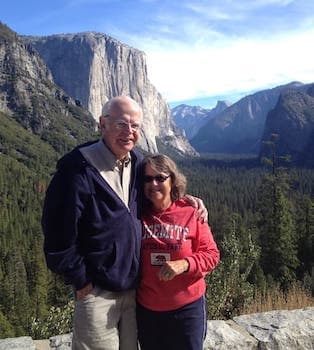
Curated with aloha by
Ted Mooney, P.E. RET
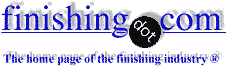
The authoritative public forum
for Metal Finishing 1989-2025
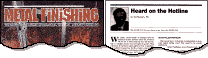
-----
What causes large crystals to form in the anodize tank?
Q. We have recently had problems with our anodizing tanks forming large crystals big enough to clog solid the heat exchangers and the PVC pipes. Some crystals are as large as your fist. I have heard that maybe the aluminum is too high in the anodize tank or that it is caused by phosphates being carried into the anodize tank from the bright dip tank. The crystals form every 1-3 months, and recently our bright dip volume has dropped by 50% and we keep our aluminum content between 10-15. One tank is stainless steel and the other uses lead cathodes. We have checked with our chemical supplier and sent out samples and no answer to the mystery crystals.
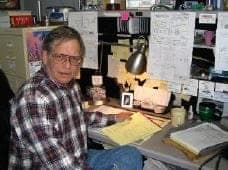
Jeffrey Holmes, CEF
Spartanburg, South Carolina
2004
A. What alloys are your running? What color are the crystals?
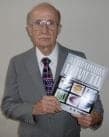
Robert H Probert
Robert H Probert Technical Services

Garner, North Carolina
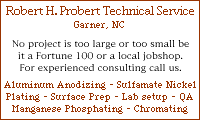
2004
Q. This may or may not be helpful; I have experienced crystals forming on the inside wall of an aluminum tank filled with water, with an SS heat exchanger running through the water bath. The crystals or precipitation comes in dime sized globs and form in over the period of about a week. We don't have any solution for this but since we don't need the water to move, this doesn't pose any problem. Perhaps it is the result of Aluminium and SS components in something that acts as an electrolyte. Hope this helps . . . somehow . . .
Charlie Harland- Ottawa, Ontario, Canada
2004
A. Charlie,
Do you take out cathodes when not in use? Otherwise that could be the reason for the problem, cathodes react with the electrolyte, form the crystals (Aluminum Sulphate?) Check it out.
- Bangalore, Karnataka, India
2004
A. Hi Charlie,
These crystals could be Al2O3 or what we call Aluminum oxide it is very unlikely that it could be aluminum sulphate. If they are Al2O3 they must be very hard #9 on moh scale they should scratch the carbide insert of cutting tools. You can also call them Rubies or Saphires.it could be Red Blue Yellow or White.
Good luck,
toolmaking - Windsor, Ont., Canada
2004
February 9, 2013
Q. Dear Sir,
I am also facing the same problem (formation of crystals in heat exchanger). So far I have been taught that crystal formation is due to increase of aluminum in the bath. Please go through my following points.
1) After formation of new bath the aluminum content is almost 0.
2) With time aluminum content increases in bath.
3) But in my case aluminum content is only 2 gms/ltr even after 20 days of production. But the crystals get formed in the heat exchanger in spite of low aluminum content
4) What is the other reason for formation of crystals?
Please guide me over it. I am having very tough time in solving this problem.
Thanking you in anticipation.
- Ahmednagar, Maharashtra, India
A. Hi,
If you are using a nitric acid based desmut or other nitric acid process before anodizing then the crystals are almost certainly ammonium aluminium sulphate (ammonium alum). Nitric acid acid is carried over to the anodizing bath. It is then reduced at the cathodes to ammonia. The ammonia
⇦ this on
eBay or
Amazon [affil links] reacts with aluminium sulphate to form the alum. This has relatively low solubility and crystalizes in the chiller.
There is a simple test. Wash a crystal to remove surplus acid. Crush it into small pieces. Put the crushed crystal into a suitable container (e.g. test tube or beaker). Add 10% sodium hydroxide solution and raise the temperature to near boiling. If the crystal is ammonium alum, there will be a smell of ammonia. Take appropriate safety precautions.
If nitric acid is the source of your problem, take steps to improve rinsing.
