as required prior to performing the spiral contractometer test. Metallic impurities can significantly increase tensile stresses in the deposit. We typically dummy plate in between loads at 3 to 5 ASF (or higher depending on experience) and have found that a minimum of 4 hours is required to keep metallic impurities at a low level. It is important to adjust the current density; for example, iron and copper are removed at different current densities. The use of a corrugated plate will help do this automatically. The Metal Finishing Guidebook recommends that chrome concentrations be controlled to levels less than 0.01 ppm. Small concentrations are known to cause significant increases in tensile s! tress. We have found that it is best to isolate Ni plating tanks from chromating or chrome plating tanks. Other contaminants that need to be controlled include lead, zinc, iron and copper. Concentrations listed in the Handbook are a good place to start but may vary based on experience. The Handbook also illustrates the effect pH and current density on intrinsic stresses. A pH of 4 will help minimize tensile stresses, above 5 they begin to rise rapidly. We control the pH between the range of 3 to 5. The effect of current density is more complicated. Stresses decrease as current density increases to about 75 ASF where they remain relatively flat until 100 ASF and then begin to increase. Stresses are also induced by changes in temperature. It is important to zero the spiral contractometer in the solution after the temperature of the contractometer and solution have stabilized; for example, at the plating solution temperature. Maintain the temperature at ± 2 F when plating the contractometer. In closing, measurement of the length of the plate and the weight of the deposit are critical and if not accurate may result in erroneous calculations.
Eric Barta- Renton, Washington
1999
A. Mr. Lehn: You might also want to check out "A Practical Guide to Understanding, Measuring and Controlling Stress in Electroformed Metals" from our on-line library.
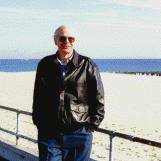
Ted Mooney, P.E.
Striving to live Aloha
finishing.com - Pine Beach, New Jersey
A. I agree completely with Eric's comments. I guess that I sort of took them as a given. Keep the chrome out! The only practical way to get rid of it is to dump the tank, so it is a lot cheaper to keep it out, almost at all costs. I used to maintain pH within 3.5 to 4.5 with daily checks and corrections. 120-130 F is about the best practical temp for having stress at the lowest rational point vs costs, plate rate and temperature destruction of the sulfamate radical. Adequate agitation helps in the tank and in the contractometer test.
James Watts- Navarre, Florida
1999
? What is your ammonia ⇦ this on eBay or Amazon [affil links] level in your solution?
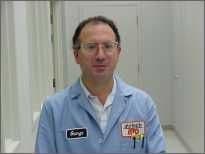
George Shahin
Atotech - Rock Hill, South Carolina
1999
adv.
"The Sulfamate Nickel How-To Guide"
by David Crotty, PhD
& Robert Probert
published Oct. 2018
$89 plus shipping
Q, A, or Comment on THIS thread -or- Start a NEW Thread