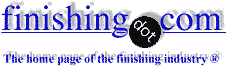
-----
Anodizing on 7075 Aluminum Flaking, Blistering, Pimpling
Quickstart:
Readers wanting a quick intro to anodizing of aluminum may wish to view our "Aluminum Anodizing (Anodic Oxidation of Aluminium) Intro".
2xxx and 7xxx alloys are more difficult and troublesome to anodize than 1xxx and 6xxx
Q. This is a great forum and very informative. Enlightened me on quite a bit of things.
I have an issue with Anodize Type 2 with potential flaking of the coating. I am finding foreign debris which I believe is from the Type 2 anodized coating after using ultra sonic cleaning, non-abrasive bristle brushes & dry fitting. This has been a pain in my a**. I will start post-coating inspection at a higher magnification to clearly view crazing & cracking. Does anyone have any other tips & tricks to prevent flaking of Type II anodized?
- Jefferson City, Missouri
September 28, 2024
A. Hi Peter.
Just one more thing that Robert Probert has mentioned on other threads but which didn't happen to have come up on this thread, and might possibly apply to your parts: sharp inside corners are a problem when anodizing. Because of the way that anodizing grows from surfaces, the anodizing on the two perpendicular sides 'crash' into each other which can cause crushing and flaking even without heat, but worse with it. Radiused corners always help.
Luck & Regards,
Ted Mooney, P.E. RET
Striving to live Aloha
finishing.com - Pine Beach, New Jersey
⇩ Related postings, oldest first ⇩
Q. We have a problem. When hardcoating a specific job made from 7075 alloy we are getting blisters on parts.
The job we are seeing the problem with is 2 different small (1.25" long x 3/8" wide x 1/4" thk CNC machined) blocks.
We first ran a sample load for the customer of 200 pieces of each & it ran flawlessly. Next we ran another sample load of 100 pieces of each. The 100 of each were on the same rack & one style part came out with the blisters & the other did not.
I found an article in the August 2000 issue of "Products Finishing" which blames the problem on the material. It says:
"Its all about dissolved gasses found in aluminum billet. Since hydrogen gas is soluble in aluminum, it sometimes precipitates out of solution in the process of being converted from the ingot to heat treated billet. The hydrogen may come from excess humidity present during heat treatment, the presence of moisture in the casting furnace or in the aluminum "charge" used in billet casting. The precipitated hydrogen forms pores in the aluminum billet. When extruded, these pores collapse, but instead of "healing" they form an interface between the flattened pore or void & the metal around it. As the anodic coating grows inward during anodizing, these interface areas become potential sites for blistering. When the coating reaches an interface it can actually separate from the substrate, forming a blister..."
We have hardcoated 7075 aluminum for over 40 years and really never saw this problem. Last year we found it on a different job & that's when I found the article. That customer accepted the blistered pieces along with a copy of the article. The new customer / job says that while they understand the article, it is a govt job & the govt will not accept the parts like this.
Anyone else have this problem or know of a fix or minimize it?
David A. Kraft- Long Island City, New York
2001
A. Dave,
We too, have seen this problem a few years ago. The article you found is interesting. We assumed the problem was due to overheating of the parts (one of those "shot in the dark" guesses. We reduced our tank temperature to 30 °F, and it seemed to solve the problem. If the article you found does in fact state the real cause of this problem, I can't answer why lowering the tank temp solved it. As this is not SOP for us, I'm also wondering if stripping and reworking the parts had anything to do with our results...perhaps getting past the "pore, or void" that the article mentions?
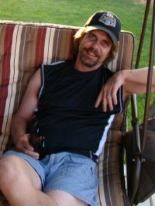
Marc Green
anodizer - Boise, Idaho
Bubbles under Hard Coat
Q. A vendor is providing a MIL-A-8625 / MIL-PRF-8625 [⇦ this spec on DLA], Type III, hard coat for aluminum parts. Some of the material exhibits a small bubble under the hard coat (looks like pepper flakes trapped under the coating). Some of the larger bubbles will flake off, appears to be some form of corrosion. The MIL standard seems only to address corrosion (pitting) on Type I & II coating, nothing specified for Type III. Is there a "best practice" criteria that would apply, i.e., none, or 'X' number sq/in?
Glenn TibbettMilitary Repair - Barstow, California, USA
2004
70xx series aluminum alloy?
