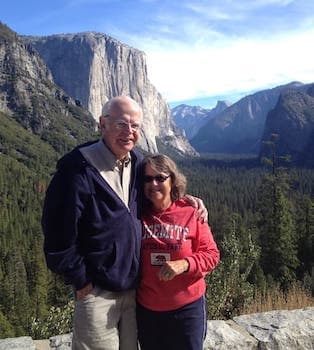
Curated with aloha by
Ted Mooney, P.E. RET
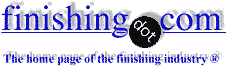
The authoritative public forum
for Metal Finishing 1989-2025
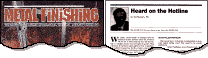
-----
How hard is "Hard Anodizing"
2004
I work within the aerospace industry as a "repair development engineer". My question is "can you provide technical detail how hard is (hard anodizing IAW MIL-A-8625 / MIL-PRF-8625 [⇦ this spec on DLA] Type 3 Class 1 .0004-.0008" thick). The original design calls for a bore to be hard anodized, this bore is showing signs of unacceptable wear and will be restored using a grind-plasma spray-grind process where the Nickel/Aluminum deposit has a UTS figure of around 80,000psi (i.e., equivalent 78 Rockwell "B" on the non ferrous metal scale).
Phil DavisEngineer - Melbourne, Victoria, Australia
2004
Hi Down Yonder.
There has not been much work by the scientist on "hardness", instead they spend most of their time doing abrasion tests for which there is an abundance of data. See Sheasby and Pinner's book.
Rockwell is not used because the substrate is much softer than the aluminum oxide coating and the diamond will punch right through.
When Reynolds Aluminum was developing the Glycolic ACid additive system they did publish some Knoop Hardness numbers which I will copy a few for you here. Hardness has to be measured on the cross section which is why so little data is available. 5052-H14 at 3.2 mils averaged 507 Knoop (load not specified) 6061T6 at 1.7 mils got 506 (all are average of three readings) 3003H14 at 3.2 mils got 645 7075T6 at 2.3mils got 436 2024T3 at 2.3 mils got 347.
Give us some more information and come back again ya heah.
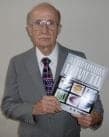
Robert H Probert
Robert H Probert Technical Services

Garner, North Carolina
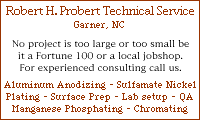
Q, A, or Comment on THIS thread -or- Start a NEW Thread