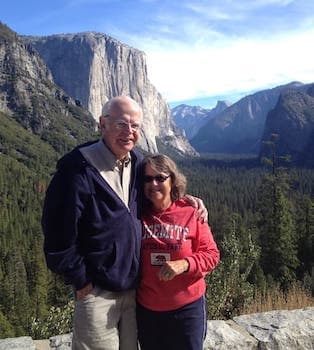
Curated with aloha by
Ted Mooney, P.E. RET
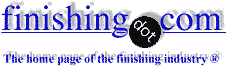
The authoritative public forum
for Metal Finishing 1989-2025
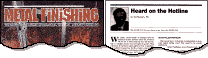
-----
Polishing & anodizing cast aluminum
Q. We are looking at what kind of cast aluminium alloy(s) will give the best effect when polishing? Are there any safe chemicals that could be used to improve the polishing result.
We would like to anodize die cast and gravity cast aluminium components. What kind of alloys are preferred? Any limitations compared to extruded aluminium parts?
Engineer - Stockholm, Stockholm, Sweden
2004
A. You only anodize aluminum. Die Cast is loaded with silicon and copper. You do not anodize silicon and copper. Stay out of the alkaline etch which increases the area of silicon and copper on the surface and decreases the area of aluminum on the surface. Use a cook book formulation of Nitric Acid and Ammonium Bifluoride (50% Nitric + 1 Pound/gallon Ammonium Bifluoride) which will decrease the area of silicon on the surface and increase the area of aluminum on the surface. Be aware that thin walls in die cast cool faster than thick walls and therefore have more silicon in the surface.
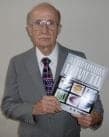
Robert H Probert
Robert H Probert Technical Services

Garner, North Carolina
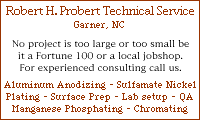
Q. Thank you for your answer. This means that if we use die casting/gravity casting of an almost pure aluminum alloy there is no problem to anodize. The problem will instead be the casting process of almost pure aluminum.
Thomas Olsson [returning]- Stockholm, Sweden
A. Dear Olsson, never be afraid of casting. Select lowest Si and Cu content alloy and follow the sequences below.
1- mass or vibratory polishing. First abrasive and then shot peening. Use appropriate media for cleaning.
2- immediately anodize with low CD and limited time in order to not anodize other elementa except aluminum.
3- follow with dyeing or E-coloring and sealing at last.
- tehran iran
Q, A, or Comment on THIS thread -or- Start a NEW Thread