Chris Jurey, Past-President IHAALuke Engineering & Mfg. Co. Inc.

Wadsworth, Ohio
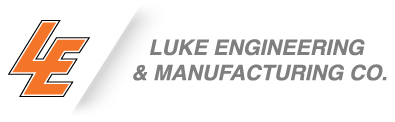
A. OBVIOUSLY YOUR VENDORS SURFACE PREPARATION WAS NOT GOOD. Had the parts been mechanically abused by time saving, sanding, bead blasting or such, in which case non-aluminum and hence non-anodizable matter, would have been imbedded into the surface and left to "bubble out" later. Or he did not clean, or he did not deoxidize and remove all of the aluminum oxide before applying the "controlled oxide".
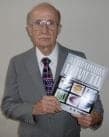
Robert H Probert
Robert H Probert Technical Services

Garner, North Carolina
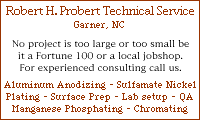
A. WE HAVE HAD THE SAME PROBLEM, THE BUBBLES COME FROM TRAPPED HYDROGEN THAT FORMS IN THE MANUFACTURE OF THE ALLOY (7075). AS THE HARD COAT FORMS IT TRAPS THE GAS IN THE ALLOY,WE ONLY HAD THE PROBLEM WHEN WE DYED THE HARDCOAT AFTER PREPPING IT FOR 3 MINUTES IN NITRIC ACID DEOX BATH. I THINK THAT THE DEOX WEAKENED THE COATING AND ALLOWED IT TO BUBBLE WHEN IT WENT INTO THE 140 DEGREE BLACK DYE. IF THE PARTS WERE NOT PREPPED AND DYED THERE WAS NO PROBLEM WITH BUBBLES.
GOOD LUCK,
LARRY COHENANODIZING - WACO, TEXAS
Q. Some 7075 parts were type II anodized 20 micron thick (.0008") per mil-spec. They were subsequently cleaned in a cleanroom, in ultrasonic cleaning stations with D.I and (supposedly) anodize-safe detergents, dips in isopropyl alcohol and D.I., and a vacuum bake approaching 100 °C.
When the tape was repositioned, the anodized finish came off. Based on a lit search and preliminary theories, the client blamed ultrasonic cleaning for crazing the parts, and alcohol of dehydrating the parts. Either or both processes may theoretically be deleterious, but subsequent study, described below, seemed to me to point away from either being the real problem.
The parts were chromic-phosphoric acid stripped (the shop doing the stripping was surprised how fast they stripped; this may have been due to the large surface area of the defective coating).
The anodizing was redone in thicknesses of .0003", .0007", and .001", finishing with an hour and a half of nickel acetate sealing. The coating still cracks and comes off at thicknesses greater than .0003" as platelets before baking, and as "mica-like" multiple layers of platelets after baking.
A higher power photo of the .001" coating, however, (400x) revealed other than what I expected to see:
I admit to very little experience looking at anodized aluminum at 400X, but this doesn't look like crazing or dehydration to me. This "ceramic tile floor" with "grout" between the tiles looks more to me like extreme oversealing that caused so much expansion from growth of boehmite / hydroxides that it broke the film and continued to grow? When we tried sealing for very short times, these "grout" lines become very thin.
Then again, I may be misreading the micrograph, and I don't think we're down to root cause either. Anyone have comments on what they see, or a recommendation on mechanical prep before the chemical processing, or what to study? Thanks!
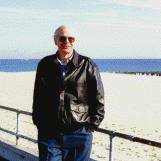
Ted Mooney, P.E.
Striving to live Aloha
finishing.com - Pine Beach, New Jersey
2004
A. We are Mil spec certified for type 2 anodizing and we seal our parts in nickel acetate at 175 °F for 10 minutes. Never failed a seal test.
Tim KnoxMetal Finishing - Springfield, Vermont, USA
Treatment &
Finishing of
Aluminium and
Its Alloys"
by Wernick, Pinner
& Sheasby
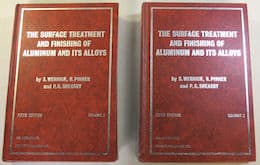
on eBay or Amazon
or AbeBooks
(affil link)
A. An interesting one, we've experienced a similar problem with delamination of the anodic film from 7XXX series alloys, on hard anodising, not quite in the platelet form seen in the pictures -- more of a gross de-lamination. Subsequent SEM and EDAX analysis showed evidence of contamination at the interface (when cross sectioned & mounted). So we off-line hand cleaned, the problem was minimised but still came back intermittently.
