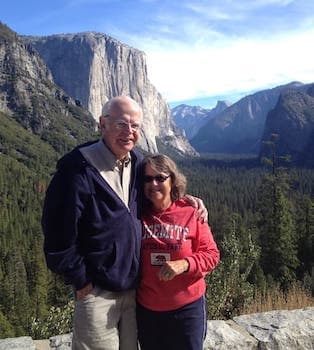
Curated with aloha by
Ted Mooney, P.E. RET
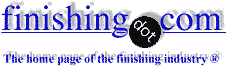
The authoritative public forum
for Metal Finishing 1989-2025
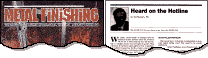
-----
Anodize Cracking Due to Ultrasonic Caustic Cleaning?
Quickstart (no readers left behind):
Readers who are not clear on what anodizing is about may wish to start with our one-page "Intro to Anodizing".
Alkaline cleaners can be damaging to aluminum and particularly to anodized aluminum.
Although ultrasonics can sometimes be successfully used on anodized aluminum, they can also sometimes damage it. Read on ...
[editor appended this entry to this thread which already addresses it in lieu of spawning a duplicative thread]
Q. Good morning, all.
I am wondering what is the effectiveness (in people's experiences) of ultrasonic rinsing after anodizing and before dyeing in removing solution from dead holes?
For context, we have manifolds that have many dead holes, but also get dyed after anodizing, and rinsing them with a hose is, at best, a hit-or-miss proposition in removing sulfuric solution from those holes prior to the dye step. Even when successful, it is EXTREMELY time-consuming, and often it is both time consuming AND ineffective, which is the worst possible combination of outcomes. Just wondering if ultrasonic rinsing is effective as an application here. Just as a jumping off point, we are talking about type II, and the average dead hole size is slightly smaller that the diameter of a standard no. 2 pencil.
I understand there is a ton of variability here WRT the depth of the holes, coating thickness, etc., I really am just wondering what people's anecdotal experience with ultrasonic rinsing at this step has been.
PE - Illinois
February 17, 2025
Tip: This forum was established to build camaraderie among enthusiasts through sharing tips, opinions, pics & personality.
The curator & some readers who publicly share their info will be less likely to engage with those who don't.
A. Hi Matthew,
I think there is little doubt that ultrasonic rinsing will be helpful, and if that rinse is dilute nitric acid (some say as thin as 0.25%, some say as thick as 1-2%) it will be even more helpful.
But an important issue is that ultrasonic agitation can sometimes damage the anodizing. In order to not do so it needs to be the proper frequency, intensity, and duration.
I think the manufacturers of the ultrasonic transducers or tanks will be a big help ⇨
Some users suggest an extra check on this by simply putting a piece of aluminum foil in the tank and seeing what happens. You can read additional perspectives by searching the site for "aluminum anodize ultrasonic".
Luck & Regards,
Ted Mooney, P.E. RET
Striving to live Aloha
finishing.com - Pine Beach, New Jersey
⇩ Related postings, oldest first ⇩
Q. I have several AL 7075 parts of different shapes and sizes coated with a clear anodize 20 microns thick. After receiving the parts, tape tests were done to check if the coatings appeared good. All of the parts seemed fine and then were cleaned in an ultrasonic bath of isopropyl alcohol and alkaline degreaser(Deconex). After integrating several of the parts, a piece of tape would remove the coatings on some parts but not others. It appears to be random which parts the coating is easily removed. Some parts that are identical have variation with the coatings. These parts have been at room temperature since being coated. Looking under a microscope the coating appears to be cracking. Any clues as to why this is happening or what I can do to find out?
