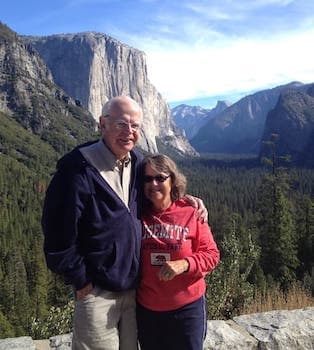
Curated with aloha by
Ted Mooney, P.E. RET
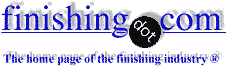
The authoritative public forum
for Metal Finishing 1989-2025
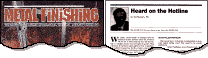
-----
Casting Material Selection
2004
Hi,
I would like to enquire about the selection of the right grade steel for the application we are using . Currently we are using 316c16 for an application that is in a environment using lasers. The pitch of the tapped holes that are present is very fine, i.e., 0.2mm But for some funny reason using this material we are unable to tapping properly cause the taps are breaking continuously. I'm looking for some resource of finding the right material for our application, where we can find out the material hardness and related things also before we try it out as a trial and error approach. We need it to be chemical resistant, corrosion, acid resistant, & it should be stable at various extreme temperatures Please suggest the right way to proceed ahead.
Regards,
Ram MartiDesign Engineer - London, UK
All formulas and tables of properties are idealizations of the real world, hammered into our pigeon holes of prejudice and prior experience--so we will probably never completely eliminate the need for trial and error testing. But I think your starting point should be the ASM Metals Handbook. This is a multi-volume set and you can pick the volumes you most need, probably including "Material Properties and Selection". I didn't look up 316c 16, but it sounds like a work-hardening alloy, and yes, it would therefore be difficult to tap.
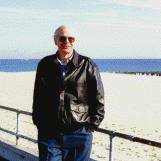
Ted Mooney, P.E.
Striving to live Aloha
finishing.com - Pine Beach, New Jersey
2004
I am guessing that you have a variant of 316 SS, which would be tough rather than hard. It might tap better if it were harder. Two of the nastiest things that I have tapped were lead and copper-both very soft. Your tap is tiny, so will be subject to breaking with any side load at all. You might be able to find a numbered or lettered drill that is a thousands or two larger than the one that you are currently using which would allow a little more clearance on the minor diameter. You might be able to try some other cutting fluids or to reverse the direction more often to have smaller chips.
James Watts- Navarre, Florida
2004
Q, A, or Comment on THIS thread -or- Start a NEW Thread