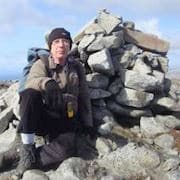
Harry Parkes
- Birmingham, UK
February 19, 2013
February 20, 2013
Dear Mr. Harry,
I don't know how to thank you and this website for giving me the directions. I really appreciate your reply.
You are very much right that I am using nitric desmut before anodizing. And if your thesis is right, you have solved my very big problem.
From last 6 month I was just helpless in front of this problem. My anodizing school taught me that the problem arises only due to increase of aluminium content in bath.
No one ever told me that it is possible due to carry over of nitric acid into the bath.
Q. There is one more query :- Does cleaning of cathodes on regular basis help us out?
No doubt we will have to arrest carryover of nitric acid, but will cleaning of cathodes will also help or not?
Once again, thanks a ton.
- Ahmednagar, Maharashtra, India
A. Hi,
The occurrence of this problem is rare. I have only met it on a few occasions in a career exceeding 40 years.
If you have crystals now, please do the simple analytical check that I recommended and PLEASE let us know the result.
I don't think that cleaning the cathodes will help or is necessary. However if you can see any coating/fouling of the cathodes, then clean them and investigate the cause.
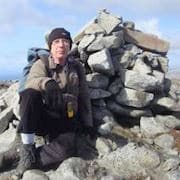
Harry Parkes
- Birmingham, UK
February 21, 2013
![]() |
Q. Would like to know if the crystals anyone is having problems with are an aqua blue.
Refinishing - Upper Marlboro, Maryland August 30, 2016 A. Hi Mara. Are you asking because you can offer a solution, but only if the crystals are aqua blue? :-) Actually, we assume you are experiencing a problem yourself, but you haven't told us what is is :-( I see a bunch of aqua blue crystals, presumably copper sulphate, but I doubt that you are either using that truck bed as an anodizing tank, nor trying to anodize it. Assuming the crystals are copper sulphate, their solubility is extremely temperature dependent; if you let a hot tank with a high concentration of copper sulphate ⇦ this on eBay or Amazon [affil links] dissolved in it cool off, crystals will form. But I still have no idea what your question is :-) Sorry. Regards, ![]() Ted Mooney, P.E. RET Striving to live Aloha finishing.com - Pine Beach, New Jersey August 2016 Q. Thank you sir. This is a stripping & refinishing business and my brother, the engineer, died last year. I am trying to keep the place going, however, my knowledge is lacking. The crystals formed this past winter, and the heater on that tank went out. You definitely answered my question. Can I reverse this formation? Or should we empty and start over? Mara West [returning]- Upper Marlboro, Maryland August 31, 2016 A. Condolences on your brother's passing, Mara. Apparently this actually has nothing to do with anodizing but is an acid-based stripping process? If so, I doubt that the high copper concentration could be beneficial to the stripping operation, so I would remove the crystals that are easily removable, and then reheat the contents of the tank, and see what you have because you don't want to create wastes unless proven necessary. But you really can't operate a processing tank if you don't even know what it is or what's in it or why; you'll have to start with that. Luck and Regards, ![]() Ted Mooney, P.E. RET Striving to live Aloha finishing.com - Pine Beach, New Jersey August 2016 |
November 17, 2017
Q. Hello,
I manage a small parts anodizing department, and we have always had somewhat of an issue with a crystalline buildup on our cathodes as well as between the plates of our heat exchanger. We do type 2 sulfuric anodizing on primarily 6061 aluminum alloy, but also do some 7075 aluminum alloy parts from time to time. I have been unsuccessful in figuring out exactly why these crystals form on my own, so I am turning to this forum for some help!
Our process line looks like this: Soap tank, rinse tank, caustic etch tank, rinse tank, desmut, rinse tank, anodize, rinse tank, rinse tank, rinse tank, dye tank, rinse tank, sealing tank, rinse tank. Parts do get sprayed down with water over each rinse tank to reduce drag-in/drag-out between tanks.
I read previously in this thread that crystal formation in the anodize tank could possibly be caused from nitric acid drag-in from a desmut tank further up the line (suggested by Harry Parkes). This seemed likely to me, as we do have a nitric acid based desmut tank before the anodize tank. I performed his simple test that was suggested involving smelling for ammonia after heating a small amount of crushed crystal and sodium hydroxide solution. Unfortunately I did not detect any ammonia-like smell from the test, so I am unsure if that is the source of the problem.