Consulting the "Surface Treatment of Aluminium" bible, the sealing section in vol II does give some details of the relation between stress and film thickness, with lower CD's giving more compressively stressed deposit. So we modified the voltage ramping cycle to incorporate a 10 minute dwell at a lower voltage giving a lower CD approx. 1/2 of what we would normally hard anodise this material at (reasoning maybe incorrectly that a lower growth rate initially would give the film chance to form a more coherent layer). Since then it's seemed ok. We still get crazing with this material (depending upon thickness), but no de-lamination.
Might not be anything to do with your problem, but perhaps something to try. Also 90 minutes sealing seems a long time? Does it de-laminate if it's not sealed ?
Best of luck, Regards,
Richard Guise- Lowestoft, U.K.
A. Could it be possible that thermal expansion/compression may be contributing to this effect? From cold anodizing solution to hot seal then cold alcohol then hot vacuum. That's a lot of extreme thermal differences.
Asyong Salungga- Toronto
A. I think that ultrasonic cleaning or heating has nothing to do with this problem. It is most likely coming from pre cleaning. Experiment with 6xxx Al and see if same problem arises. If you don't have the problem with 6xxx Al, than you should look into your cleaning process.
Mussadiq Hussain- Canyon Country, California, USA
Thanks for all the feedback, folks! I think step one is to stop doing things known to be wrong like sealing for an hour and a half, and if that doesn't solve it, go on to these excellent suggestions :-)
Regards,
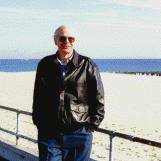
Ted Mooney, P.E.
Striving to live Aloha
finishing.com - Pine Beach, New Jersey
Heating/Baking causes 7075 Aluminum Anodize to flake off
Q. The material is 7075-T651 aluminum to be anodized per MIL-A-8625 / MIL-PRF-8625 [⇦ this spec on DLA] Type II Class 2. When we receive the parts they look fine, but one of our first processing steps bakes the part at 150 °C for 1 hour. After that, there are specks all over the part where the anodize has removed itself from the part and the rest is easily removed with tape. Any tips?
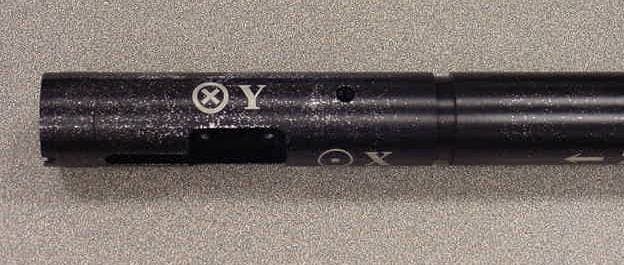
Jeffrey Mandl
Electro-Mechanical Manufacturer - Twinsburg, Ohio, USA
2004
A. TRY SHOTPEENING PRIOR TO ANODIZING. GOOD LUCK.
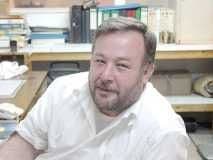
Khair Shishani
aircraft maintenance - Al Ain, UAE
A. With limited knowledge of anodising, I dare say that Cair Shishnani is on the right track; A glass bead peening; or a light polish using a silicon carbide emery belt may improve adhesion of the anodise.