Paul Oppenheimermechanical engineer - Washington, DC, USA
2004
![]() |
A. Paul. Your alkaline cleaner is removing the coating. Can you just use the alcohol cleaner? Tape tests are not used on anodizing. Anodizing converts the aluminum surface into an oxide. There is no plating involved. Robert HenryBrooklyn, New York A. You should never use an alkaline cleaner on an anodized part. James Watts- Navarre, Florida |
![]() |
A. If the metal had been blasted (bead, sand, and grit), and/or bent or hammered so that the surface was "work hardened" then the anodizing would likely flake off. If very thin parts were anodized, like in your case where you are going to a thickness of 0.0008, well 1/2 of that or 0.0004 ![]() Aluminum How-To "Chromating - Anodizing - Hardcoating" by Robert Probert Also available in Spanish You'll love this book. Finishing.com has sold almost a thousand copies without a single return request :-) is "in" the metal (under the original surface), then if 0.0004 is close enough to the other side the anodizing would crack on occasion. The aluminum oxide is hard and brittle, the base metal is soft and malleable. If you started with clad material and anodized all the way thru the clad, then something will flake off. Come back with more information and let's have another go at it, ![]() Robert H Probert Robert H Probert Technical Services ![]() Garner, North Carolina ![]()
- Washington, DC |
A. In the semiconductor industry, Ultrasonic cleaning has been shown to affect/damage the anodic coating. As far as your coating flaking off, my bet would be a poor coating due to overheating of the part/area during the anodizing process (I've seen this frequently on 7075 alloy).
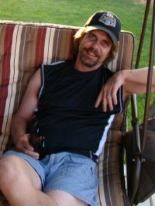
Marc Green
anodizer - Boise, Idaho
for Shops, Specifiers & Engineers
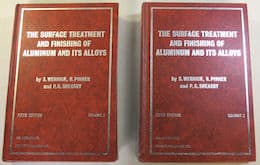
avail from eBay, AbeBooks, or Amazon
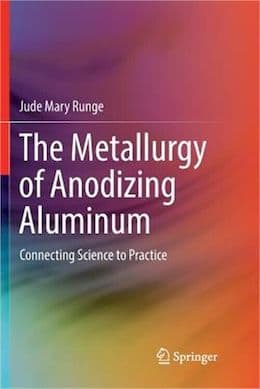
avail from eBay, AbeBooks, or Amazon
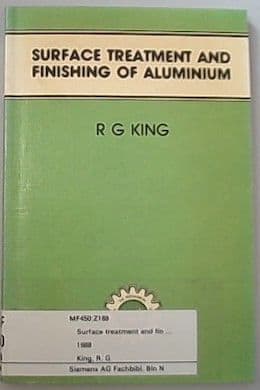
avail from eBay, AbeBooks, or Amazon
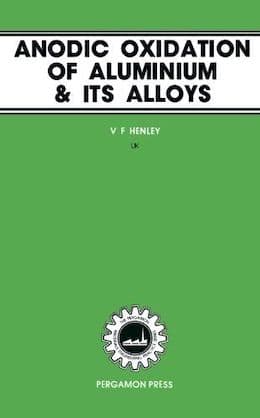
avail from eBay, AbeBooks, or Amazon
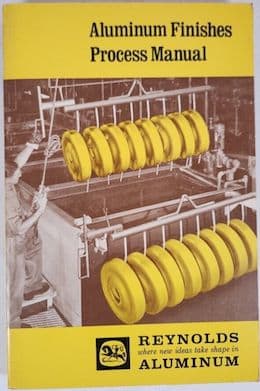
avail from eBay, AbeBooks or Amazon
(as an Amazon Associate & eBay Partner, we earn from qualifying purchases)
A. The anodizing was defective; the cleaning and tape test (apropos in this case) merely led to its early detection. Possible causes and contributing factors:
Overheating due to insufficient cooling during anodizing. Alumina formation creates 1670 kJ/mol, plus resistance heating occurs as the anodize current passes through the film. Normally noticeable from a powdery appearance, the overheating can result in disintegration of the oxide-metal interface.
Sharp edges and inside corners. Anodizing grows vertically into and outward from a surface. At an edge, the 2 growth interfaces intersect at a right angle and the corner gets starved (and this is the area of fastest dissolution, too). At inside corners, the outwardly growing surfaces intersect, resulting in a line of defects. This is the reason that greater radii of curvature are required with increasing anodize thickness per MIL-A-8625 / MIL-PRF-8625
[⇦ this spec on DLA]F and ALCOA studies; see photos in The Surface Treatment and Finishing of Aluminum and its Alloys, 6th Edn., vol. 2, p. 787-788 (2001). For a 20 micron (0.78 mil) anodize thickness, a radius of curvature of at least 0.64 millimeter (0.025 inch) is required.
Anodize cracking known as crazing can occur due to temperature change, as the anodic coating has a lower thermal expansion coefficient than the Al alloy. Common if hard anodize formed at 0 °C is sealed or otherwise heated. Visible with a stereo microscope at 20X magnification.
