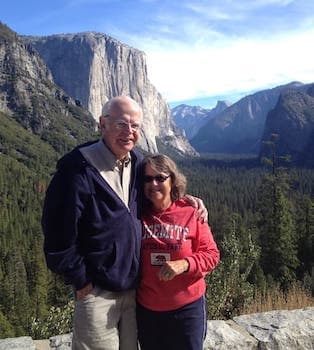
Curated with aloha by
Ted Mooney, P.E. RET
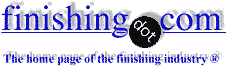
The authoritative public forum
for Metal Finishing 1989-2025
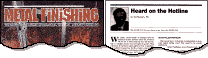
-----
Repairing titanium shafts by plating or hardcoating
Current question and answers:
Q. Greetings.
I hope someone here will be able to help me.
I am trying to figure a way to repair a worn titanium shaft. The bearings failed, and took about 0.5-1mm material of the shaft.
Is there a best suited way to add material back? The shaft is about 1.5 cm in diameter.
Best regards,
- Ljubljana Slovenia
March 5, 2021
A. Given the enormous amount of material lost, the only option I see would be laser welding build-up and re-machining. Too much for anything else. Even though laser is a low heat input process, there is risk of distortion, so, depending on outcome, a final straightening could be necessary.
Guillermo Marrufo- Monterrey Mexico
March 8, 2021
⇩ Related postings, oldest first ⇩
Q. I have a Front Axle for a motorcycle made from Grade 5 Titanium (6-4) with the O.D. dimension too small when machined. It was my fault as I didn't specify a good enough tolerance! I need to bring the overall diameter of the shaft up 0.1mm or 0.004" to match the original stock axle. The wheel's bearings inner race are directly on the shaft and it is a bit too sloppy for me. I have a rear axle and swingarm pivot also made which turned out fine and would like to get Titanium Nitride coating on all three, but need to get front axle size up before coating.
** I was told Ti will not plate (ex: hard chrome, etc.)**
Any other suggestions? Thanks.
- Niagara Falls, ON
2000
A. The best process and maybe the only one is to hard chrome plate and finish grind to size and tolerance.
Steve Ward- Canada
2000
Multiple threads merged: please forgive chronology errors and repetition 🙂
Q. We have a cryogenic application (4 K) of a titanium shaft (TiAlVa64) making oscillating movements (about 2.5 degrees) in a AISI 316 sleeve with a pressure load of 73 N/mm2 without any lubrication except liquid Helium. Although there is a reasonable hardness difference, I wonder if a hardlayer on the titanium shaft is needed to prevent pitting or other wear. A hardchrome layer is impossible to get to the surface due to the TiO2-skin.
Your help would be appreciated very much.
University Twente - Enschede, Holland
2001
A. Aren't the metals (and alloys) already extremely hard and brittle at cryo temperatures? You are nearing absolute zero. A hard coating may not be of use.
Mandar Sunthankar- Fort Collins, Colorado
2001
Repairing titanium shafts by plating or hardcoating
Q. My company is trying to find the best way to plate titanium (6Al-4V). We have a difficult-to-replace transmission shaft that has experienced fretting corrosion on a bearing surface to below acceptable fit limits but within structural limits. Best (only?) solution seems to be applying plating to increase shaft diameter. But typical plating processes apparently can't be used on Titanium. Any recommendations?
Dale Robertsaircraft structures engineer - Grants Pass, Oregon, USA
2004
![]() |
A. I would suggest you look into thermal or plasma spray processes. I know the military has begun using them for similar applications in lieu of chrome plating. ![]() Jim Treglio - scwineryreview.com PVD Consultant & Wine Lover San Diego, California 2004 A. I am pretty confident in saying I do not think titanium can be electrodeposited from aqueous systems. The only way may be to use PVD technology, but if it is for the aircraft industry, I would not be too keen to take this route. ![]() Trevor Crichton R&D practical scientist Chesham, Bucks, UK 2004 |
A. Two titanium plating formulas:
I.
100 gm Ti(OH)2
40 gm HCl
100 gm NH4Cl
1 lit water
pH 4-5, 30-50 C,3-4 A/dm2
II.
38 gm TiCl3
200 ml toluene
800 ml ethyl alcohol
0.02 % pitch(or resin?)
graphite anodes, 21 A/dm2, 18 °C
from ukrainian book L.I.Kadaner:"Galvanostegija" (Electroplating), Kiev 1964
- Cerovski vrh Croatia
A. Would you try chromic or sulfuric anodizing titanium first and then for your build up plating?
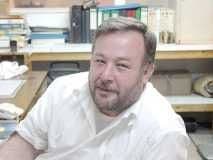
Khair Shishani
aircraft maintenance - Al Ain, UAE
2004
A. Dale,
Plating with EN or electrolytic plating can be more successful and better for the adhesion than with PVD. The adhesion for the PVD is only 30 Mpa/mm2 but with plating type EN you can get over 90 Mpa/mm2.
Regards,
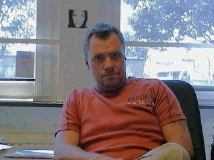
Anders Sundman
4th Generation Surface Engineering
Consultant - Arvika,
Sweden
2004
A. Electrospark deposition is a method of repairing metal in a specific area and is well-suited to small repairs. Most metals can be applied to electrically conductive surfaces in layers .001" and up. There is very little heat put into the part and resulting surface repair is metallurgically bonded to the substrate. There are a handful of companies that produce the equipment and/or provide repair services.
Amy Harmon Krtanjek- Seven Valleys, Pennsylvania
2004
Aluminum and Titanium Coating options
August 11, 2009Q. Hello,
I have two separate coating questions and was hoping for some wisdom. I have very limited knowledge of finishing/coating beyond simple anodizing.
ALUMINUM
This application has a few aluminum components that are exposed to salt water (submerged). Raw aluminum quickly corrodes. Black hard anodize provides a protective barrier, but it scratches off relatively easily and still permits corrosion. What are my other options for coating the aluminum that are more corrosion resistant? One of these parts has a 10-32 tapped thread, so the coating must be applied over the threads without gumming them up (uniform thin thickness). I've used "Feather Shaft", a ceramic coated aluminum shaft distributed by Pacific Bearing and this type of coating seems particularly good, so I was wondering if there is something like that which may be readily available as a commercial coating option.
TITANIUM
I have a titanium shaft, being used for its strength and weight that runs on Vesconite bushings. Although Ti is a great choice for the above mentioned reasons, it's a lousy bearing surface. What kind of coatings are available that are hard, wear resistant, low friction, and can be held to tight tolerances?
Thanks!
Mechanical Engineer - Manchester, New Hampshire
A. High phos electroless nickel sounds like the most appropriate coating to be used for all of your processes. These require professional plating shops and not slop shops if you want less grief from your customers.
James Watts- Navarre, Florida
August 13, 2009
A. Titanium anodize type II is for prevention of "cold welding". It creates only few microns film on the surface, which is also wear resistant.
adv.
Contact us for more information.
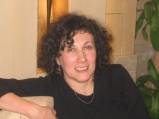
Anna Berkovich
Russamer Lab

Pittsburgh, Pennsylvania
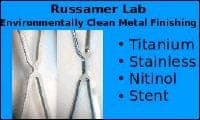
August 24, 2009
Q, A, or Comment on THIS thread -or- Start a NEW Thread