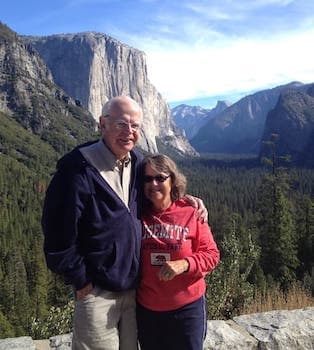
Curated with aloha by
Ted Mooney, P.E. RET
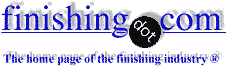
The authoritative public forum
for Metal Finishing 1989-2025
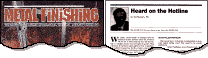
-----
Peeling of zinc in continuous hot dip galvanizing processes
Q. We producing GI wire of sizes from 2.60mm to 3.90 mm. We facing problem on zinc coating, when we make gabion box or making springs for gabion box coating on wire is cracked how can we get proper coating please suggest us
Carbon content in ms wire is 1008.
Thank you,
Elite wires pvt. Ltd.
- Hetauda, Nepal
October 24, 2021
A. Hi Nurlah. May we assume that you mean hot dip galvanized wire, not electrogalvanized (zinc electroplated)? In either case, can you give us the thickness of the zinc, and the galvanizing or electroplating specification if any? Carbon content is '1008' -- that means 0.1008% carbon, not type 1008 steel? Finally, is this process something that you have been doing for a long time and this problem suddenly came up, or is this a startup operation and you have not yet achieved success? If so, have you tried buying a bit of a competitor's wire and forming it for your gabion boxes and springs? Can we get photos to better understand what you mean by cracking? Thanks!
Luck & Regards,
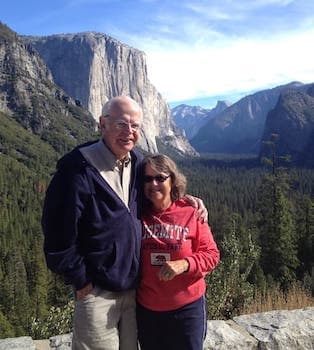
Ted Mooney, P.E. RET
Striving to live Aloha
finishing.com - Pine Beach, New Jersey
October 2021
⇩ Related postings, oldest first ⇩
Q. We are manufacturer of Chain link Fencing from Galvanized wire. During the course of forming of wire, zinc peels off from the bend, can you suggest a means to overcome the peeling of zinc.
Mohammadi Daud- Karachi, PAKISTAN
2002
A. Hi, Mohammadi. It is hard to be specific from this distance and with limited information, but it sounds like the wire may not have been properly cleaned and fluxed. Give us more data if you can please, and read the other comments here for food for thought.
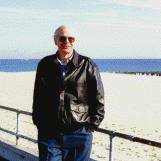
Ted Mooney, P.E.
Striving to live Aloha
finishing.com - Pine Beach, New Jersey
2002
Q. We face problem of Zinc coating peeling in hot dip anodizing of Cable Armour wire. If we increase the Silicon content to improve the adhesion, the resistivity of the wire goes higher than specified. Hence we have to use Silicon lower than 0.05 %. Is there any other way to improve Adhesion of Zinc Coating ?
Sudhir JoshiTata Iron and Steel Co. - Mumbai, Maharashtra, India
2003
Q. We face a problem of zinc peeling in our CGL (continuous galvanizing line) hot dip with non oxidizing vertical furnace and horizontal radiant tube furnace. We checked the O2 ppm in the radiant tube furnace it was 5 ppm; checked the pot composition and it was ideal. We checked the furnace for leaking, it was not leaking. Anyone have any idea for the reasons?
Ahmed MiladSr. maintenance engineer - Egypt
2004
A. I can think of several reasons that could possibly cause the zinc to flake off. More information may be needed to help diagnose your particular problem. Without knowing how severe the adhesion problem is, or if it is flaking off while it is in the line, or during the adhesion test, some ideas could be:
1. Improper cleaning prior to the furnace could be a cause, especially if the strip is oily. More heat in the direct fired section could help in this area.