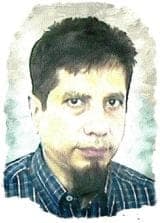
Khozem Vahaanwala
Saify Ind

Bengaluru, Karnataka, India
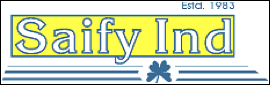
for Shops, Specifiers & Engineers
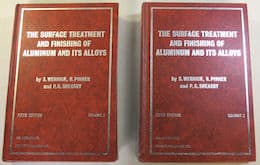
avail from eBay, AbeBooks, or Amazon
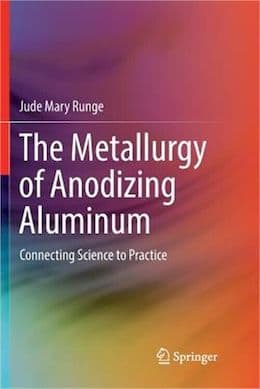
avail from eBay, AbeBooks, or Amazon
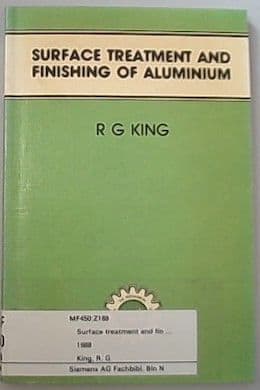
avail from eBay, AbeBooks, or Amazon
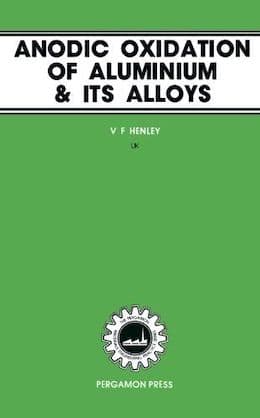
avail from eBay, AbeBooks, or Amazon
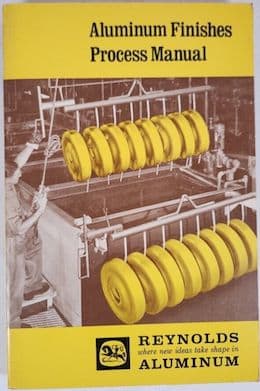
avail from eBay, AbeBooks or Amazon
(as an Amazon Associate & eBay Partner, we earn from qualifying purchases)
A. 1. Hydrated Aluminum Oxide has a different coefficient of expansion than 7075 aluminum. Sheasby and Pinner address this in their book.
2. Steel shot peening will imbed fine iron particles into the 7075 aluminum which will not anodize and will contribute to worse loss of adhesion.
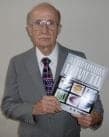
Robert H Probert
Robert H Probert Technical Services

Garner, North Carolina
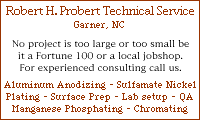
A. I agree with Bob.
We have seen a similar condition with Al alloy heatsinks, Type II anodized to 17µm coating thickness, dyed and sealed in boiling water. Gross overheating was allowed to occur in the power MOSFET that was generating the heat. The onset of cracked anodize was 145 °C. case temperature maintained for 30 minutes. The cracking (like an egg shell) occurred in a pattern that neatly shadowed the MOSFET package. When cracked, the anodize could be removed in small pieces. Thicker anodic coatings seem more susceptible to this than thinner coatings, since cracking can occur at somewhat lower temperatures with thicker coatings. The cause is no doubt the large differences in thermal expansion between Al alloys and aluminum oxide structures.
- Columbia, Maryland, USA
Ed. note: it is our sad duty to advise of the passing of Paul Yursis in August 2005.
Here is a brief obituary by Mike Caswell.
Hard Anodize Coating Blisters On 7075
Q. We are experiencing blisters in 7075 after hard Coat. Does anyone know why this happens, and how to avoid/eliminate them.
Joel A. Lipof- Paterson, New Jersey
2006
A. 1. With time and temperature, and especially with heat treating, the zinc migrates to the grain boundaries, when you anodize over these grain boundaries, it flakes off.
2. Work Hardening from dull tools or tumbling or blasting. When you anodize completely through a work hardened surface, stress flake the coating off.
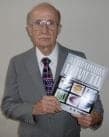
Robert H Probert
Robert H Probert Technical Services

Garner, North Carolina
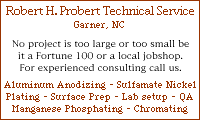
A. Blisters aka pimples are caused by intermetallic particles which block anodize growth into the metal. A particle holds up an area of anodizing which becomes detached from the metal as anodize growth continues in surrounding areas. Looks like an incipient volcano. Stresses create cracks radiating outward from the center into the uplifted anodize (actually, surrounding anodize has moved downward) through which acidic electrolyte enters and creates white sulphate corrosion. The undercut anodize & corrosion products can detach & get swept away, after which the bare metal area some 500 microns in diameter can begin anodizing anew.
