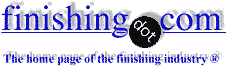
-----
JS500 vs E-coating
Can anyone explain the benefits to using a JS500 process vs a e-coating process?
John Peters- Minneapolis, Minnesota
1999
JS500 and E-coat cannot be compared because they are totally different coatings. JS was developed by Torcad in order to give extended corrosion without significantly affecting dimensions. It is in effect an electrolytically deposited coating of zinc, that is dichromate passivated and then leached back to white in the JS solution. This combination of sacrificial zinc, plus the chromate gel, which now contains JS and is covered in JS has self healing properties, and causes moisture to bead and run off. The result is that it gives a minimum of 500 hours to red rust from 0.0003" minimum coating, compared with 72 hours from zinc chromate. JS500 is used extensively in the automotive, agricultural and building sectors.
E-coat on the other hand is an electrophoretically deposited coat of paint, which is evenly deposited over the article to be processed. As it is a paint it can come in many colours, but is usually black. It is pretty flexible but like all paints when it is scored, rusting of the base metal can occur. To give more corrossion resistance zinc can be applied to the base material before E coating. If I remember correctly E-coat has a salt spray life of 240 hours. It is used mainly in the automotive sector.
Andrew Munro Macdonald- Burlington, Ontario, Canada
2000
If you can reference a published article evaluating the performance of JS500 we would like to refer readers to it.
It's probably true that E-coat "is used mainly in the automotive sector", but that does not mean it is rarely used in other sectors; it's just that it's difficult to compare any other use to the millions upon millions of vehicles that are e-coated each year.
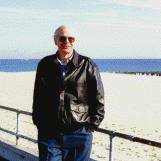
Ted Mooney, P.E.
Striving to live Aloha
finishing.com - Pine Beach, New Jersey
2000
2005
On certaing Electro-zinc plated bolts we have reciently found a problem with hydrogen Embrittlement with bolts due to the baking time not being sufficient, this has been difficult to control and are therefore looking into alternative to Electro-zinc plated bolts.
We have therefore discovered JS500 and Dacromet treated bolts, the JS500 we have dound give no degredation in the bolts hardness or yield strength but does not live up to the electro plated bolts in a salt spray test. We have been assured dacromet is more resiliant (but have not tested ourselves as yet)but during yield testing we have discovered that both the bolts hardness and yield strength have decreased.
Could you please inform us of the differences in the plating processes and how the daromet bolts properties have degradated so.
Yours Sincerely
- Bath, Avon, England
Q, A, or Comment on THIS thread -or- Start a NEW Thread