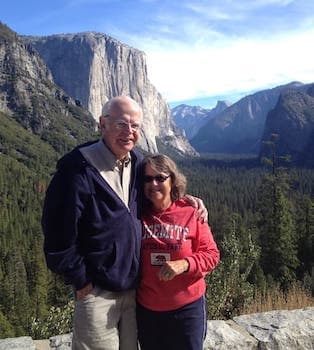
Curated with aloha by
Ted Mooney, P.E. RET
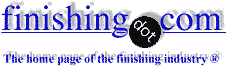
The authoritative public forum
for Metal Finishing 1989-2025
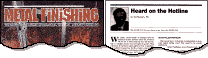
-----
Avoiding waviness on the finished stainless steel surface
I am running a stainless steel fabrication unit in Dubai, UAE. In a handrail project, we are making balusters for the handrail from 2B finished (Cold rolled) 6 mm thick stainless steel sheets. To get mirror finish, we usually grind the surface of the stainless steel balusters first with 220 grit sandpaper then with 320 grit and 400 grit sandpapers. After this, we do cloth buffing with buffing soap. When we polish stainless steel in this way, the surface looks wavy. How can I avoid this waviness. Can anyone help me to get better finish for stainless steel.
Thanks,
Reji JoseStainless steel finishing - Dubai, United Arab Emirates
2004
Can't be 100% sure of where the problem lies. It could be in any of the steps preceding the final buff or the buffing step only. More than likely, you are doing a hand buffing operation. That means that you have the human factor to contend with. Repeatability depends on pressure and the condition of the buffs. In hand buffing, it is possible to create pressure points or variations in either the wheel or the material. This can be amplified by repeated passes or operations and may only be noticeable on the final buff. Automation will eliminate most of these variables.
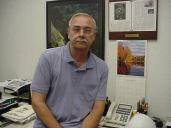
AF Kenton
retired business owner - Hatboro, Pennsylvania
2004
I have seen Mr. Kenton's response to my letter no: 27893. Thanks for your advice. You have mentioned that, automation can solve my problem. Please let me know, how can I automate the grinding and buffing processes. Are there any machines available in the market? If so how can I contact the manufacturer?
Thanks,
Reji JoseStainless steel fabrication - Dubai, UAE
2004
Dear Reji,
If you are using mill finish start from 90 and 120 grit so you achieve proper cut and then flour , jute fibre and final buffing .
Best regards,
Qutub Saify- Ajman, UAE
2004
Most automated buffing systems are designed for a specific or limited range of similar parts because the parts have to be fixtured/positioned tight for the wheels to work properly. meaning, that you will probably have to get a quote for your part system(s). Usually there are 3 to 5 stages involved. We represent one company here in the USA, but I know there are others closer to you in Italy, Germany, and the far east. Anything more specific, get in touch.
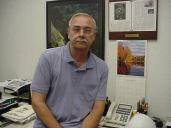
AF Kenton
retired business owner - Hatboro, Pennsylvania
2004
I have been doing mirror finishing for quite some time especially on handrail and never have this problem that you are talking about.I start with a 120grit,then a 240grit,followed by a 320grit as far as sanding goes.I then use a sisal wheel with a black paste,followed by a stitch wheel with green paste and finally a loose mop wheel with a white paste.As I polish I change direction.For example sisal one way,stitch across and loose wheel the same way as sisal. Doing this gets rid of all scratches and streaks if you are really picky.
Dominique KanonikSelf employed - GOLD COAST, QUEENSLAND, AUSTRALIA
2007
Q, A, or Comment on THIS thread -or- Start a NEW Thread