In SEM analysis back in 1997, I found particles of primary solidification phases FeAl3 and Cu2FeAl7 at the core of developing blisters. These are coarse particles up to 25 microns in diameter which should not be present in wrought microstructures; they are not the sub-micron particles formed by heat treatment.
Re preventing blisters: Shot peening breaks up the intermetallics within the near-surface Al matrix to a small enough size so as to not blister the subsequent hard anodizing, and is a common procedure for helicopter manufacturers. personal discussion, Leah Markowitz, Senior Engineer, HR Textron, 1998 SUR/FIN conference. See also "Hard Anodic Coatings on Aluminum Alloys: Evaluation and Control of Porosity," L. Markowitz, Metal Finishing, p. 19-24 (December 1992).
As MIL-A-8625 / MIL-PRF-8625
[⇦ this spec on DLA]F, paragraph 3.3.2 could be interpreted as prohibiting shot peening, note: "Aluminum parts which have been peened with metallic shot shall be chemically cleaned" prior to anodizing. MIL-S-13165C [ed. note: or AMSS13165], paragraph 3.3.10.2 and MIL-P-81985, paragraph 3.5.2.1. Typically, this cleaning is a light etching followed by a nitric acid-type deoxidation.
The problem can also occur with Al 2024. The University of Illinois has developed an electrochemical process for removing intermetallics from the surface of aluminum alloys. Probably useful for applied coatings and chem film but not hard anodizing:
http://www.otm.uiuc.edu/attachments/T98002-092.pdf
- Goleta, California

Rest in peace, Ken. Thank you for your hard work which the finishing world, and we at finishing.com, continue to benefit from.
Multiple threads merged: please forgive chronology errors and repetition 🙂
Q. Hi,
Just a question, has anyone ever experienced pitting corrosion in the 2024-T4 material. EDS shows that chlorides are present in the pits. Is it the process line, or something else.
Your help would so greatly appreciated.
aerospace - vancouver, BC, CA
2006
A. Chlorides from dragged in tap water and/or fluorides from proprietary products anywhere in an aluminum treatment process line will cause pits. This is aggravated by the galvanic action between titanium racks and stainless steel tanks or heaters.
In old 2024 or heat treated 2024, the copper has migrated to the grain boundaries, where it is more rapidly picked out by chlorides and/or galvanic action, thus leaving behind pits.
Do a laboratory line with beakers, D.I.water, and fresh make-ups, and see if you can confirm what I have said above.
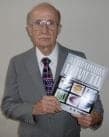
Robert H Probert
Robert H Probert Technical Services

Garner, North Carolina
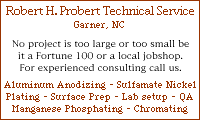
7075 MIL-A-6825 Type 2 Class 2 flakes after heating to 180 °C
Q. We have machined 7075 chassis. We have them black anodized using MIL-A-8625 / MIL-PRF-8625 [⇦ this spec on DLA] Type 2 Class 2. We have heated them up to a temperature of 180 °C. After cooling, the anodizing starts to "flake" off of the chassis. Is this a problem with the anodizing process or is the alloy of the 7075 changing properties after reaching these temps? We have done the same testing to 2024 & 6061 & have had no problems.
Jack D. McCormickOil well navigation tools - Twinsburg, Ohio
2006
A. Up front. I do not know, but I suspect that it is a function of the thermal coefficient of expansion. They are significantly different. On a small part, it would not make as much of a difference as on a large part. There is also a possibility that the center of the aluminum is retaining the temperature a lot longer than the oxide so that you would have the oxide shrinking much faster than the aluminum that is under it.
7075 has a relatively high non-aluminum content which does not anodize, so your adhesion of the oxide would not be as strong, which would also allow it to fail easier. Now, the important question. Why are you baking it to such a high temp. Lower would most assuredly be better for the oxide.
A third factor is you seal a certain amount of liquid in the sealed anodize. If you are baking relatively soon after seal, I would expect steam formed and cracking the pore walls of the anodize. Remember, anodize is not a solid. It is tightly packed hexagonal pores of a hard and brittle ceramic.
- Navarre, Florida
A. Like he said, the aluminum expands 5 times the aluminum oxide. Something has to give. Also the dye cannot stand that temperature.
