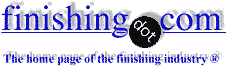
-----
Silver Plating Problem: Low Brightness, Burning
Quickstart: Discoloration of silver solution & silver deposit may be caused by pH out of range but readers are warned that pH can't be safely lowered. Organics not removable by cold continuous carbon treatment or high carbonates are the chief suspects. Other possibilities are selenium contamination if significantly over about 5 ppm, or nickel contamination. Remember to do any experimentation on small volumes, not the whole bath.
Q. We are a decorative silver plating shop servicing the Hotel banquet-ware industry. We use a type III cyanide silver solution with an organic brightener system. The bath is 750 gallons, We use continuous filtration through a 1 micron bag filter at 60 gpm. We Carbon treat the solution 8 hrs. every two weeks. The solution is 5 years old with the following concentrations:
Silver metal 4.3 oz/gal [ed. notes: 32 g/l]
Free Sodium cyanide 10.5 oz/gal [78.5 g/l]
Sodium_carbonate 8.5 oz/gal [63.5 g/l]
Operating temp 72 °F
Issue- The bath has turned a dark brown in color, the brightness has dropped, the tendency to burn has increased (when we add cyanide the burning increases). We have tried micro-filtration in the lab to clear up the solution (supplier says it is carbon dust) but that did not clear it up.
- San Diego, California, USA
2004
![]() |
A. Steve, ![]() Pat Mentone St Paul, Minnesota A. Hello Steve, ![]() Praveen Kumar plating process supplier Mumbai, India |
Q. Thanks Guys,
I am on my way to check the pH, As far as hull cells go, we have run 100's.We are running them at 1 amp for 10 min. Adding cyanide blows out the top end, and it requires a 5x make-up addition of brightener to clean up 50% of the of the panel(high end). The only way to get a good panel is to cut the sample by at least 50%, add back the silver and cyanide and bring in a ton of brightener. We have tried many techniques in the lab to try and filter out the "Dark Color" but I believe the solution to be free of particulate. We are in the process of freezing out some carbonate to see if that improves performance and or color.
I appreciate the responses and look forward to any more suggestions.
Metal Finishing - San Diego, California
A. Hi,
If cutting the bath then adding back the essentials significantly improves things, that is strong evidence that the bath is contaminated and that the cutting reduced the concentration of the contamination. However, I do not have enough experience in this to offer good guesses of what the contaminant is.
Luck & Regards,
Ted Mooney, P.E.
Striving to live Aloha
finishing.com - Pine Beach, New Jersey
A. It would be nice to save this big old $25,000 workhorse.
Here's a few more ideas:
1) What have you been using to treat your carbonates? If you use nitrates, a 5 year build up might be the problem. I know of no way to remove nitrates other than dilution, with subsequent build up of the other ingredients. You might try some Hull cell panels, using some dilution and additions.
If you use hydroxides, accurately test the pH. Use closely bracketing pH standards. I found an interesting page in an old British analysis book, concerning the Hull cell testing of conventional silver cyanide solutions that were similar to your formulation. The make-up pH was 11.5. At a pH of 13, the Hull cell showed rough, burnt deposits, over most of the panel. I know of no way of lowering the pH without killing everybody. Maybe someone else could give us a safe way of doing this. Maybe some sort of simple electrodialysis membrane could be used safely. To see if the pH is the problem, you might adjust a sample to pH 11.5, UNDER A FUME HOOD, with some sort of compatible acid - if there is any. Heat the solution up a little and stir for a few hours, in order to drive off the dissolved HCN. Cool and perform Hull cell tests under the hood.
2) I've suspected all along that your problem is organic breakdown products from 5 years of brightener additions and from such things as rack coatings. The dark color seems to be the key. I never believed in the "carbon dust" theory. I assume, since you are measuring your "carbon treatment" in hours, that you are either packing a filter with carbon or using carbon cartridges. This may not be enough. As I understand it, carbon filters only pick up short-chain organics and leave the longer-chain varieties behind. These build up and can eventually ruin the deposit, in various ways. You may need more power in your organics removal.
The only way to fix your bath may be a traditional, hot, peroxide, carbon treatment. Carbon treating precious metals baths is only done as a last resort, because about 10% of the silver or gold gets hung up with the carbon and must be sent out for refining. Try it on, say, 1000 mL samples in the lab, first. Make the first trial a little strong, just to see if it works. You might:
A) Heat 1000 mL of analyzed solution to 120 deg F.
