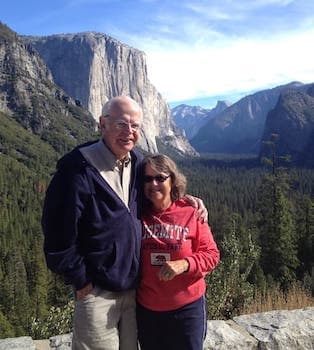
Curated with aloha by
Ted Mooney, P.E. RET
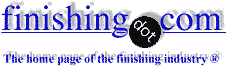
The authoritative public forum
for Metal Finishing 1989-2025
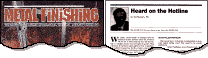
Thread 275/32
Zinc plate/Yellow Chromate appears green in color
Q. We are not a plating company, but take on plating as an added service for our customer. We assemble parts, braze, stamp and send off to the plater. The questions asked by my customer and the answers I get from my plater (which do not satisfy my customer) are driving me up the wall. I am no pro by a long shot, so here is what I need help on.
The customer is complaining the zinc plate yellow chromate appears to be green in color. He belives the platers rinse tanks are not purged of olive drab chromate or the same tank is used for both yellow chromate and olive drab. He believes the yellow chromate parts are picking up green color from one of the plater's tanks. This issue is sporadic. The plater responded that their is nothing wrong with the color of the part. Their yellow chromate has a hue of red, green and gold when applied and dried under heat. The only way the color could be matted is that all parts would need to be oiled after the chromate is applied and dried.
This would then make the part gold all over. They counter flow rinse tanks after almost every solution that they used within their plant. However there is always a small amount of contamination from one tank to the next, but the amount is so small that it would not effect the color of the next batch going in. They say if it was too contaminated or strong it would apply two layers causing the chromate to rub off making bad product. Is what the plater say true. Is there anything he is overlooking or not telling me that could cause what my customer is seeing. Please respond. ASAP
Thanks,
Quality Tech, 1st. Tier Automotive - Coldwater, Michigan
2004
publicly reply to Janet Losinski
A. Hi Janet,
The shade of yellow, red or green is not important to the corrosion protection. The colour difference is normally caused by minute quantities of metal impurities plating out with the zinc. However it is important not to overheat the yellow passivation when drying (not more than 60 degrees C)as this would cause the passivation to brake down and discolour towards brown. It is also not a good idea to oil freshly passivated articles as the passivation has not had a chance to fuse with the zinc properly.
Regards,
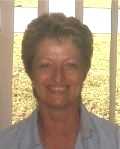
Trudy Kastner
electroplating service - Durban, KZN, South Africa
2004
publicly reply to Trudy Kastner
A. Janet,
Your plater can greatly reduce the colored iridescence, especially the greens and purples by eliminating heat, from the hot water rinse or hot air dryer, to aid in drying the parts. Although this iridescence is an acceptable color per MIL and ASTM specs and as long as the part does not get heated above 140 deg f, which dehydrates the gelatinous structure, thus losing its corrosion protection. Platers use hot water or air to greatly reduce their labor, so asking your plater to eliminate this step may increase your costs. I would suggest enlightening your customer over pushing your plater to change what sounds like an acceptable process. Zinc is not and should never be considered a "cosmetic, decorative finish" but a paint base and base metal corrosion protection.
Good luck,
metal finisher - San Diego, California
2004
publicly reply to Steve Parkhurst
A. Hi Janet,
I have to agree with Trudy and Steve, but I also agree with your plater. First about the green color in the passivation. Green color is in small amounts acceptable, as Steve mentioned. By overheating the passivated surface when drying it, you'll get more red color, but with incorrect passivation, green will always be present. Your plater was correct when he told you about oiling the passivated surface before drying it, but he wasn't speaking about common oiling. Passivated surfaces are being "sealed" with special oils before drying. With this kind of sealing you will get gold colored yellow passivation throughout the surface. This kind of sealing increases the price of the plating.
If you want a normal Zn plating with a common yellow passivation and without too much green color here's the answer. Yellow passivation needs to have pH about 2,0. You can decrease the pH with HCl or HNO3. In the case, when you use HNO3 the color of the passivation will be a little red, but when you use HCl the passivation will get rich with chlorides and the passivation will turn out more green. The correct treatment is a matter of experience. Ask your plater which acid is he using. Don't forget that the temperature
(speed) of drying is very important.
With best regards,
plating - Maribor, Styria, Slovenia
2004
publicly reply to Dimitrije Stopar
A. Dimitrije is right; apart from HCl even an excess of Sulphate in the passivation formulation can turn the passivation green. This can be corrected by asking yr plater to dose with 2-3 ml / lit of HNO3. Regards
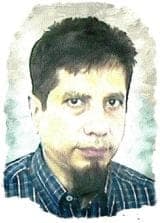
Khozem Vahaanwala
Saify Ind

Bengaluru, Karnataka, India
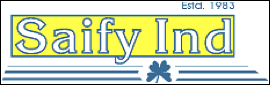
2004
publicly reply to Khozem Vahaanwala
Q. Dear sir,
We are facing problem in yellow passivation in zinc plating.
The color we are getting is green or bluish but customer demands
Golden color. How can we maintain? Please suggest?
Regards,
- India
September 14, 2013
publicly reply to Sanjeev Yadav
A. Hi Sanjeev. Can you offer any feedback on the four suggestions already made before we ask for a 5th? Thanks.
Regards,
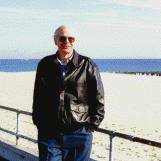
Ted Mooney, P.E.
Striving to live Aloha
finishing.com - Pine Beach, New Jersey
September 17, 2013
publicly reply to Ted Mooney
A. With yellow chromate you can achieve different tonalities, depending on the time, pH, temperature of drying and thickness of deposit (Zn).
example: 10 seconds you may obtain iridescence color with more green .
20 seconds you may obtain iridescence color with more yellow.
more time more yellow.
HCD the tonalities are more yellow with normal parameters ( pH 1.8 - 2.2).
Drying with hot water 100-140 °F max. and not using air or centrifuge hot
is my suggestion based on my experience.
- Tecate, BC, Mexico
publicly reply to Eduardo Lorona
Q, A, or Comment on THIS thread -or- Start a NEW Thread