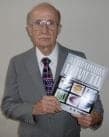
Robert H Probert
Robert H Probert Technical Services

Garner, North Carolina
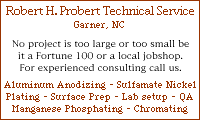
A. Reference NASA-TM-104622. I have had the same problem with different parts made of 7000 series aluminum . The answer is do not hot water seal or seal at all. Keep the anodize thickness at .0006" max. The problem goes away. There is a little loss of corrosion protection, but it beats cracks. It was all attributed to thermal stresses. See the NASA technical memorandum.
Steven EinfeldtSpace products - Chatsworth, California, USA
June 25, 2012
Multiple threads merged: please forgive chronology errors and repetition 🙂
Q. I have a part made of 7075-T75311 .It has been anodized per MIL-A-8625 / MIL-PRF-8625 [⇦ this spec on DLA] type 2 class 2. Square pieces of the anodize approx. .003"" square are flaking off the surface. I have examined some of the flakes in a SEM EDS; I find 35.6% oxygen, 46.8% aluminum, 7.2% sulfur, 2.8% copper, 2.7% zinc. I realize this is sulfuric anodize. I did not expect the sulfur to be present, it is on both sides of the flakes.
Was the anodized part poorly neutralized and rinsed? Any ideas what causes the flaking and cracking?
Steven Einfeldtengr. - Chatsworth, California, USA
February 20, 2008
A. The sulfur is from aluminum sulphate occluded in the pores. This probably has nothing to do with the flaking; however, it interferes with dye adsorption, and it can be reduced by
(1) cutting the anodizing solution down to about 8 gm/L dissolved aluminum and
(2) running the work thru a 5% nitric acid to flush out most of the aluminum sulphate before dyeing.
Regarding the flaking. How old is the 7075? Was the 7075 heat treated? Have you aged, heat treated and either tumbled or blasted the surface? Has the surface been work hardened?
In 7000's that have been aged or heat treated, the zinc migrates. If that grain boundary, containing the zinc, is close to the surface, then you anodize completely through and down to it, then it will (unplate) and flake right off.
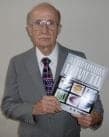
Robert H Probert
Robert H Probert Technical Services

Garner, North Carolina
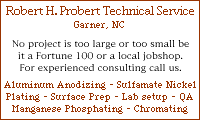
A. 7000 series aluminum is a favorite of aerospace. It contains a sizable amount of zinc and flaking after anodizing and dye is not uncommon.Changing pretreatment can help with some of these problems. I would try staying away from an etch or limit it to a very short time. I would also try Nitric and fluoride for deox to help remove the zinc from the surface.
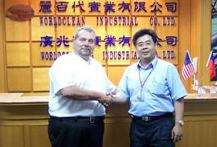
Drew Nosti, CEF
Anodize USA

Ladson, South Carolina
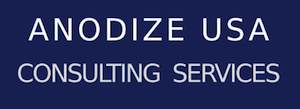
Q. I have been having problems with blisters forming on 7075. This is very rare I know and I have torn our operation apart and can't seem to find anything that we may have missed. I have seen delamination before but this is a new one. I have done a matrix of experiments to prove out our process. I keep coming back that there is something that is not right with the metal that we are trying to anodize. The problem is that it is very intermittent. I expect it to come back because we have not done anything to end the problem. What I can say is that we have processing 7075 for many years and consider it not that hard to anodize and have a long track record of success. I have been told by many that this could be a hydrogen outgassing problem. A problem that is created when the billet of aluminum is 1st made. What I would like to do is prove this with the data and move on with life. Any ideas how I could go about that?
Mike RobergAnodizing Operations Manager - Minneapolis, Mn, USA
June 7, 2009
![]() |
A. In heat treated or "old" 7075, the zinc has migrated out of alloy and into the grain boundaries as molecular zinc. If it is near the surface and you anodize though to it in some spots, the anodizing flakes off. ![]() Robert H Probert Robert H Probert Technical Services ![]() Garner, North Carolina ![]() A. Mike, - Belgaum, Karnataka, India June 16, 2009 |
Q. 7075 is a high strength alloy, but it is more susceptible to corrosion. I just started anodizing and have had much better luck with 6061. I noticed also severe pitting in some of my 7075 parts and was wondering if the coating growing from the sides of the pits is causing stress fractures as it grows against itself in addition to the other factors mentioned. I also wonder if lowering acid content in the anodizing process would help prevent pits and too rapid a growth.