2. The atmosphere in the furnace could need adjusted (more hydrogen possibly).
3. The strip temperature going into the bath could be too low.
- Terre Haute, Indiana, USA
2004
December 12, 2011
A. There can be several reasons for the peeling. It's all hit and trial method to reach at the root cause. But you need to analyse the samples first. Put the sample into 30% HCl solution for a minute or two to check the surface under coating.
1. If you see under surface bright and white enough after removing the Zinc coating it means the strip is not oxidized and ok for coating in this condition; you need to put attention on pot bath chemistry and CRC composition. May be silicon and carbon more in your CRC.
2. If you see the under surface black after removing the zinc coat it means you need to attend the furnace parameters. The strip is getting oxidized before coating which is like a cancer for the galvanizing.
a. First thing is to check all manholes gaskets and sealing using leak detector; please check the cleaning of strip.
b. Check for furnace leakages.
c. Pressure testing needed for all zones of furnace.
d. Check for any water leakages (hearth rolls, jet cooling blowers, water cooled damper, entry seal jackets).
e. Your dew point in furnace will indicate the water presence.
f. Check the Nitrogen & Hydrogen dew point and purity (PPM).
g. Need to check the flames of direct fired zones (try to adjust the air/fuel ratio depending upon your fuel whether CNG or LPG).
h. Take trial by running at low air/fuel ratio.
i. Sometimes snout shoe may have leakage which is hardly visible, so take the trial by running the line at high zinc bath level and see the result (if no peeling at high bath level and peeling starts at low bath level it means certainly your snout shoe leaking).
j. At extreme condition you need to do pressure testing of radiant tubes and heat exchangers.
k. High zinc coating also leads to adherence problem.
l. Aluminium % also needs to be checked.
- Bokaro Steel City, India
Snout Leakage in Galvanizing
November 20, 2013Q. Dear Experts
Snout is one of the most important parts in Hot-Dip galvanizing.
So we have to control the situation of the atmosphere during process.
However, sometimes because of leakage, the atmosphere becomes out of control.
Now, if you let me I would like to ask you:
1-Have you ever had any experiences about Snout leakage?
2-How could you realize the Snout leakage?
3-How does this problem affect the quality of your products (specially about black spot)?
4-And finally, how could you resolve this problem?
- Iran
Multiple threads merged: please forgive chronology errors and repetition 🙂
Q. I am process engineer responsible for continuous galvanizing line, we have great problem of peeling on our galvanized products , what are the different variables we should check to discover the reason of this defect , what are the effect of different impurities element on the zinc path on peeling and what are their limits .
Mohamed Farag AttiaKandil Steel Company - 10th of ramadan, Cairo, Egypt
2006
Sir:
If your line is a flux line it is possible that I could help. If it is not, I do not have sufficient experience in gas lines to be of value to you.
Regards,
Galvanizing Consultant - Hot Springs, South Dakota, USA
Zinc peeling observed in zero spangle bath
2006Q. I am Pramod Kumar Sinha a Process Engineer in Continuous Galvanizing Line in Cairo /Egypt. I am facing zinc peeling problem in new galvanizing line.
When we create new bath of zero spangle (Pb-0.005%) after galvanizing we face peeling above 140 gsm coating. But when we change the bath with normal spangle (old prepared & used from 6 month) we face no problem and found good adherence up to 360 gsm. I am not getting what is the reason behind it. Details of bath analysis is like this:
Al Fe Pb Result Remarks 0.63 0.04 0.005 Poor New bath adherence prepared 0.52 0.013 0.011 Poor Ditto adherence 0.453 0.011 0.006 Poor Ditto adherence 0.292 0.012 0.003 Poor Ditto adherence 0.24 0.012 0.003 Poor Ditto adherence 0.22 0.007 0.054 Ok at 360 GSM Bath change and continuous from zero to in all coating normal spangle
Pramod Kumar Sinha
- 10th of Ramadan , Cairo, Egypt
A. Hi
I think too much Al% in zinc pot will reduce adherence you have to pay attention to your speed it means the remaining time in zinc pot
msco - Isfahan, Iran
2006
2006
Q. What are the characteristics/bath composition which define/differentiate zero and normal spangle bath?
Atul MishraERW pipes - Maharashtra, India
Multiple threads merged: please forgive chronology errors and repetition 🙂
How to overcome zinc peel off in Galvanizing?