B) With stirring, add about 3-5 mL of 30% (100 volume) hydrogen peroxide. Check the temperature.
C) Maintain temperature at 120 and stir for 1 hr.
D) Add about 2.5 grams of powdered activated carbon.
E) Stir and maintain temp. for 1 hour, or more.
F) With stirring, add about a gram of filter aid. Diatomaceous earth works OK.
G) Cool and filter well
H) Analyze and adjust silver and cyanide. Analyze carbonates and compare. Analyze brighteners, if you can.
I) Run Hull cell panels and adjust brightener(s).
J) If this works, repeat with more or less temperatures, concentrations, and times, if you wish. The more heat and peroxide, the more cyanide will break down to carbonates. The more carbon you use, the more silver it will adsorb.
If this works and, if you decide to go full scale, you have to do it right. You HAVE to do it in a separate treatment tank. The treatment tank should be located away from the plating tank, since even traces of the easily airborne carbon dust in the plating tank can cause roughness problems, sometimes long term. After treating, the filter must remove all traces of carbon before the solution is returned to the plating tank. To make filtering easier, let everything settle overnight and then start filtering near the top. Make sure everything is ready before you start.
According to one of my books, the chilling out of sodium carbonate, at 3 °C, won't lower it below 8 oz/gal. You're only at 8.5 now - why go to the expense?. Did you prove this in the Hull cell? If you can afford it (and, find it), barium cyanide is the best way to remove carbonates. Maybe you'll find it's time to retire the old gal.
- Houston, Texas
by T.V. Harper
(classic reprint of an old book)
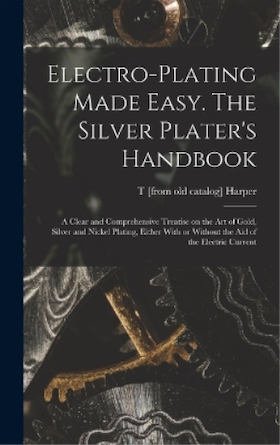
on AbeBooks
or eBay
or Amazon
(affil link)
Q. Chris,
I really appreciate you taking the time to give such a detailed answer.The pH issue seems to be of debate. Pat had recommended raising the pH over 12 where as your info is to lower to 11.5. The pH of the solution is @ 12.7. Raising it from there did not alter the Hull cell. It seems to me that it may be possible to safely lower the PH with Sulfamic or sulfonic acid. Has anyone tried this?
As for dilution, That, of course, improves the panel but not the color. Working with such a large volume makes any treatment very costly. After the peroxide, carbon treatment, we are able to filter out the "Dark Color". Ending color is a fairly bright orange, not the straw color I would have expected to see. Has anyone heard of "bad" cyanide turning the solution orange? Anyway, even after the peroxide treatment and the color lightening up, the Hull cell panels still did not improve to much degree. Still burning half the panel at .5 amps.
In talking with my brightener supplier, They now tell me that the "organic" brightener system has Selenium in it. Could it be that the selenium has built up to a very high level and is the bad guy ? I am getting very discouraged with my suppliers tech support. Feel like I am on an island.
We will keep chuggin' along...the great thing about plating is you never stop learning...
Thank you all for any and all of your advice.
Metal Finishing - San Diego, California
![]() |
A. Steve P, hard chrome plating - Cheshire, UK A. Stephen, - Houston, Texas |
? Steve,
I have a couple of questions. What are you using for anodes? Are you using steel anode baskets? Are you using a silver strike before this bath? any possibility of dragging in contamination from your strike bath?
A. The pH is certainly high enough now, but was it ever lower than 11? If it was lower and you used steel anode baskets then possibly the black color is ferricyanide.
I also agree there is no safe way to lower the pH.
As for selenium, it is a common brightener for silver is effective at concentrations of less than 5 ppm. Your supplier should be able to do a selenium analysis and give you a recommendation if it is too high or too low.
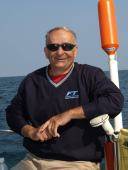
Pat Mentone
St Paul, Minnesota
Q. Thanks all for your continued support, Some added info, The pH has never been below 12, Part of our Air Quality permitting requires this and it is monitored on a weekly basis. In lab tests lowering the carbonate with calcium nitrate did eliminate a lot of the burning but did not clear up the color. Also, with any addition of brightener the burning returns. An interesting observation; The silver anode is polarizing in the hull cell and sloughing off black "stuff".Conductivity of the solution seems very poor. We use silver bits in a PVC anode basket (titanium contacts) in our tank, I am thinking the dark color may be from the anodes (although they are bagged). I will be examining this next. Our supplier is one you all have heard of but has not seen our scenario before and would prefer us to replace the bath.