Benjamin Craig- Eighty Four, Pennsylvania, USA
April 18, 2011
Q. I work at an manufacturing plant where we make parts for aircraft that require many sealing surfaces. We have been running a part made of 7075 (more specifically 7075-T73511) for years now. The part has a large sealing surface that has been continually rejected by our customer for scratches that don't even have a depth to them. The problem we are having is the scratches only appear after anodizing but never before. 100% visual is done at all steps throughout the process even at the anodizer. We have gone through our process as well as our anodizing supplier and have not found where the scratches are originating from. We lap the surface before anodizing and suspect that something is being impregnated into the material that doesn't show up until the anodize process brings it to the surface.
Josh Bugni- Valencia, California, USA
January 17, 2012
A. Hi Josh,
It will help if you can post some pictures of the part with the defect.
- India
Measles on Hard anodized 7075-T6
Q. We are having problems with Hard anodizing of 7075-T6 parts.
It appears that the coating produces multiple small bumps at the surface. These bumps are poorly attached to the base material as I could chip them off using a knife. See picture attached. The part on the image is about 2 inches high.
Any insight about what caused the problem and how to resolve / avoid it ?
Thanks,
- Quebec, QC, Canada
May 9, 2012
A. Typically, that is Zinc precipitate in this particular alloy.
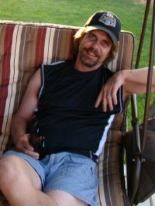
Marc Green
anodizer - Boise, Idaho
Q. OK about the zinc precipitate, but is there anything I could do to successfully anodize the parts anyway?
Benoit Gilbert [returning]- Quebec, QC, Canada
May 16, 2012
A. First things first, is that if you have SEM capability at your facility, I would analyze one of the blisters to confirm that is indeed the issue. I only have one part that I anodize that is made from 7075, and to date, I've never had issues. I know we're very careful about using Alcoa aluminum in this part that we manufacture. We use a HNO3 based de-smut, which may, or may not help you out, depending on how bad the precipitate is (if that is your issue)
If you do a search on this site, I know this particular question has arisen many times. You should be able to find numerous posts about this problem, and perhaps a solution from others who anodize this alloy more frequently than I.
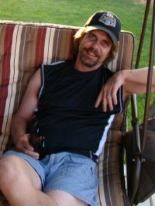
Marc Green
anodizer - Boise, Idaho
Q. I am having a problem with 7075 aluminum blistering after black hard coat anodize. We have run several loads with no problems and all of a sudden the last 2 loads have had blisters. I have checked the parameters of my tank and everything is where it should be. We rack only on Aluminum racks, no titanium. Does anyone have any suggestions?
Paula Stablewski- Batavia, New York, USA
September 12, 2012
Copper particles found between anodize layer and substrate
Q. We have recently run into a huge problem where our customer has found that anodize is coming off of our 7075 aluminum parts after a tape test is performed. We are only a machine shop and send our parts out for MIL-A-8625 class II type I with a dichromate seal.
Our sub has sent out the parts to be tested and the conclusion was that there was copper particles found between the anodize and the substrate. We have confirmed that our customer cleans the parts and then puts them into an oven @ 250 degrees for 2 hours. After baking when they perform a tape test the anodize comes up in small pen point size areas. I'm at a point where I don't know which way to go. My sub is NADCAP approved and all of there routing shows that parts were plated to spec.
We just machine them and have not changed our procedure for 25 years. Never seen this before. Please help
Bobby B- Tampa, Florida
December 5, 2013
![]() |
A. Any thing over 80 °C (176 °F) and the (1) the zinc comes out of alloy into the grain boundaries, and (2) the anodic oxide cracks - this occasionally results in "flaking". Try ramping up slowly for 15 minutes. If that dos not work, there is nothing you can do with this particular batch of 7075, especially at 400 °F or °C. ![]() Robert H Probert Robert H Probert Technical Services ![]() Garner, North Carolina ![]() A. Copper migrates to the surface of the metal with temperatures over 140 °F. Also, the deoxidizer they're using prior to the anodize could have high copper contamination. - Seattle, Washington, USA December 17, 2013 |
Q, A, or Comment on THIS thread -or- Start a NEW Thread