Q. We are facing a problem of zinc peel off in continuous galvanizing line. It is not a continuous one but occurs sometimes. Still we are unable to find the root cause, please help me to overcome this problem permanently.
VijaykumarPlating shop employee - Mumbai, Maharashtra, India
2006
A. Hi
I think in this line [it is common to have] peeling; pay attention to your cleaning condition and Al% in zinc pot.
- Isfahan, Iran
2006
Multiple threads merged: please forgive chronology errors and repetition 🙂
Peeling problems in Hot Dip continuous galvanizing Non-Ox furnace
2006Q. Dear Sir,
We have serious peeling problems in our plant. We had been suggested that the main reason is leakages; we have plugged all leakages. The ratio of fuel to air is also a recommended oxidising in the first 2 zones and reducing in the other 2 zones.
The plant was working good with zero spangle but after we changed the zinc bath for minimum spangle the problem of peeling resurfaced.
We have checked all leakages and it has been arrested; the percentage of Al is 0.20 to 0.26%.
Now please, if any person can help us in solving the problem.
What can be the possible cause of peeling after change over of Zinc bath from zero to minimum spangle?
As we were getting 350 gm/m2 with zero spangle and after changing the zinc bath, there was peeling from minimum thickness also .
The bath chemistry was found to be with in the standard prescribed requirement.
We do galvanizing of FH and HR coils, The coating is 90 gm/m2 to 350 gm/m2.
The thickness range is from 0.18 to 1.5 mm.
steel complex - Cairo, Egypt
A. Without giving the details on what you did during change over of Zinc bath (or) what was the real change during mini spangle to zero spangle, it is difficult to fix the problem.The problem may be with oil in CR coil or with furnace temperature too.
S.K.Subramanian- Chittagong, Bangladesh
2006
Q. We have not done any change in the Pot , we have 2 different pots for Regular and zero spangle, and I would like to bring to your notice after I changed the Pot the zinc peeling problem disappeared.
Dilipkumar Singh [returning]- Cairo
2006
A. Composition of zinc and its alloys may be changed. Go through leakages, furnace parameters, N2H2 gas quality, etc to be analysed.
G Nataraju- India
May 30, 2008
A. Please check the oil in CR coil; if oil contaminant is high then keep more temperature in first two zones. Check the dew point in furnace, increase aluminium % up to 0.30, check the pressure of lpg and air and its ratio.
PRABHAKAR WADIBHASME- Nagpur, M.S. India
September 19, 2008
A. I understand that you have two zinc baths ... let me know the pot equipment details, i.e., roll dia. & center distance of roll at X & Y axis ... furnace & other process section is okay.
Just you have to focus on bathe chemistry and pot equipment, i.e., roll sizes, etc.
Regards
- Guwhatati Inida
July 19, 2014
Is lead content the cause of lack of adhesion in continuous galvanizing?
Q. Is lead the culprit for delayed adhesion failure in continuous galvanizing? We use 0.08 max. in Zinc bath. Commercial quality coil shows failure in adhesion during forming.
Seen SEM structures, inter spanugular opening observed in skinpassed material.
- MUMBAI MAHARASHTRA India
February 27, 2014
Galvanized coating is peeling off of wire
September 16, 2019Q. Dear Sir,
We are having a problem about galvanized steel wire in 1.80 mm diameter. Wire is used for C-ring production and packed in 500 kg spool. One spool has no problem but on other spool coating is peeling. Both spool wires produced at the same time in same conditions. Zinc sticks on the part of machine.
- TURKEY

Q, A, or Comment on THIS thread -or- Start a NEW Thread