Thanks Again,
Steve P [surname deleted for privacy by Editor]Metal Finishing - San Diego, California
2004
Q. Please let me know your findings we have a silver E bath with the same problem. Cannot seem to figure it out.
I agree also with you about tech support, getting a lot of different answers. Please let me know of findings.
- St. Pete, Florida
2005
Q. Steve,
Just read your postings, seems like you have been having the same problem I have just inherited. I work for a company that uses a silver cyanide bath (E-type) but I will not say the manufacturer of the bath. I just got the plating shop as part of my duties and have the same kind of problem. The silver bath is a dark orange color and the plating is coming out a very satin off-white. There is a strong brown tint to the plating.
I have been running hull cells' adding the (E) brightener to the solution. As I add the brightener to the bath, the plating seems to burn (black coating) on the low density areas at normal plating amperage. I have to plate at 1/2 the amp hours I normally do. I have been getting around this by adding silver cyanide and Potassium cyanide to the bath. It helps a little but I'm loosing ground quickly. Our pH is 11.73
Please let me know your problem works out and how you solve the problem.
- Sacramento, California, USA
March 11, 2008
A. Hello.
I have not read all the answers in here, but the concentration of carbonate is way too high. You have to freeze the carbs out of the bath, lowering the temperature to below 40 °F. The carbs will then crystallize and you can filter the liquids out. Adjust the cyanide concentration and you are way to go again :)
- Trondheim, Norway
April 11, 2011
A. DEAR SIR,
I HAVE GONE THROUGH THE TOTAL CONVERSATION, AND COME TO CONCLUSION THAT THIS IS NOT ISSUE OF ANY pH, BUT THIS IS PROBLEM OF HIGH ORGANIC CONTAMINATION IN SILVER BATH.
PLEASE DO HEAVY ACTIVATED CHARCOAL HOT TREATMENT AT 90 °C WITH MIN. OF 30-50 GM/LTR STIR WELL FOR 12 HOURS.
KEEP FOR SETTLING 24-48 HOURS. FILTER THE SOLUTION, MAINTAIN THE CARBONATE CONTENT BELLOW 40 G/L. ADD BEST QUALITY OF SILVER BRIGHTENERS A&B AGAIN AS MAKE-UP A- 25 ML AND B- 15 ML. MIX IT FOR 12 HOURS AND TAKE HULL CELL FOR 1 AMP WITH GOOD MIXING, YOU WILL GET 100% CLEAR & BRILLIANT BRIGHT & WHITE SILVER PLATING END TO END.
TRY THIS AND REPLY.
silver brightener manufacturer - AHMEDABAD, GUJARAT, India
April 15, 2015
A. We have seen the silver cyanide solution turn dark orange if the solution is contaminated with nickel. The nickel contamination will also tone down the brilliance of the silver plated deposit.
Michael Brouillard- Indianapolis, Indiana, USA
July 20, 2016
A. We have been using a 5-gal silver cyanide tank with Silverex III brighteners for 30 years and have had the solution turn dark several times when the pH dropped below 12. We remedied this each time with treating a portion of the tank with barium hydroxide to drop some of the carbonate buildup and raise the PH at the same time. The Ba(OH)2 must be kept tightly sealed in storage not to clump into a rock. I used an old titanium tank heater and a 3-gal stainless steel pot to carefully mash the Ba(OH)2 crystals to get them to dissolve and let sit overnight. Pour the clear top liquid back into the tank and filter the rest before adding. Rinse the BaCO3 cake in the filer with DI water spray bottle and let sit a day. Destroy cyanide contaminated BaCO3 by adding it to a pot with a gallon of tap water and add chlorine bleach ⇦ bleach/sodium hypochlorite in bulk on eBay or Amazon [affil links] under a fume hood until a green, blue or brown color (of metallic ferrocyanides) and dispose of BaCO3 as solid waste after filtering again.
Ronald GrafShop owner - Claymont, Delaware, USA
October 7, 2021
Q, A, or Comment on THIS thread -or- Start a NEW Thread