A contributing factor is very limited ductility in age- and work-hardened Al alloys. In one case, where T6 temper material with very sharp edges had been hard anodized and then subjected to a 15
5 °F thermal shock, an interfacial stress of about 70,000 psi contributed to flaking off of the anodize. Were any parts examined prior to cleaning? What was the anodizing specification, and were the parts sealed or subjected to a hot rinse? The following portion of MIL-A-8625F was not met: "3.13 Workmanship. Except for touch up areas in accordance with 3.3.4 and as noted below, the applied anodic coating shall be continuous, smooth, adherent, uniform in appearance, free from powdery areas, loose films, breaks, scratches and other defects which will reduce the serviceability of anodized parts or assembles."
- Goleta, California

Rest in peace, Ken. Thank you for your hard work which the finishing world, and we at finishing.com, continue to benefit from.
Multiple threads merged: please forgive chronology errors and repetition 🙂
Hard anodize is washing off
Q. We have 6061-T6 and 7075-T6 parts that are anodized to MIL-A-8625 / MIL-PRF-8625 [⇦ this spec on DLA]-f, type iii, class 2 black. When we put them through a bath of brulin 815gd, the anodize is coming off, flaking, bubbling, etc. It doesn't happen on all the parts, but most of them. We have already had one set chem etched to remove the previous anodize and had them redone. They changed all the material in the anodize tank and started again. Still getting same results. Is the ultrasonic cleaning with brulin 815gd messing up the anodize?
Wade Mayengineer - Hampton, Virginia
February 22, 2008
A. While the technical data sheet for this product indicates that it's safe for aluminum, your results would make me question that statement. Seeing that the pH listed on the MSDS is 11.7 - 12.5, that level of alkalinity is extreme enough to give me concern with aluminum, much less anodized aluminum. Furthermore, the data sheet makes reference to the pH falling with continued use to the point where if < 9, there can be corrosion. Certainly the etching you've experienced could be construed as "corrosion." Lastly, do you see black dye coming out of parts rather quickly upon initial immersion? If that is the case, your parts may not be being properly sealed. The mil spec governing Type III hardcoat anodizing contains a requirement that "unless otherwise specified, Type III coatings shall be unsealed." As this leads to fading dyed parts and reduced protection, we've always interpreted this requirement as requiring sealing if the parts specify dyed. ASTM B136 is a simple test for sealing integrity.
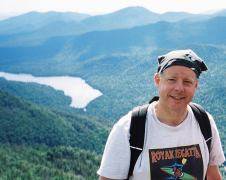
Milt Stevenson, Jr.
Syracuse, New York
Q. Hello,
I have a question regarding red and black anodize flaking.
We are currently sending parts for anodizing (Aluminum 2024-T4 per MIL-A-8625F, TYPE II, Class 2.)
Once we receive the part from anodizing, we clean them using the Ultrasonic cleaner preparing the surface for the bonding process. After applying the bonding material, we oven cure the parts and then during wiring process, the parts are placed once again thru the Ultrasonic Cleaner.
After reading the previous responses, I do understand that ultrasonic can be a possible cause of the flaking problem we are seeing. However, We have tried several different batches of the parts that we get from anodizing and some batches go thru the process mentioned above and Flaking does not occur and on some batches the flaking occurs.
Thank you in advance for any advise or feedback anyone can provide regarding this.
- IRVINE, California, USA
July 6, 2012
A. Hi Asutosh,
I see a couple of possibilities that may be giving you problems.
Firstly, you are right that the ultrasonic cleaning may well be giving you a problem. Knowing that if you use the wrong frequencies that you can actually "punch" holes through thin aluminum sections, it would be no surprise to learn that the ultrasonics are contributing to a damaged anodise layer.
The other thing that may be contributory is your bonding process. What is the curing cycle? Remember that aluminum has approximately 5 times the co-efficient of thermal expansion of aluminum oxide. If you have a long high temperature curing cycle the aluminum will expand at 5 times the rate of the coating. This may not actually cause flaking, but may cause cracking of the coating. The subsequent ultrasonic clean now has even more chance of flaking the anodising off.
Aerospace - Yeovil, Somerset, UK

Q, A, or Comment on THIS thread -or- Start a NEW Thread