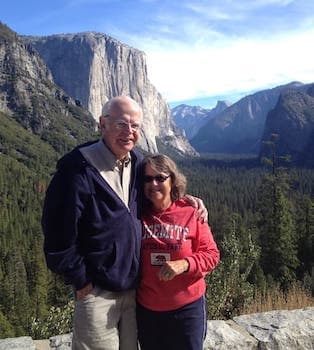
Curated with aloha by
Ted Mooney, P.E. RET
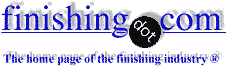
The authoritative public forum
for Metal Finishing 1989-2025
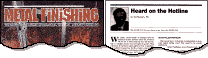
-----
ID burnishing on Hard coat anodizing, before? or after? to achieve RA of 15 max
Q. My company is a distributor or tubing Aluminum extrusion and pipe, and copper and brass.We are in the process of quoting a new project that need a ID surface finish of 15 RA max on an aluminum extrusion, my extruder is having a very tough time figuring out how to achieve this. They have tried honing and burnishing before hardcoat anodizing and they are unable to achieve this finish requirement. I have talked with several other people in the industry and they say to either hone or burnish after hardcoat is this the correct way to go about this or not. Is there any other manufacturing process that would be better for this application.
Mike RohrerQuality Manager - Brookfield, Wisconsin
2004
First of two simultaneous responses --
A. Just be sure the hard coat is not very thick. Be reminded that the anodizing builds VERTICALLY therefore on an inside curve the growth crashes into itself and fractures. Also be aware that if you do any abrasive work before anodizing you will imbed hard abrasives in the soft aluminum and this will somewhat upset the vertical growth of the anodizing.
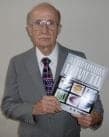
Robert H Probert
Robert H Probert Technical Services

Garner, North Carolina
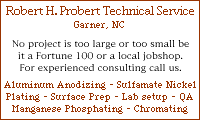
2004
Second of two simultaneous responses --
A. Burnishing is never a good idea for anodized parts. It just moves the metal around and anodizing penetration can expose flaws and make things worse. Honing is the best process for improved surface finish. Before hardcoat is good, after hardcoat is better, and both before and after is best. Finishes as low as 4 RMS are possible.
Chris Jurey, Past-President IHAALuke Engineering & Mfg. Co. Inc.

Wadsworth, Ohio
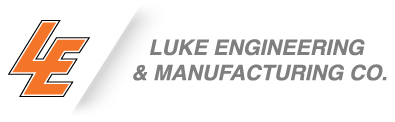
2004
A. Mike,
Typically hard coat anodize will raise the surface finish of anodize 2-1/2 to 3 times the starting RA. First you need to begin with a very low Ra. I have developed a process that will only increase the RA by 1-1/2 times. With a very low starting RA, this process, and some of the other suggestions listed you should not have a problem reaching your requirement.
- Centerville, Georgia, USA
2006
A. Dear Sir,
Please set the parameters (i.e., force, speed , feed, number of passes, lubricant) properly, I am sure you will get required finish.
OR
You can tell me about your tooling and material and I can give you parameters to obtain required finish.
Research - Nasik, India
November 19, 2012
Q. Is there any research article available that correlates the tailoring of hard anodising parameters on surface finish of burnished surfaces?
S Sundararajan- Tamilnadu, INDIA
November 29, 2013
Q, A, or Comment on THIS thread -or- Start a NEW Thread