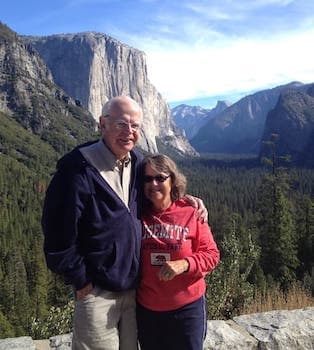
Curated with aloha by
Ted Mooney, P.E. RET
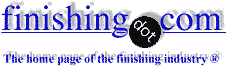
The authoritative public forum
for Metal Finishing 1989-2025
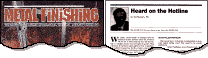
-----
Diffusion of oxygen in silver platings during post-plate heating
My company plates tungsten slugs (various sizes, typically 0.065 inches long by 0.050 inches in diameter) first with electrolytic Ni (say 50 micro-inches thick), then electro plate Ag (say 200 micro-inches thick) over the Ni. We use a brightener in the Ag plating bath that incorporates Sb into the Ag plating layer. We also have several post plate heating processes at temperatures ranging from 850°C to 600°C. After these heating processes we braze a Cu lead (say 0.030 inches in diameter by a inch long) with a Cu/Ag/P braze material at 700°C.
For ten years now we never experience Cu leads breaking off the plated tungsten slugs until now. Years ago (more than 10 years ago) we did make a process change that purposely reduced the concentration of brightener (Sb) in the Ag plating bath, and this did produce some braze failures (Cu leads breaking off the plated tungsten slugs). So we went back to the "old" process and the braze joints did not fail.
The whole point of this story is that I truly believe that during some of our post-plate heating processes there was a air leak and oxygen diffused through the Ag plating and oxidized the Ni plating - and Sb somehow protects the Ni plating by reacting with the oxygen in the furnace. Brazing to the Ag plate is really no problem, but with the NiO present the braze joint is weakened - failing later during a mechanical stress test. I've performed many experiments supporting this theory and Lab results of the braze failures found oxygen between the Ni and Ag platings, but my boss just doesn't believe this could happen.
Does anyone have any words of wisdom that could help me? Perhaps papers demonstrating the ability of oxygen to diffuse through Ag at high temperatures (600-800°C) could help. In the meantime I believe I found and fixed all the gross air leaks in my post-plate heating (furnaces) equipment, and the failure rates seem to be going down significantly. Also, does anyone know of a good method to determine the percent of Sb in Ag plating? I tried ICP, but we get too much variability in the results.
Rowland PhillipsElectronics manufacturer - Santa Ana, California, USA
2004
![]() |
A. Rowland, any protective effect from the incorporation of Sb in your Silver plate could be simply that the tighter grain structure of the brighter finish is less permeable. Wonder if x-ray thickness testing equipment could be used to determine the level of Sb in the plate? Craig HaseltineC&L Equipment Inc - St Charles, Illinois, USA 2004 A. You should be able to determine the amount of Sb in the Ag using X-ray fluorescence. It's a pretty common technique, used in a number of industries, non-destructive and can be very accurate. ![]() Jim Treglio - scwineryreview.com PVD Consultant & Wine Lover San Diego, California 2004 A. Silver is relatively noble and has relatively high solubility and diffusion rates for oxygen. This allows strengthening of some alloys via internal oxidation of alloying elements such as Cr and Mg. As interstitial oxygen diffuses inward faster than substitutional alloying elements diffuse outward, the oxidation occurs internally rather than on the surface. The Ag-0.25%Mg-0.2%Ni alloy is hardened (via internal MgO formation) by heating in air between 650 and 800 C. Hardening time varies as the square of the thickness, from 1 hr for 0.4 mm thick strip to 4 hr for 8 mm (at 745 C). ¯ Metals Handbook, 9th edn., vol. 2, pp. 677-678 (1979). Additional data from Smithells Metals Reference Book, 7th edn.,
(1992): At 1000 K (727 C), D(O in Ag) = 1.43 x 10(-5) while D(Ni in Ag) = 6.69 x 10(-11). Thus, O diffuses 0.21 million times as fast as Ni in Ag. Hence, oxygen can diffuse through the Ag to form NiO as you have observed. Your hypothesis that "oxygen diffused through the Ag plating and oxidized the Ni plating - and Sb somehow protects the Ni plating by reacting with the oxygen" seems very reasonable. Sb dissolved within the Ag intercepts diffusing oxygen, forming internal Sb2O3. To collect and analyze these particles, dissolve the silver within an anode bag. Please inform us of results. Ken Vlach [deceased]- Goleta, California ![]() Rest in peace, Ken. Thank you for your hard work which the finishing world, and we at finishing.com, continue to benefit from. |
I would like to thank you for your helpful advice. Besides NiO formation as a root cause of failure, what are your thoughts on a possible Kirkendall effect between the Ni and Ag plating layers?
Rowland Phillipselectronics manufacturer - Santa Ana, California, USA
2004
Q, A, or Comment on THIS thread -or- Start a NEW Thread