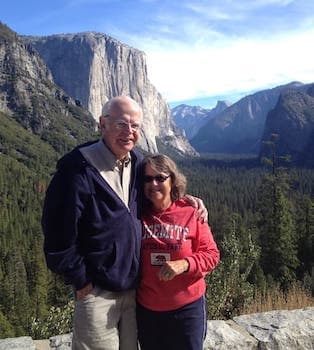
Curated with aloha by
Ted Mooney, P.E. RET
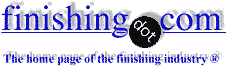
The authoritative public forum
for Metal Finishing 1989-2025
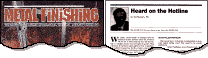
-----
Zinc plating - plating peel off issue
2004
I am working in an Indian starter manufacturing unit. We are having one of our part "Frames" made out of SAE 1006 - made by Cold forging and then Zinc plated and Yellow passivated. The zinc plating is done by "acid zinc plating method" and in this process, the plating thickness depends upon the Current density I mean. The part will look like a barrel with open lid at one end. Half of the other end lid is pierced and removed. A small assembly is coming inside the Frame and then it is crimped. The crimping area is nearer to the open lid side diameter 50mm with a metal thickness of 0.75mm and the plating thickness is 35 microns in this end.The plating thickness at the other end is only 17 microns where the metal thickness is 2.75mm and the diameter is 50mm. Our standard is 15 microns plating thickness minimum in both the ends. Due to this 35 microns thickness in the crimping end; during crimping operation, plating is peeled-off and we get a lot of rejection. How can I get uniform plating thickness through out the length of 50mm of my part? Is there any other way to improve my Plating adhesion property?
Plating process details:
1) plating time: 15mins.
2) current: 2amp/dm2
3) concentration of plating bath: (a) zinc metal 35 - 40 gm/lit, (b) total chloride 120 - 140 gm/lit, (c) boric acid 30-33 gm/lit V S Magesh Chennai - India
Automotive - Chennai, Tamil Nadu, India
![]() |
Dear Mr Magesh, ![]() Khozem Vahaanwala Saify Ind ![]() Bengaluru, Karnataka, India ![]() Alkaline zinc plating gives a better metal distribution, you may wanna try that. Sena KIRAY- Istanbul, TURKEY |
A. Mr Magesh,
Alkaline Zinc is the only way out of your situation, The deposit distribution on a component of the configuration you have described will be around 1: 1.10 in rack plating using alk zinc. Whereas the distribution in acid zinc is very visible from your letter. Good pretreatment. Good activation. Alkaline Zinc. This combination is your solution.
Regards,
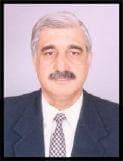
Asif Nurie [deceased] [deceased]
- New Delhi, India
With deep sadness we acknowledge the passing of Asif on Jan 24, 2016
Q, A, or Comment on THIS thread -or- Start a NEW Thread