I have also read in other threads that crystal buildup could possibly be caused by the dissolved aluminum content being too high in the anodize tank, so I have considered that as a possibility, but again, I am unsure. The crystals always seem to show up, even after a fresh sulfuric bath has been put in place at the start of a new season with relatively low aluminum content present.
Here are some pictures of our cathodes, as well as one of the plates in our heat exchanger. It seems these two places are primarily where the crystals tend to form, as well as along the plastic wall of the anodize tank above the surface of the acid. It has never clogged any of our PVC plumbing lines, thankfully.
I hope it is okay to link images in this way (imgur.com), it seemed the easiest solution to me.
----
Ed. note: Yes, readers are welcome to submit their photos via links to imgur.com or similar sites as long as they don't surrender copyright; but we then download the pics and serve them from this site since external links make the page terribly slow especially on smart phones, and because this site is intended as a permanent reference source, and the one thing worse than a broken link is missing pictures :-)
Our cathodes are made from 6061-T6 aluminum flat plate (I believe), bolted together with 316 stainless steel bolts. The cathodes themselves do seem to slowly dissolve over time, but we have only had to replace them once over the past ~5 or 6 years we have had this anodizing setup, due to them becoming pitted. I'm unsure if this is related to the crystal buildup.
The crystal buildup itself has not had any adverse effects on our anodizing quality as far as I can tell. However, it does require us to remove the cathodes and scrape the majority of the crystals off periodically, as I am wary of them building up too much and getting knocked off into the bath when inserting/removing racks from the tank. We also have to disassemble our heat exchanger yearly and clean out crystals from between the plates to restore liquid flow thru the heat exchanger. I'd like to figure out the cause of the crystal buildup so that we may eliminate these two time consuming maintenance duties (especially disassembly/cleaning/reassembly of the heat exchanger!)
Does anyone have any insight into where/why these crystals continue to form? Any help would be appreciated. I think I have given enough relevant information to get a start on our problem, but if more pertinent info is required, please let me know.
Thank you in advance!
- Bozeman, Montana, USA
December 20, 2017
I have the same problem Alex Johnston.
At some point when it gets a lot I pull the plates and scrape off most of it and then wash the rest off.
It's pretty soft and dissolves pretty easily with water.
I'm curious about it too ... have the same basic setup.
- Tomball, Texas, USA
A. Alex, Jeffrey
I believe it is aluminum sulphate. It forms from the droplets of acid that evolve from the anodize process. The acid reacts with the exposed aluminum cathode and forms the salt. It is typically more noticeable on Type II anodize tanks as Type III operates at a much lower temperature and the subsequent condensation of humidity 'washes' the salt off.
- Green Mountain Falls, Colorado
December 21, 2017
Q. Hello,
I have the same condition in my type II anodize tank, I saw the type of cathode in the picture, used for electro cleaning, do you think a cathode for anodize could be made similar to this and in this way keep the aluminum below the solution all the time preventing this salt?
Regards
Aerospace - Chihuahua, Mexico
December 27, 2017
A. We've solved this issue many years ago (on the Al cathodes) by applying an ECTFE coating on all Al surfaces that are continuously exposed to atmosphere.
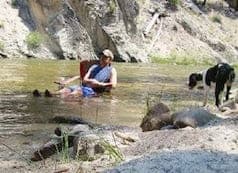
Marc Green
anodizer - Boise, Idaho
December 29, 2017
A. I have had bad experience about your problem 4-5 years ago. Surely,there is nitric acid problem according to your shared pics with heat exchanger plates. Firstly,if I were advising, I would use sulfuric acid + oxidizing agent such as hydrogen peroxide instead of nitric acid. I have used nitric acid as neutralizing bath before anodizing but I saw the same problem whereby all heat exchanger plates were built up by crystalline. So I have been using sulfuric acid+H2O2 based neutralize bath and I never saw same problem again.
If you say it's impossible to use H2SO4 based neutralizing than you should use double rinse after your nitric acid neutralize because one rinse is not enough for this problem.
Secondly, you should not allow aluminium content to reach 20 gr/lt. If you pass this rate, it will be dangerous for heat exchangers. The chemical which creates the problem in heat exchanger is absolutely "aluminium sulphate". Try my advice and you won't see any problem.
Sincerely,
- sakarya,TURKEY
December 31, 2017
Q, A, or Comment on THIS thread -or- Start a NEW Thread